A new Quality Recycling Process (QRP) for flexible packaging, from CEFLEX (a consortium of European firms working on flexible packaging recycling) and its stakeholders, appears to demonstrate the viability of high value applications for recycled polymers from a mechanical recycling process.
CEFLEX says the breakthrough process has been developed in the consortium’s Sustainable End Markets workstream. “We have reached a milestone through the power of value chain collaboration and expertise in waste management of flexible packaging,” said Dana Mosora, workstream lead. “Our trials have shown good yields and delivered recyclate quality suitable to replace virgin polymer grades in a number of demanding film and flexible packaging applications.”
The CEFLEX stakeholder team set out to deliver commercial quantities of Polyethylene (PE) and Polypropylene (PP) film quality recyclates for a range of non-food flexible packaging markets not currently open to household collected post-consumer flexible recyclates. With this milestone reached, the CEFLEX workstream is planning industrial trials to underpin the business case for investment in infrastructure which can leverage the QRP into a mainstream solution.
A new ebooklet explores and profiles the process from several perspectives and gives insights from participants in the dedicated action team, which has rigorously tested its potential.
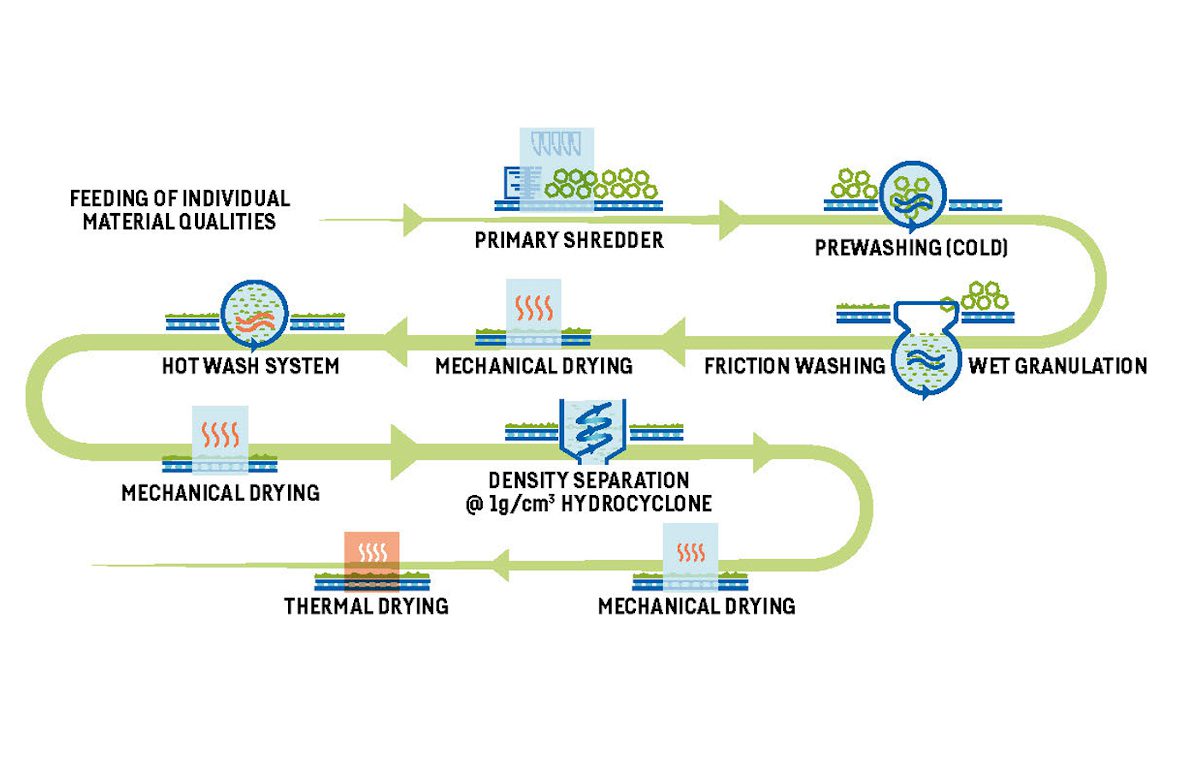
Gareth Callan, PepsiCo Sustainability Packaging Manager, R&D, gave a brand owner perspective, “A circular future for flexible packaging is only achievable through collaboration across industries and that’s what the Quality Recycling Process is enabling. Sorting and reprocessing lies at the heart of the challenge. We need new technology that unlocks value at scale so that recycling of flexible packaging can become more economically feasible.”
Monica Battistella, Product Manager and Sustainability Advisor at Taghleef Industries commented, “Many applications are possible if we could just understand that recycled plastic does not need to look perfect, just like recycled paper and cardboard are not – and then we would see the higher value that it has in simply being good for the planet. I believe consumers have already understood this.”
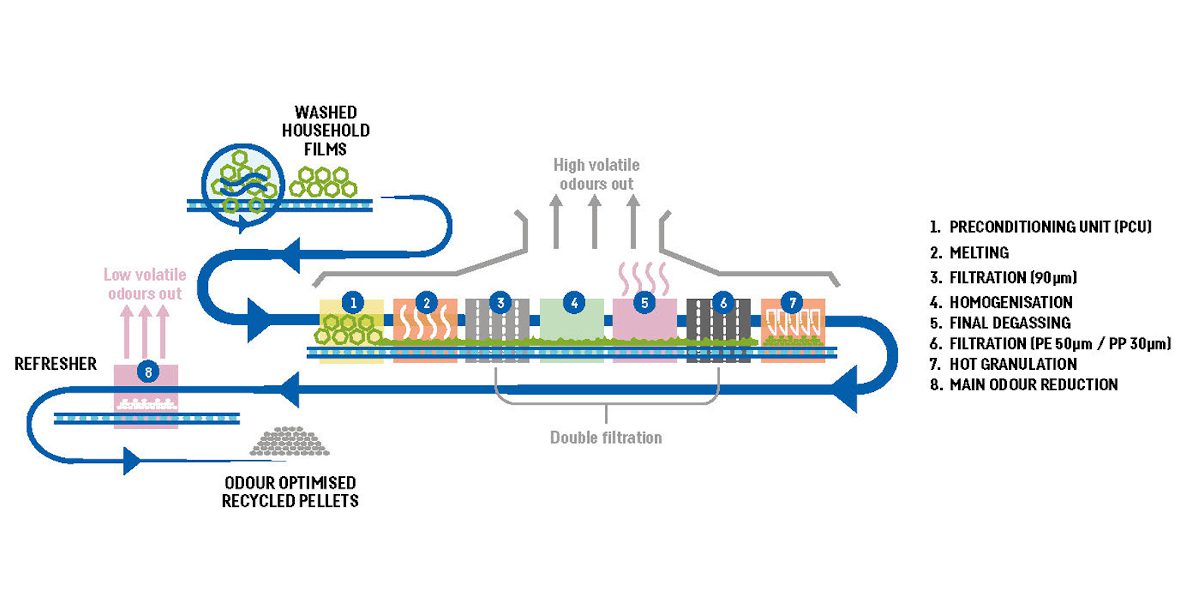
Berry Bellert, Sales Engineer & Development, Plastics Recycling at Dutch environmental company Atterro added, “It is not a matter if we can, it is more a matter of justifying the investment to do it. We have to realise that sorting flexibles is much more complex than sorting rigid packaging but it can be done!” He praised CEFLEX’s Sustainable End Markets workstream as it has already proved that, technically, it is possible to recycle PP film into non-food film applications and a good start to build the business case for investment.
Consult the e-booklet for a range of perspectives and experiences about boosting value and keeping materials in the economy: https://ceflex.eu/resources/