It’s still a widely used method of detecting gas leaks, but now seems inefficient given its reliance on outdated technology. Martyn Hanks of instrumentation firm QED Environmental outlines the problems and offers what he suggests is a tried and tested alternative for large gas networks.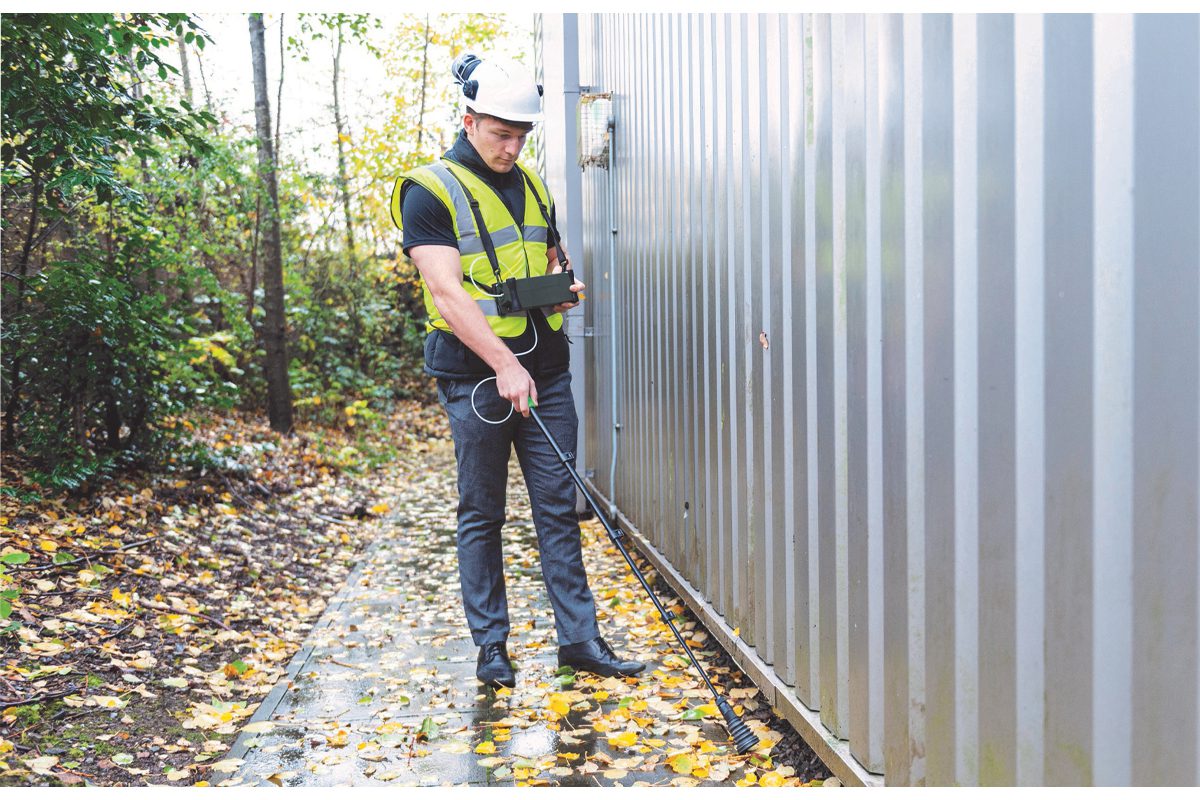
Most consumers across the world are supplied with gas via local distribution networks which vary in size depending on the country. In the UK there is 280,000 kilometres of pipework; in France 170,000 kilometres and in the US over 3 million kilometres.
In short, in most countries there is an enormous amount of pipework that needs monitoring, repairing and maintaining in order to maintain efficiency of distribution and, more importantly, safety. Often, as in the UK, a large amount of the gas pipe is of the cast iron type that is subject to corrosion, water infiltration and is in need of regular repair.
And, of course, surveying for leaks is not a once-a-decade job. Depending on individual national regulations, surveys can be twice-yearly or in the case of the UK and France four times every year. That is enormous amount of manpower charged with finding gas leaks.
The most widely used method of detection is the line walker, equipped with either gas sensing equipment or a vehicle-based surveying solution. Once a leak or flute is detected, the distribution network operators (DNOs) want to limit excavation, which normally involves disruption to gas supplies and often road closures. What’s more, the penalties for over-running on repairs are often costly.
And yet, the technology to find and accurately locate the source of gas leaks remains unresponsive to the demands of the application.
There are multiple methods of detection currently being used, from infra-red and laser infra-red, through to semi-conductors and electromechanical sensors. However, the predominant instrument is the flame ionisation detector (FID) which necessitates the line walker to carry equipment that detects gas leaks by using a flame to ionise organic compounds containing carbon.
There are multiple issues involved with this method, most notably the response time which is slow compared to other methods. The average person can walk circa 26-27 metres in 20 seconds, which is the reaction time of the FID. This means that the line walker can be significantly past the area of the leak when the FID alarms. The line walker then has to double back and narrow down exactly where the leak is coming from. All of this takes time and has a cost.
Other methods are not much better. Gas imaging camera response times vary, whilst infra-red (IR) can be more than 10 seconds. Semi-conductors (SC) typically have a response time of more than six seconds, whilst a combined SC/IR solution also has a response time of more than 10 seconds.
Once a leak is detected the next stage is pre-localisation, which involves drilling small bar holes into the road and inserting bell or carpet probes to measure the methane levels. The issue here is that methane follows the path of least resistance and the source of the leak in the pipe may be significantly different from where it comes to the surface. Ultimately, the longer it takes to find the source, the higher the overall cost will be.
A second issue is calibration, with equipment currently in use having to be recalibrated daily. This downtime is exacerbated by the need to regularly recharge the battery, which further cuts operating time in the field.
For the operator, the equipment is often bulky, weighing up to six kilograms. While this may not sound like much, it must be remembered that a line walker could be walking several kilometres a day as part of his job.
A final issue is false readings. In urban areas the current technology has a tendency to pick up other hydrocarbon gases often emitted from vehicles. Again, false readings add to time and cost.
Laser absorption spectroscopy technology provides a solution for many of the issues currently impacting gas detection. It offers all the advantages of optical detection in a highly compact and lightweight portable device.
Crucially, this type of equipment is selective to methane only, and avoids any cross-gas effects from other hydrocarbons present. This results in much higher sensitivity, with the Huberg Laser One, for example, able to detect leaks at levels as low as three parts-per-million.
In operation, laser technology is also more accurate in determining the source of a leak. The Laser One is able to take a reading every second and has a response time of <2.5 seconds, which means that it is much quicker to identify the exact location of a flute.
A number of major European gas companies are already using this technology. These companies are finding that close identification of the source of the leak in the pipe lets them carry out fast and cost-effective ground excavation, minimising disruption to local communities.
Ultimately, there can be little doubt that the gas leak detection industry has long been in need of innovation to truly deliver tangible and scalable change. Laser absorption spectroscopy is that innovation. The emergence of new technology such as laser optics can deliver a step-change in identification and remediation cost savings for gas companies, while also significantly improving the working conditions of their employees.
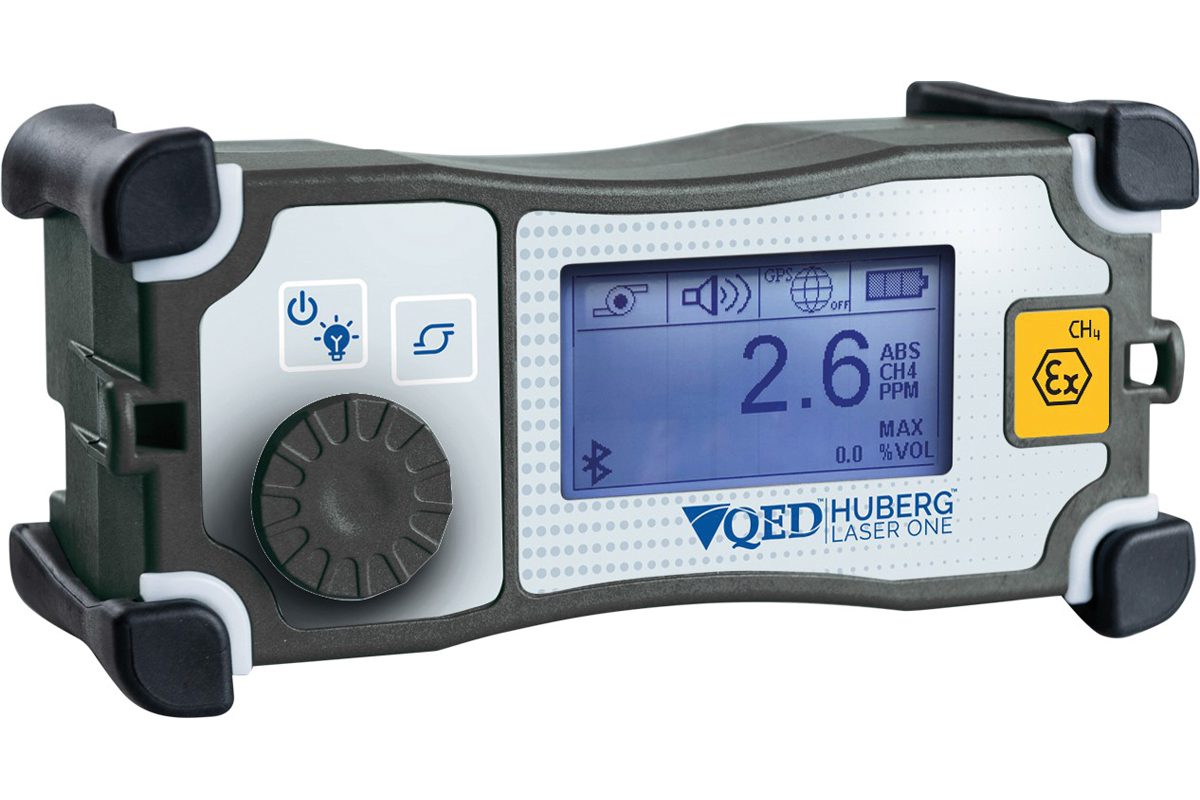