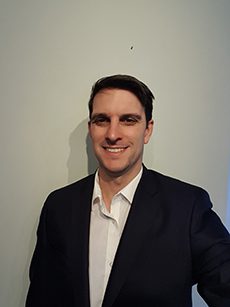
With the waste and recycling sector ranking the second highest for workplace death rates according to the HSE annual workplace fatality figures for 2020/21, and as recent incidents illustrate, there is clearly a need to raise awareness of the risks in this sector and share best practice advice. Will Rogers of Eco Verde Energy (EVE) shares insight into how AD plants specifically can provide a safer working environment for operators.
AD plants can be home to many dangerous working situations, such as the movement of operators and plant vehicles, exposure to dangerous gases, confined spaces, as well as the risk of fire and explosions.
Site managers and operators must be aware of the risks, as well as the policies and protocols in place, to protect anyone working on or visiting an AD site, from harm.
At EVE, we have recently reviewed the health and safety policy for all EVE-managed AD plants, to optimise worker safety. Addressing lone working has been a key element of this.
With lone working, it is not being alone which causes the danger, but the type of tasks carried out when there is nobody else on site.
Where possible, EVE’s policy is to avoid lone working but we understand that this isn’t always achievable on a site which operates 24 hours of the day, 365 days of the year.
Emergency call outs, staff absences and travelling between sites are all scenarios which give rise to potential lone working situations. This is why plant owners and operators need to use all tools and data available to them to reduce the risk to the individual where lone working could occur.
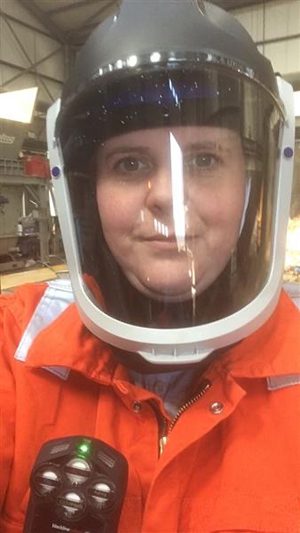
Adoption of a new technology
As part of their health and safety review, EVE has recently introduced the use of technology within the team to further support health and safety emergency protocols.
The G7 Lone Worker created by Blackline is a small device which employees attach to their uniform whilst they are working. The device monitors the area in which the worker is carrying out their duties, any exposure to dangerous gases and also provides quick access to emergency services when needed, among other functions.
It has a proximity detection feature to identify workers who have been in contact with one another. This feature is really useful in the case of a COVID-19 outbreak as it allows us to isolate the area where those infected have been and notify those who they have been in contact with.
The technology can detect when lone workers have had an impact fall, if they have been motionless for a period of time and when workers have failed to report to a compulsory check-in.
Being able to monitor our workers and what risks they are exposed to has been really beneficial for us and is why we, as a business, decided to invest in the kit to protect our staff.
Not only can we guarantee that if a lone worker was to need medical assistance, we would be alerted, but we can also use these devices to prevent future incidents from occurring by using the data which is captured by the device to support decision making around health and safety improvements.
Use of data
Taking a bigger picture approach, Rogers recognises the benefits having a device that captures so much data can offer to the company’s health and safety procedures.
We can use the data to create a map of each of our sites, indicating where the key areas of concern are and use this data to prevent future incidents from occurring.
The collected data can build a bigger picture of our sites and brings attention to areas where additional safety measures are needed, such as highlighting an area where the oxygen levels in the atmosphere are low.
We can then take action to fix the cause of the problem before harm occurs. This can be lifesaving, which is why health and safety reporting is so crucial.
The data which is collected is only accessible by the health and safety team and the site directors and is only used for the purpose of health and safety management.
Our operations teams have welcomed the technology and reported feeling safer at work since knowing there is a system of communication in place if something were to happen while lone working.
Set out a clear policy
Rogers highlights the need for a clear and robust lone working policy which all employees are aware of and understand. The policy should detail what is and what is not expected of workers, both alone and within company, the procedure in an emergency and how to report any issues that arise during a shift.
It’s important to ensure there are no blurred lines in the rules. The policy needs to be clear and concise to avoid any misunderstandings among the team,” explains Rogers.
We all need to be singing from the same hymn sheet. That includes me as health and safety director, right through to the teams who operate the AD plant. A lack of understanding can have severe consequences.
In addition, ensuring health and safety training for employees is continually provided is essential.
At EVE, employees are regularly provided with refresher training so they are aware of the most up to date procedures when it comes to health and safety when working alone or as part of a team.”
Hierarchy of control
Approaching every scenario using a hierarchy of control is a method which all AD plants should be using when assessing risk. This method considers a hazard and how best to reduce the risk of harm to the operatives. It then follows a hierarchical structure which is most effective from the top of the hierarchy, to the least effective at the bottom, as after PPE, there is no further layer of safety for the operator.
“We would first consider whether there are any alternative options to avoid lone working such as allocating the job to two workers instead of one, by ensuring the task can be undertaken in the sites core hours if not, due to say an emergency breakdown or out of hours call out, and the nature of the work didn’t involve high risk tasks, such as confined space entry, we would look at engineering control measures to minimise the risk , coupled with a robust set of rules for all operatives to follow as part of our safe system of work and finally, ensuring that the correct PPE and safety devices are worn by all workers,” explains Rogers.