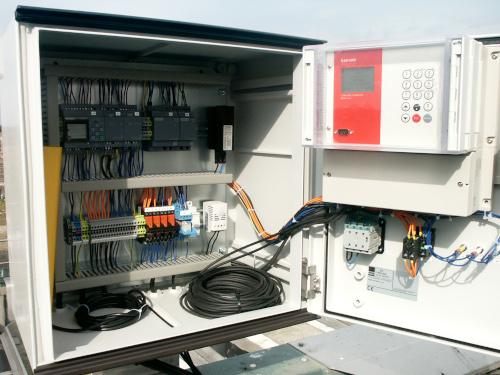
Ultrasonic flowmeter measures turbidity and flow for grit trap control at wastewater treatment plants, “reducing pump and scraper operation by up to 85%”
In classic three-stage wastewater treatment plants, grit and grease traps are indispensable as a process step in the first mechanical pre-treatment stage. In fact, anything that can lead to operational disturbances – and issues like wear or clogging – should be removed or filtered out at this stage. Sand, stones, glass, mineral solids and other impurities with grain sizes of 0.2 mm to 1 mm will settle to the bottom of the grit chamber, where they are removed using appropriate combinations of pump and scraper. The grit removal process is usually initiated on a timed sequence, and this means the process is often operating when it is not necessary, increasing wear and wasting energy.
Wastewater technology firm Technisches Büro Holger Pinta uses Katronic’s fixed ultrasonic flow measurement systems to detect turbidity due to sand build-up in sand-trap pressure lines, and uses the measurement to control pumping processes more efficiently.
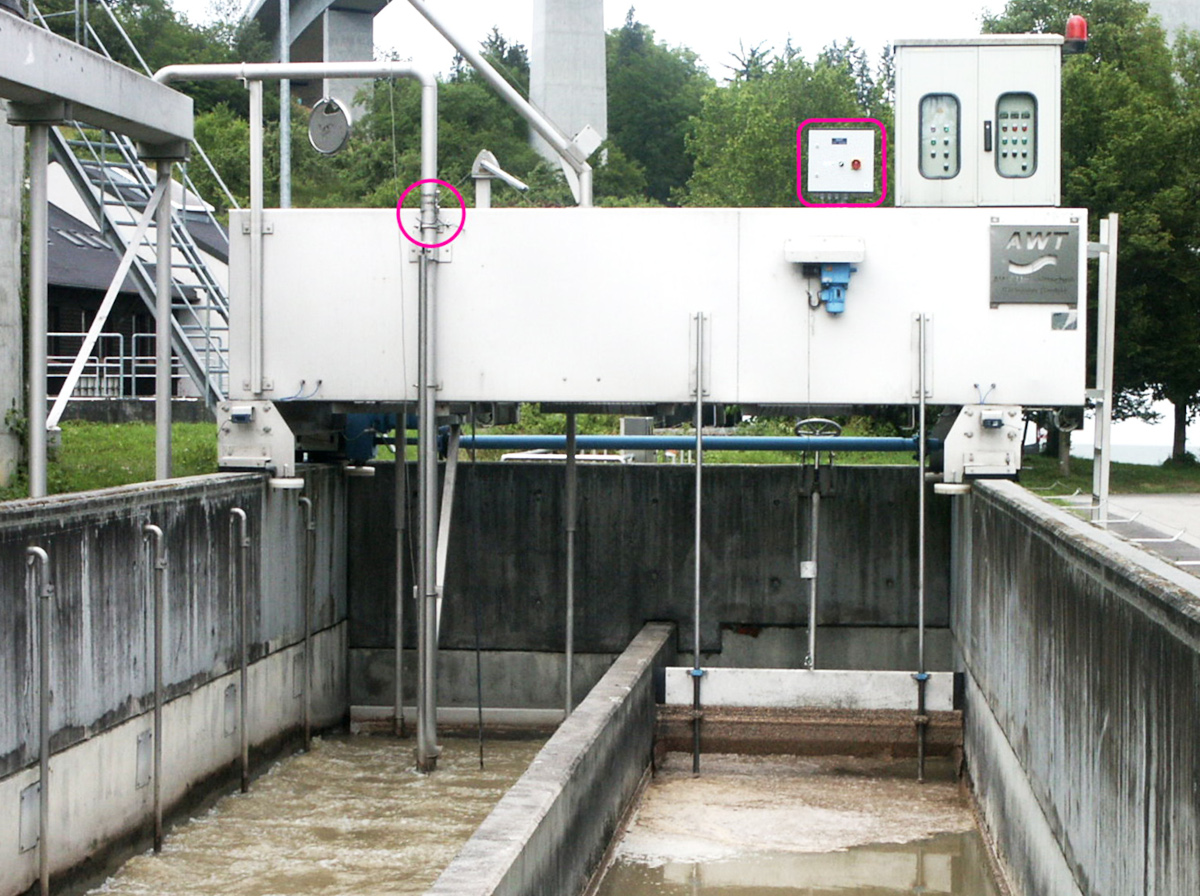
These permanently-installed, clamp-on transducers of the flow measurement units are used – normally – for flow measurement of liquids with low solids content. They detect turbidity due to sand via a mechanism whereby any sand in the line scatters an ultrasonic pulse, detectable as a reduction in the measured signal strength. Modelling has allowed the relationship between turbidity and the level of grit in the pressure line to be characterised in detail, and this means the grit pump and scraper can be initiated at an optimum point, reducing the required operating times of the sand trap pump and scraper by up to 85%. It is also possible to continuously monitor the pump delivery rate. Users who are more familiar with their process peaks can better control the energy input for their grit trap pumps and thus counteract component wear at an early stage.
Two ultrasonic sensors mounted on the sand-trap pressure line detect the turbidity non-invasively after the floating sludge pump is switched on. These are hard-wired to the Katronic transmitter and a 4-20mA signal (proportional to turbidity) is supplied to the central control system, which also takes weather information into consideration. The standard programme can be modified for each installation according to the specific conditions of the grit chamber.
The Katronic flowmeters installed on the pressure line fulfil a second function in wastewater treatment plants: Monitoring the flow rate. As soon as the flow rate permanently falls below an adjustable limit value (set to indicate wear on the impeller or clogging), a visual warning is given. This feature – developed by the Technisches Büro Holger Pinta – helps clarify what’s happening in grit chambers in wastewater treatment plants. Plant operators can not only control the pump and scraper more efficiently, but they have a continuous view of the process at any time, and a heads-up if there is a risk of wear with the pumps or the impeller, or if too much energy is being used.