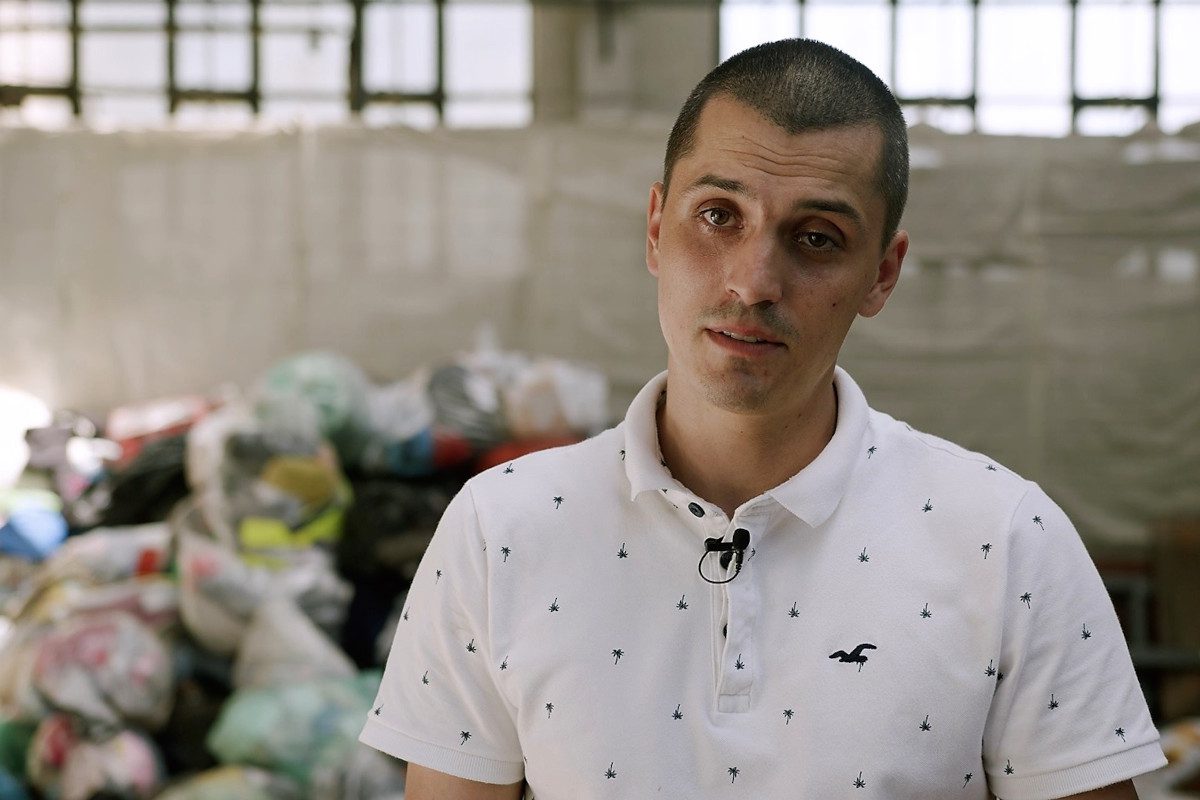
A textile waste collection company in Slovakia has published the results of a waste monitoring project using Sensoneo waste monitoring sensors, part of a system that supports dynamic and automated waste collection.
The firm, Ekocharita, annually collects approx. 3000 tonnes of textile waste. As of January 2021, Ekocharita began installing Sensoneo smart sensors to monitor the fill levels of their containers in real-time. By the end of June they had monitored 600 containers, and with data gained from the sensors, they seemingly managed to significantly improve the management of their operations by:
• decreasing the time required for the collection of 1 tonne of textile waste by 30 percent,
• reducing the waste collection cost by 20 percent,
• and making the logistics process smoother and better organized.
A spokeperson for the firm said they were now able to guarantee the daily collection of volumes needed for a smooth logistics process – “and it takes us fewer hours and less km than before.“
Textile waste is a stream that is still awaiting legislation to mandate separate collection. European law along these lines is expected to come into practice in 2025. Until then, the system is supported by private companies that manage the collection of discarded clothes, and ensure its reuse, recycling, and charity donation.
Ekocharita operates within an area of 16000 km2 and manages 1300 containers for clothes, shoes, toys, and home textiles. The containers are usually distributed in busy urban areas. The availability of textile waste containers in close proximity encourages citizens to sort the clothes properly.
What makes containers for textile waste unique is their very irregular filling cycles. The speed at which the containers become full is absolutely unpredictable, which makes collecting this waste difficult for operations and logistics, and puts high financial and time demands on managers. Real-time online monitoring of fill levels can significantly improve operations and reduce costs.
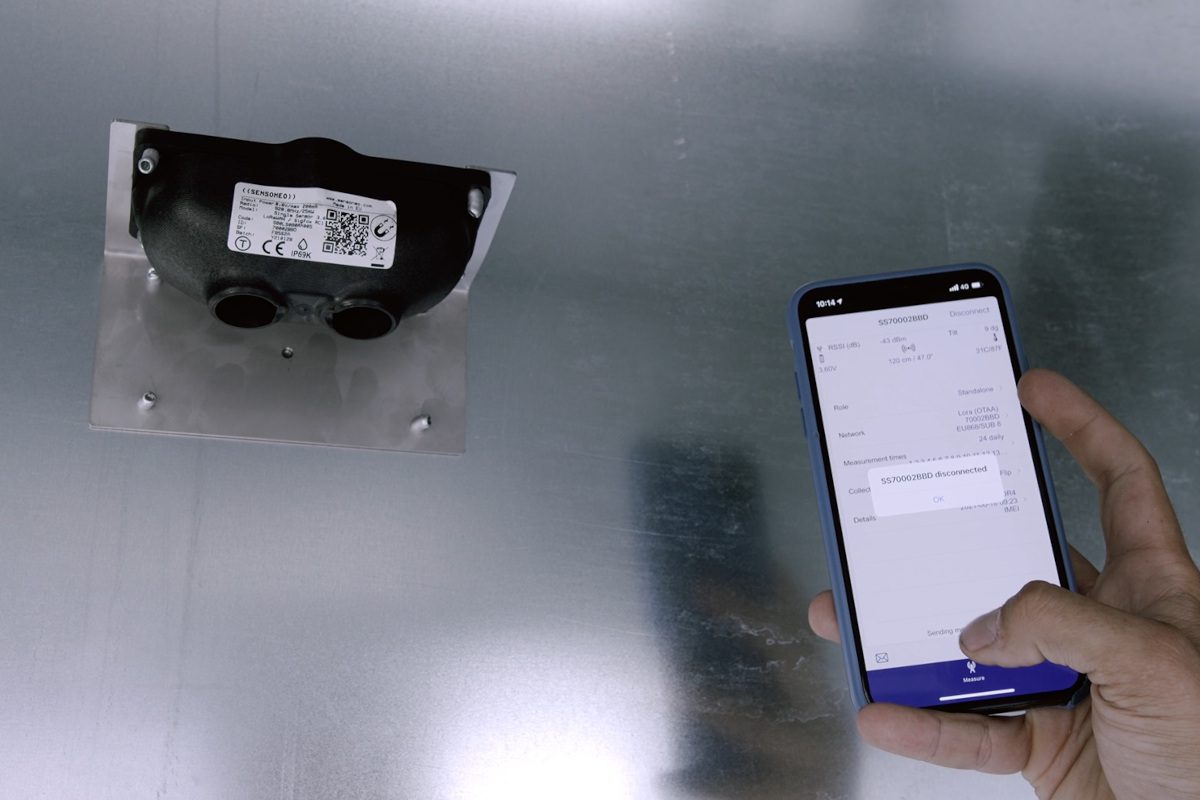
Implementation of waste monitoring sensors
Ekocharita began installing the sensors in January 2021 with the help of the EIC Accelerator grant that Sensoneo received for large-scale deployment of its solution, to help it establish the positive environmental, operational, and financial benefits of smart waste management.
The Sensoneo sensors use ultrasonic technology to monitor fill levels in containers 24 times a day. Along with this data, they also monitor temperature and provide fire and tilt alarms. For the data transfer, the company decided on the LoRaWAN IoT network. With every batch of installation, the positive impact on operations became more and more visible. “We have installed the sensors on our own, following a 2-hours training from Sensoneo, and we were surprised by how easy it was – it takes less than 5 minutes to install and set up the sensor,“ said Juraj Kunak, CEO and Founder of Ekocharita.
The drivers were originally opposed to the technology’s introduction, but became very proactive as they realized the actual positive affect to their workloads, said the firm. Juraj Kunak: “Even those who said that ‘I will not use it, I can’t do it with a smartphone’ are the first to open a smartphone at six in the morning, make 12 red dots along the way, and at 10:00 they are back with a full car.”
A complete change of operations
With smart waste monitoring on board, Ekocharita has seemingly completely redesigned the way it operates. The whole network is digitalized, and the drivers can easily and quickly identify the containers which really require pick-up, and so spend their time much more efficiently. “Right now, the driver wakes up in the morning, opens the app and can see the orange and the red dots – and that is exactly where he should go to quickly collect the full car – because that is the metric based on which the drivers are paid.”
Before the sensors, collection was based merely on the estimations of the drivers: “They were driving for 8-9 hours to collect a full car. They were running in circles and let’s say in 6 months the drivers were completely burnout. Now they can start at 7 or 8 and can be finished by 12:00 or by 1-2:00 PM and they can go back home to their families.”
“We know that 6 full cars are coming to the warehouse every single day.”
The ability to choose only the nearly-full containers for collection also allows Ekocharita to ensure they collect the volumes of material they need for easy and smooth warehouse management: “Before having sensors for example, 5 drivers would come full, but one driver would come empty. For one day, you can say it does not matter, but after 30 days you are missing let’s say 15 tons inside the warehouse, and that is the highest loss.”
On-time waste collection means the avoidance of overflowing bins, says the firm. Potential mess around bins and a dirty environment is a great obstacle for many business partners of Ekocharita.
“Having sensors means being reliable for the partner. That is why we are deploying more and more containers which are very near to us in shopping malls, schools, universities, kindergartens. New areas where I have not been before because there was another competitor. Now we are able to replace them.”
“Digitalization not only helped our operations – it also opened a brand new customer segment for us.“
Cost vs benefit calculation
Ekocharita was able to implement the solution as a result of the EIC Accelerator grant awarded to Sensoneo. The company has also calculated the corresponding ROI had they been required to make the investment themselves. And to do this, it used Sensoneo’s monthly “smart waste as a service” pricing. “If the purchase of the sensors had been fully on us, we would have received the ROI in 7 months,” said Juraj Kunak, CEO and Founder of Ekocharita.