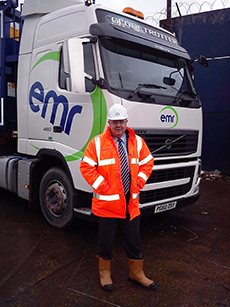
Mark Priestman, Managing Director of Non-Ferrous at EMR (formerly European Metal Recycling) writes
As the recycling industry innovates to embrace its role as a key player in the UK’s journey towards a more sustainable society, new challenges continue to emerge.
One challenge which EMR faces is how it handles a series of non-biodegradable chemicals found in some plastics which are categorised as Persistent Organic Pollutants (POPs). These chemicals break down slowly in the environment and can therefore end up in the food chain if not captured during the recycling process.
Last year, the Environment Agency made changes to the classification of waste plastic produced by the treatment of Waste Electrical and Electronic Equipment (WEEE). Following an industry investigation, some waste plastics, which are found in certain categories of WEEE, have now been classified as containing POPs.
This isn’t a change to the law, rather a greater focus on which items in our day to day lives contain substances that were not classified as problematic when the electrical items were made but which have now been identified as persistent pollutants.
The impact on EMR’s operations is – in some ways – profound. Separating the plastic from the copper in wire, for example, is already a complex process, requiring sophisticated technology but our modern, global economy means we can see cables coming from thousands of manufacturers via hundreds of countries arriving into our plants every day. Not all of these will contain POPs, so EMR is innovating to find methods to identify and separate these cables, processing them in a way that protects the environment while allowing plastics that do not contain POP’s to re-enter the recycling chain as the next generation of cars, construction products, traffic cones and more.
Unsurprisingly, this has increased costs for EMR, both in applying for the license variations to treat more challenging waste and operationally to separate out the POPs from the non-POPs containing material.
Of course, EMR’s reputation for excellence and responsible recycling means that we will always meet the demands of any regulations and, fortunately, these demands also create opportunities. During the past 10 years EMR has invested in its plastics recycling division (MBA Polymers), developing innovative ways to separate plastics via a range of processes. As this technology develops further, EMR can play a bigger role in ensuring even more of the plastic waste that the UK produces can be recycled.
It is worth asking why these chemicals are in our end of life products today. The answer – that these compounds were chosen at the time, to improve the safety or operating performance of the plastics where they were used. Scientists have only realised more recently that they create persistent pollution problems. These chemicals are now banned for use in new products and alternatives have been found, but of course they are still present in older products that reach end of life.
If the UK is to reach its goal of building a more sustainable and circular economy, it is issues such as these which will provide the greatest challenge and create the most need for innovation.
While EMR is working hard to meet these challenges, there should also be a role for manufacturers and government agencies – all of whom can help us sort, limit and eventually phase out these materials. The good news is that we’ve already overcome challenges like this before. For example we have transformed the way we recycle fridges to avoid the release of harmful CFCs into the environment.
Working together, EMR and the manufacturers of the products it recycles now share a new long-term responsibility, ensuring that POPs are kept out of the environment and our path towards a more sustainable economy can continue.