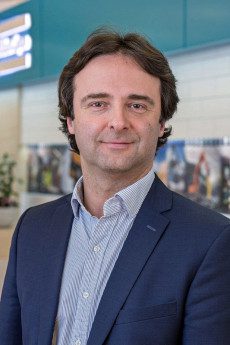
Mitigating higher energy prices: how we can help reduce energy costs for running compressed air equipment and keep manufacturers competitive? Alexander Pavlov of Atlas Copco Compressors offers a few thoughts.
We have to accept there is no short-term solution to mitigate soaring energy prices that have trebled in recent times − we have heard from customers who are now paying 24p/kWhr or as much as 40p/kWhr for electricity, whereas it was only about 10p/kWhr last year. This unprecedented level of running cost increases over a period of just a few months inevitably impacts on manufacturers’ end product price structures and their competitive ability.
As a global supplier of compressed air systems to industry we strive to offer our customers the best value in sustainable technology that is designed from the outset to aid their productivity. That is why we are able to offer the assurance that there are ways to assist in reducing these costs and to increase productivity to offset the financial burden.
Apart from negotiating more favourable new energy supplier contracts, industrial consumers will need to look to their operational efficiencies to help reduce the impact of rising energy prices. If they can invest in the most energy efficient equipment, avoid unplanned downtime with proactive preventive maintenance, optimise operational performance, review the power demands of production processes, this effective energy management and monitoring strategy will help to reduce energy bills.
Moreover, electricity consumption can be reduced by carrying out even the most basic tasks, such as switching off the compressors during non-production periods. And of course, everyone should start with air leak detection audits and fixing those leaks.
Energy efficiency is key. Government sources claim that applying effective energy efficiency techniques could save more than one-fifth of projected manufacturing energy demand, but there are significant barriers to that achievement, such as lack of operator knowledge and limited investment budgets.
This is where help is available from Atlas Copco with practical measures and advice on saving energy, such as the application of VSDS compressor technology that can realise as much as 60% of energy consumption, or the substantial benefits of heat recovery systems, and cost-reduction opportunities revealed by conducting energy audits. We echo the British Compressed Air Society which is calling for UK businesses to take simple steps to cut their compressed air energy usage figure by 10%, which could demonstrate savings of £147.5 million.
In the Chancellor’s Spring Statement, he promised to reveal a proposed tax rate cut on business investment this autumn. In the recent past, the government offered unprecedented support for businesses during the Covid lockdown period, but pandemic-related economic shocks and the accompanying uncertainty have limited business investment. That is why the super-deduction capital allowance scheme was introduced in 2021 to cut tax bills by 25p for every £1 invested in productivity-enhancing new plant and machinery, which includes compressed air equipment.
There is a degree of urgency for potential investors as the scheme ends in March 2023, so now is the time to make the right move to benefit from this 25% saving on capital expenditure. Those companies who already invested in modern, energy efficient compressors before the electricity price hike are already reaping the rewards of lower production costs compared to their competitors who are using less efficient technology.
In an effort to improve output without a capital cost outlay, some compressor users might resort to overhauls of their old or underperforming air compressor equipment. We would like to alert manufacturers that this practice becomes an expensive option in the light of higher electricity prices and ask them to look at the lifecycle costs instead. It has become much more cost effective to purchase a new, significantly more energy efficient model which uses less energy to run compared to overhauling outdated existing equipment.
We have already seen examples of customers who have cut thousands of pounds off their annual compressor running cost bills by installing new advanced compressors rather than overhauling the old ones. So that they have the full facts and can make an informed choice, we are now giving customers two options in our quotations: overhaul price versus new compressor price, that takes into account the associated electricity savings on the running costs.
To ease this route to more energy-efficient equipment and encourage compressor users to realise the significant payback from upgrading or switching to energy-saving systems, Atlas Copco offers finance packages for product upgrades through its hire purchase or fixed term rental options.
That is also why we developed our AIRPlan, which allows manufacturers to avail themselves of the latest, most efficient compressed air equipment whilst only paying for the air that they need. They still have to meet energy costs, but they save on substantial capital outlay and compressor running costs.
One area that offers manufacturers a significant opportunity for cost savings is to recover the waste heat from air compressors in order to reduce the need for purchasing energy to heat hot water, either for process applications or for plant room warming. Without energy recovery, this heat is lost into the atmosphere via the cooling system and radiation − and so is the opportunity to save money. Heat recovery is not a new concept, but we feel that now is a better time than ever for manufacturers to look into this possibility.
Although the amount of electrical energy that can be recovered depends on the size of the compressor and its running hours, typical energy recoveries attainable are between 70-94%. It is estimated that up to 90% of all industrial air compressors in the UK could be equipped with a heat recovery system that lowers operating costs and CO2 emissions, while also reducing the operator’s carbon footprint. We have calculated that compressed air heat recovery has the potential to save almost 2% of the UK’s electricity consumption, so it seems to be worth serious consideration.
Finally, we should not overlook the role of compressor system maintenance in energy-efficient production. It is very important for companies to view regular planned servicing as an essential component of energy optimisation, one that will sustain the efficiencies to be gained from new compressor installations or help to improve the performance of existing equipment.
All of the foregoing strategies represent good practice even in a less volatile economy than we are experiencing now. In keeping with the compressor industry at large, it is our earnest endeavour to assist UK industries in riding out this challenging period of uncertainty and look forward to more stable times ahead.