Coal-fired, energy-from-waste (EfW) and steel plants use lime to remove sulphur dioxide (SO2) from their flue gas output, as do oil and gas refineries. This process requires pumps that can work with such highly corrosive material, as Wilfried Staijen, a mining and pump specialist with Bredel Hose Pumps, explains
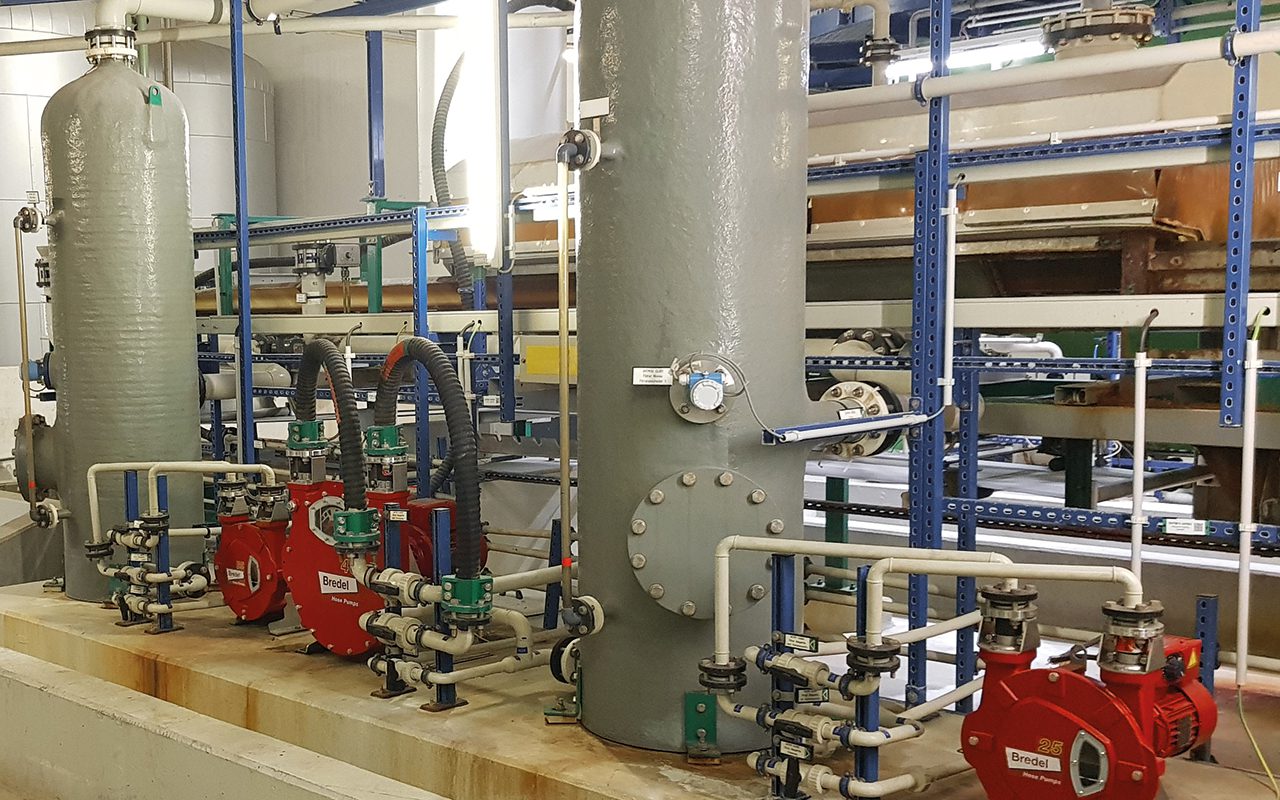
Although highly effective, the abrasive nature of lime presents a problem for the dosing pumps employed for this purpose. Many facilities using centrifugal pumps, for example, have experienced recurring problems with seal failures, leading to excessive maintenance and repair costs. The solution to this issue for a growing number of energy plants is peristaltic hose pumps, such as the Bredel range from Watson-Marlow Fluid Technology Group (WMFTG).
A recent case in point has seen the adoption of eight such pumps as part of a flue gas
desulphurisation (FGD) process at a European EfW plant. Used for dosing abrasive limestone slurry, the Bredel pumps are helping the facility gain greater control over its processes and reduce OPEX (operational expenditure) costs.
Why lime?
According to the British Lime Association, lime plays a key role in many air pollution control applications, and is particularly effective in the removal of acidic gases like SO2 and hydrogen chloride (HCl) from flue gases. In fact, efficiencies are usually in the range of 95-99%.
The use of lime in all three main flue gas treatment processes – dry, semi-dry and wet – shows its flexibility and adaptability as a global flue gas treatment. Calcium oxide (CaO, or quicklime), calcium hydroxide (Ca(OH)2, or hydrated lime) and calcium carbonate (CaCO3, or limestone or chalk), can all be used to neutralise acidic gases and remove SO2 from flue gases. This process helps to ensure that plants comply with both local and international environmental legislation for emissions.
In short, lime is the most cost effective and versatile alkali that can be used for flue gas treatment, with less dosage and lower waste production when compared with other reagents. For this reason, mineral lime reagents are used in abatement techniques at more than 85% of UK sites that treat flue gas.
Demand tracks EfW growth
The number of EfW plants in the UK has seen a marked increase since 2013. This trend is expected to continue until at least 2023 as the government targets a reduction in the landfilling of household and commercial waste, and looks to encourage more recycling and use of EfW.
The growing popularity of FGD is visible in many parts of the world. In all locations, lime-based products can provide a cost-effective, efficient solution in the treatment of flue gases generated from the energy recovery process, in turn reducing the volume of waste sent to landfill. A further benefit of FGD is the creation of high grade by-products, such as gypsum, which is sold commercially for use in plasterboard manufacture and a variety of other industrial processes.
Types of flue gas treatment
A variety of flue gas abatement techniques are in use today, each designed to suit particular applications. Dry scrubbing, for example, can be achieved using low-temperature dry injection. Here, hydrated lime is fluidised in air and injected directly into the exhaust ducting. In general applications, over 95% of SOx (sulphur oxide) can be removed, along with more than 99% of the HCl and over 95% of the HF (hydrogen fluoride).
High temperature dry injection is another type of dry scrubbing technique where hydrated lime is injected into the kiln at temperatures in excess of 850C. The hydrated lime decomposes within 30 milliseconds to produce a porous and very reactive form of quicklime. This process can reduce reagent consumption if combined with traditional, lower temperature alkali scrubbing processes.
When it comes to semi-dry scrubbing, calcium hydroxide in water (called milk of lime or sometimes liquid lime) is atomised at the top of a spray dryer chamber into hot flue gases of approximately 220C. The water in the milk of lime evaporates, cooling the gases (SO2 and SO3, together with any HCl/HF present), which dissolve and react with the lime. Semi-dry scrubbing is capable of removing up to 95% of SOx, and up to 99% of HCl and HF.

Pumps for wet scrubbing
However, it is wet scrubbing that is considered the principal flue gas abatement technique, where crushed limestone is added to water before the resulting alkaline reagent slurry is sprayed into a flue gas scrubber or tower. In a typical system, the gas to be cleaned enters the bottom of a cylinder-like tower and flows upwards through the limestone slurry spray.
An important aspect is the volume ratio of reagent slurry to flue gas, which is known as the L/G ratio. L/G ratios are usually 1:1 (litres of slurry to 1000Nm3 of flue gas) in wet scrubbing applications. It is in this application that reliable, high-performance pumps have a fundamental role to play.
It is acknowledged that wet scrubbing incurs high capital and operating costs due to the handling of the liquid reagent and the waste. However, it is still the preferred choice for many power plants due to the low cost of limestone and SO2 control efficiencies.
Abrasiveness challenge
During a site visit to a major EfW plant, running a 15-hour wet scrubbing operation, it was noted that centrifugal pumps were experiencing frequent failure when transferring abrasive lime slurry reagent. In such cases, the principal problem is that slurry entering the scrubbers is both high in temperature and contains up to 25% dry solid content. Adding to these challenging characteristics, the slurry crystallises as it cools.
Emissions from incinerators are under scrutiny, so they need to perform without any unpredictable downtime. Realising the requirement to change its pumps in the wet scrubbing process to meet stringent industry demands, the European EfW plant trialled Bredel hose pumps.
Such was their success in performing lime slurry transfer operations across a five-day duty cycle that the plant now employs eight Bredel pumps.
Protectively propelling
In Bredel hose pumps, which are both dry running and self-priming, the actual pumping principle is based on alternating compression and relaxation of the reinforced rubber hose, drawing content in and propelling product away from the pump. As a result, the fluid being transported is only in contact with the hose, making it ideal for handling aggressive or abrasive chemicals, such as lime.
Unlike centrifugal pumps or progressive cavity pumps that may be found in FGD processes, Bredel pumps are virtually maintenance-free as there are no expensive seals, valves, diaphragms, glands, rotors, stators or pistons to leak, clog, corrode or replace, leading to a much more controlled process and lower OPEX costs.
It should also be noted that the Bredel pumps include a unique rotor design which does not rely on the gearbox shaft. This protects the bearings of the gearbox from overloads which might occur in other hose pumps. With such a design, Bredel provides the guarantee of trouble-free and long lasting operation, even in heavy duty operations.
Peristaltic pumps are generally well equipped to cope with changes in things like viscosity, which is useful here as the slurry will tend to thicken as the process progresses and water evaporates. Likewise, they cope well with abrasive material.
Following the change from centrifugal pumps to peristaltic hose pumps, the EfW plant reported a more controlled operation and much improved OPEX costs.
On a typical basis, some 255,000 tonnes of waste are incinerated at the facility from a total of 1 million tonnes collected. This process leads to the generation of 139,000 MWh of electricity, around 35,000 MWh of which is used by the plant, with the remaining 104,000 MWh sent to the grid.
Ultimately, the success of the Bredel pumps is helping the plant continue these operations while maintaining its commitment to the environment.