Design and manufacturing firm Celeros Flow Technology says it has resolved pump performance issues and increased operational life in a recent project with a major water customer.
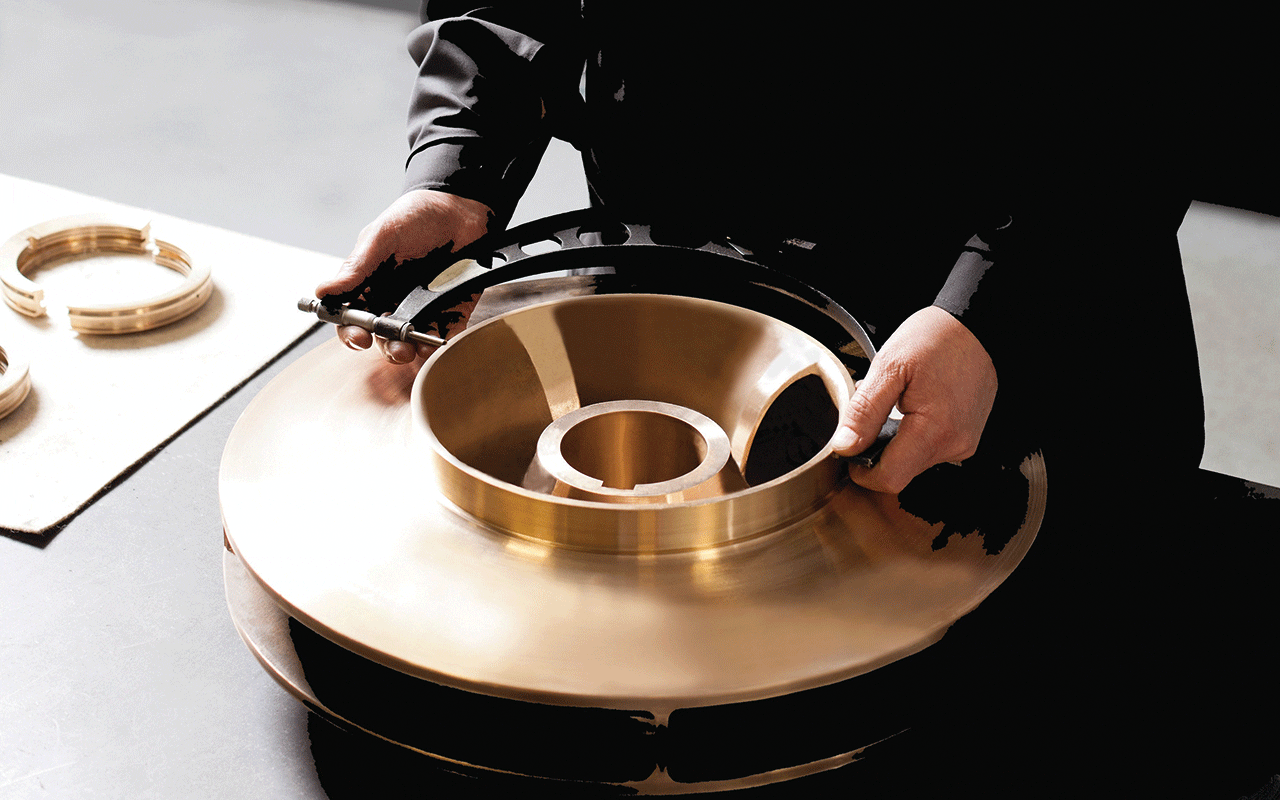
This project illustrates a situation where detective work has led to significantly improved performance with four BB1 pumps. A site investigation and subsequent materials upgrade has achieved a 50% increase in pump operational life and delivered major cost savings by dramatically reducing Mean Time Between Failures (MTBF).
Signs of a problem
The four Uniglide pumps in question had been in operation for approximately seven years but had not been subject to any serious maintenance in that time. The first indication of issues with the pumps was a drop in performance. The original pump manufacturer, ClydeUnion Pumps was invited to conduct a comprehensive health check of the pumps to determine the reason for their reduced performance.
“There are numerous reasons why pumps may run less efficiently than they should,” said Mike Golds, Global Upgrade and Rerate Programme Manager at Celeros FT. “These might include a change in process parameters or operational conditions; alterations in the operational environment, such as a change in temperature or humidity; general wear and tear caused by variants in the duty cycle, contaminant levels and so on; or a change in the properties of the fluid being pumped.

Finding a solution
Initial testing confirmed that the performance of the Uniglide pumps was significantly down on original design parameters. When the top half casing was removed, the Celeros FT team discovered that the impellers on all four pumps were badly damaged and the wear rings were severely worn.
“Upon investigating the root cause of the damage, we determined that the water supply tank often dropped to a low level, which resulted in cavitation occurring,” explained Mike Golds. Over time, this cavitation had caused holes to develop in the impeller inlet vanes on all four Uniglide pumps. From discussions with the customer it was apparent that the low tank levels could not be prevented, which meant that the impellers as originally specified would have to be replaced every six years.
This kind of upgrade schedule is costly. A better alternative is a materials upgrade and one that offers a more long-term solution in a case like this. CFT replaced the existing cast iron impellers with parts made of aluminium bronze (material BS 1400 AB2), which is more resistant to cavitation damage.
Celeros FT manufactured the new impellers at the ClydeUnion Pumps site, complete with new wear rings for the four pumps. The upgraded units were then reassembled and tested again to ensure they met performance requirements.
Replacing the impellers and fitting new wear rings on the Uniglide pumps achieved an immediate 6% increase in performance. Despite their exposure to cavitation, the new aluminium bronze impellers have a design life in excess of 15 years – more than doubling the Mean Time Between Failures (MTBF). The return on investment for this project was calculated to be within two years.