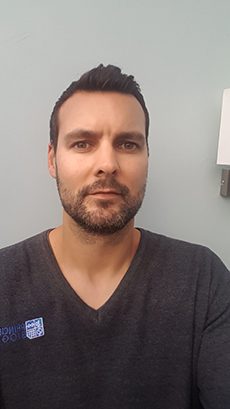
From developing a small-scale on-farm digester to a large biomethane facility, embarking on a new anaerobic digestion project can be a daunting prospect. A comprehensive design phase to determine the most successful layout for a site can reduce the risk, ensuring your plant remains profitable for years to come. Steven Cotterill of Anaergia UK presents “four design cornerstones to set your AD project on the path to success”…
1. Follow the process flow
At a well-designed AD facility, process dictates positioning. In so far as the site footprint will allow, design the layout of your plant to follow the flow of material. This will enable feedstock to be pumped or conveyed over the shortest distance possible, reducing the likelihood of downtime from blockages and lessening wear and tear on feed equipment, process pumps, macerators and conveyors.
This design principle can be applied across the whole site. A compact layout is more cost-effective, as a smaller footprint means less land, less concrete and less labour will be required to build the plant. However, make sure to factor enough space into your design for landscaping, planting and shielding, which are often required by planners.
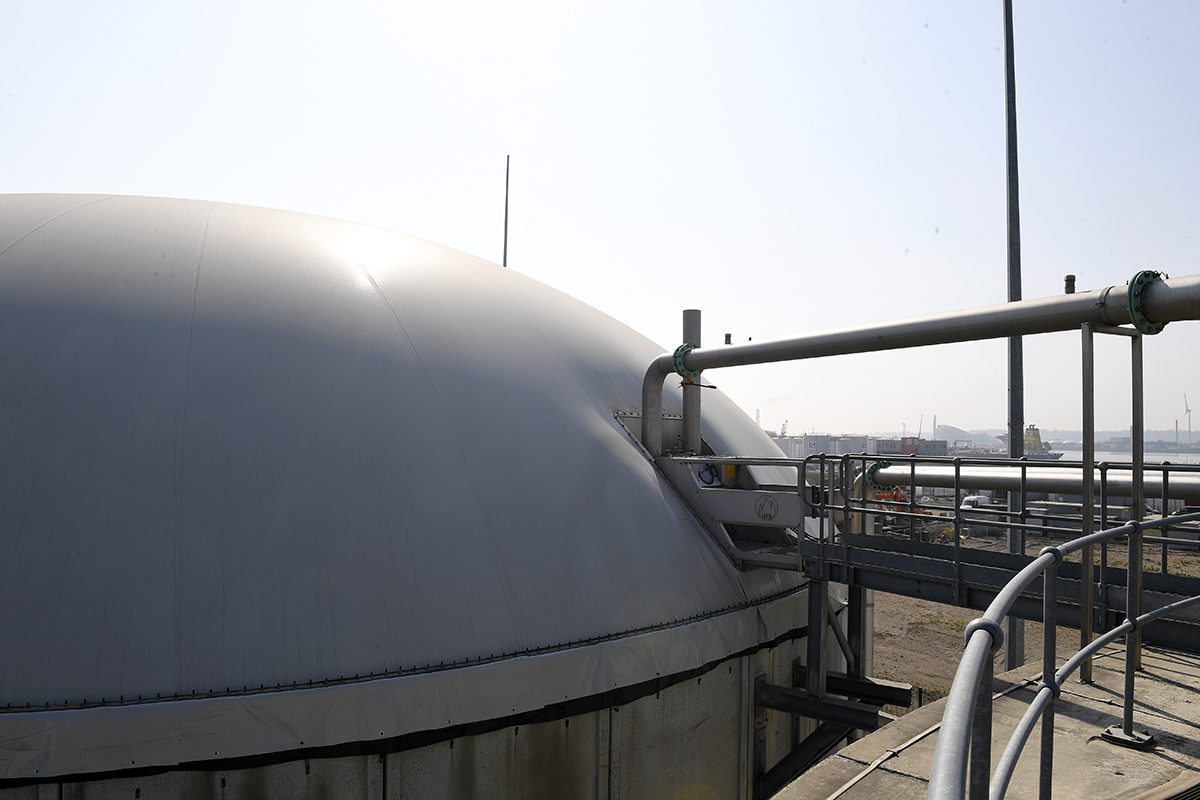
2. Enable easy access to equipment
Maintenance is vital for successful AD operation, so ensure that forklift trucks, small vehicles or lifting machinery can easily access key equipment such as tanks, pumps and mixers. This will give service engineers the flexibility to quickly remove, repair and if necessary, replace parts and equipment, reducing downtime.
Ensure that high level equipment can be easily reached via steps or access ladders with a sufficient platform for working, or that there is room for a cherry picker or scissor lift. If the plant has a flexible membrane roof, you will also need to allow access for cranes, as the lifetime of the membrane is shorter than the subsidised life of UK AD plants and it will need replacing.
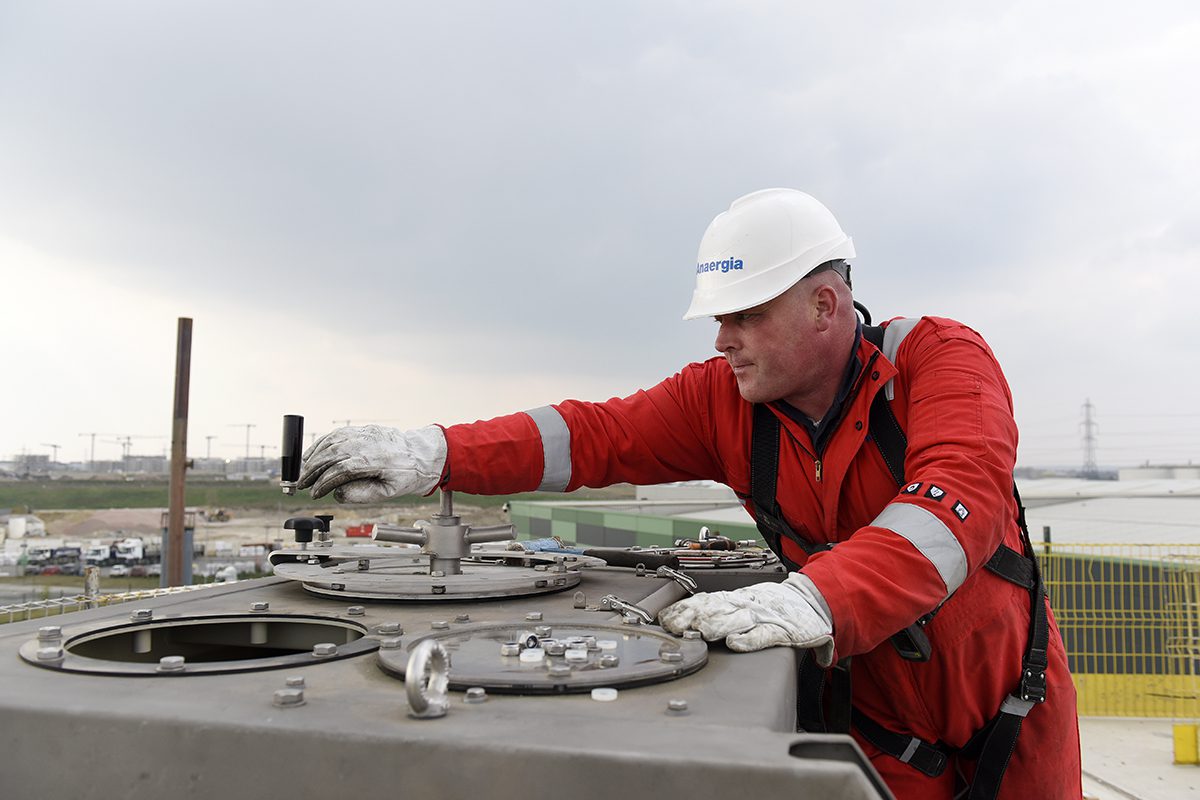
Finally, consider DSEAR (Dangerous Substances and Explosive Atmospheres Regulations). Avoid siting equipment that will need regular maintenance within a DSEAR zone, to reduce the time that operatives will spend in this high-risk area.
3. Protect your people
The health and safety of site operatives and visitors is paramount and, as stated above, full consideration to DSEAR and HAZOP (Hazard and Operability Study) must be followed. The potential for explosive atmosphere increases near to pressure relief valves, as these are a final safety measure of biogas release should the flare fail to light when excess biogas is not being consumed. Therefore, as well as siting key process equipment away from ATEX-zoned areas, try to avoid locating any electrical equipment or instrumentation within the biogas release zone. If this is not possible, then ensure that equipment or instrumentation are correctly ATEX-rated.
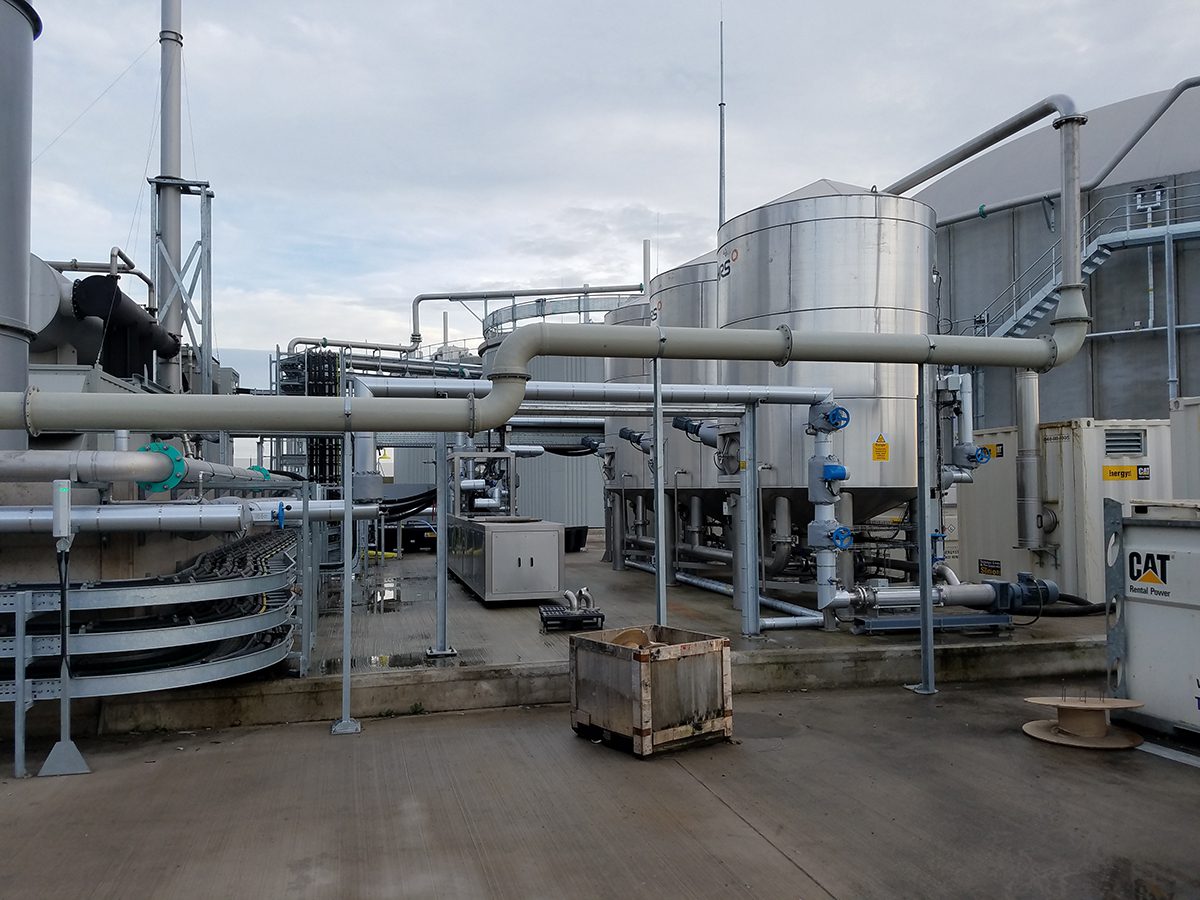
Establish clear personnel routes throughout the facility. Inside the reception building, provide designated walkways for operatives to follow, as well as barriers and/or handrails to protect people from tipping vehicles and bucket loaders. Arrange process pumps and associated pipework away from walkways to avoid trip hazards and consider placing pipe runs and electric cables above head height on support frames to keep floors clear for access.
Take into account the maximum number of personnel that could be on site at any one time and ensure there are adequate facilities available. In the unlikely event that operatives come into contact with large quantities of digestate or feedstock, it is important to make sure that the site includes good washing facilities and toilets in both clean and dirty areas. Showers, changing rooms, laundry rooms and a sufficient-sized mess room for operatives and contractors are also essential.
4. Take care of transport
When designing your AD facility, consider vehicle movements in and out of the site, as well as within the site boundary. A traffic management plan is a good starting point and depending on the number of vehicles expected on site, a traffic light system may also be required.
Locate the weighbridge as close to the operations office as possible to enable efficient communication between drivers and site personnel. If the weighbridge needs to be located further away, then ensure there is a serviceable automated ticketing system.
Make certain there is enough turning and reversing space for vehicles delivering feedstock or collecting digestate. If delivery vehicles are tipping into a reception building, it should be high enough to accommodate the bulk trailer at full tipping height.
Factor in enough parking spaces to accommodate all staff and contractors and situate car parks as close to the reception as possible. This will ensure that new personnel arriving on site can easily and safely get to reception prior to signing in and being inducted.
Finally, ensure that the bund size is adequate (110% of the largest vessel or 25% of total tank volume, whichever is higher) and that vehicles can easily access it, whether via a ramp or flood gate.
To conclude, a comprehensive site design coupled with strong 2D and 3D concept artworks can help developers to visualise their proposed AD plant and correct any potential layout issues before building works commence, saving both time and money. For expert AD design and layout advice, contact ukoffice@anaergia.com