Upgrade of chemical dosing equipment at a wastewater treatment plant in Germany is delivering high performance on phosphorus removal, says Thomas Klobuczynski, industrial sales engineer, Watson-Marlow Fluid Technology Solutions.
The wastewater treatment plant (WwTP) serving the town of Hessisch-Lichtenau in Germany is taking an innovative approach to chemical metering in a phosphorus removal application.
Two diaphragm pumps, originally used to dose ferric chloride to eliminate phosphate, are being replaced with a single Qdos CWT peristaltic pump from Watson-Marlow Fluid Technology Solutions (WMFTS), in a first for the country. The Fürstenhagen wastewater treatment plant serves an 18,500 population-equivalent (PE) in the Werra-Meissner district of Hessen state.
The primary wastewater processing system includes a mechanical pre-cleaning system with grill and sand trap and an aeration tank with upstream de-nitrification and downstream nitrification, with recirculation. There are two secondary clarification basins and a sludge treatment unit.
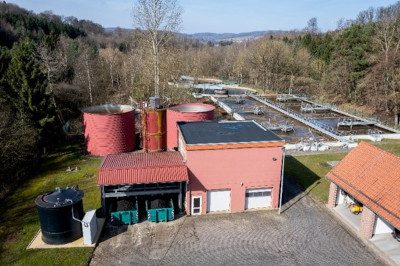
Ferric dosing
Chemical dosing with the precipitating agent, ferric chloride sulphate (FeClSO4), is required at the biological treatment stage for consistent phosphorus reduction, because the phosphorus load at the plant inlet is highly variable. Environmental regulations mean discharge of treated effluent to the river Losse is strictly limited to 0.70 milligrams per litre (mg/l) total phosphate.
Single-point dosing is used to deliver the precipitate, with the chemical metering pump drawing the ferric chloride from a 25m3 holding tank. It is then transferred to the dosing point, which is some 30 metres away.
According to the operator, it is essential that dosing is carried out consistently 24/7, but the two legacy diaphragm pumps performing this task, operating alternately, were unreliable and required frequent servicing.
Wastewater operations manager Marco Quehl said, “We need a constant basic amount of precipitant to be dosed, and the quantity needs to increase automatically in line with the phosphorous load at the inlet.”
Corrosion challenge
According to Quehl, the biggest problem with the diaphragm pumps was that the corrosive ferric chloride sulphate left iron residues on the pump valves, resulting in poor sealing against the valve seats and constant minor leaks.
“This required frequent minor maintenance work, and after an average operating time of around 12 months, in which the two diaphragm pumps ran alternately, we had to replace the pumphead, or even the entire pump,” he said. “When the necessary cleaning operations were also considered, this turned out to be time-consuming and expensive in the long run.”
Most chemical dosing pumps need regular maintenance to remain operational. This can take a pump out of service for hours, often needing a back-up pump to provide process continuity. It also takes the full attention of at least one skilled onsite technician.
Time saving
Pumpheads across Watson-Marlow’s entire Qdos range do not need to be taken apart. Instead, the pumphead is simply removed as a single unit and a new one clicked in place. It takes one operative less than a minute, offering substantial benefits in terms of time saving and onsite health and safety, as maintenance staff have no chemical contact.
“We’d already had positive experience with using Watson-Marlow Qdos tube pumps for dosing ferric chloride sulphate and other chemicals,” Quehl said, “which is why we agreed to testing the CWT pump at our site.”
The new Qdos CWT is the world’s first peristaltic pump with no tube, which represents a step-change in the mechanics of peristaltic pump design. The pump underwent its first field trial at Fürstenhagen WwTP as part of a long-term test period.
Reduced stress
While a conventional peristaltic tube is compressed flat via plastic deformation, the Qdos CWT pumphead incorporates an EPDM element, which is elastically compressed against a PEEK track. This reduces material stress and fatigue, providing significantly longer service life, reduced maintenance, and less plant disruption.
The pump is self-priming and there is no fluid back flow, even when the pump is not in operation. This also prevents gas locks, so there is no risk of interruption and no need for additional equipment such as pressure-sustaining valves, air-discharge valves or holding pumps.
Operations manager Bernd Sennhenn said, “The Qdos CWT was installed 12 months ago, and it has been running faultlessly since then. It was possible to install this pump as a direct replacement for a diaphragm pump.”
Reflecting on the trial at Fürstenhagen WWTP, Quehl said, “The Qdos CWT has been in operation for more than 8,000 hours and dosed a total of almost 90,000 litres of precipitating agent and hasn’t needed any maintenance.
“In comparison with diaphragm pumps, the Qdos CWT also doses more evenly and with lower pulsation, which protects the pipework and connectors. There’s no need for pulsation dampers.”
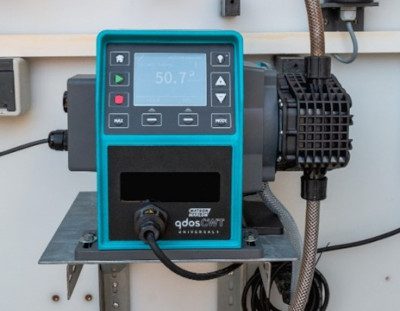
Continuous operation
The dosing pumps upgrade has saved the plant considerable outlay in time and cost. The Qdos CWT has been operating at an average of 75% of its maximum capacity, demonstrating its capability and reliability at higher performance ranges.
This reliability of the Qdos CWT lies in the design of the technology. The fluid contact element is subjected to low stress levels, and although a second metering pump is kept in reserve at Fürstenhagen, to ensure operational availability, it is practically never needed.
Due to the overall reliability and functionality of the Qdos CWT pumphead, the Fürstenhagen plant has achieved a 97.5% reduction in phosphorus load over the year.
“The new Qdos CWT technology is simply the best when it comes to dosing precipitating agent at our plant. There’s no need for anyone else to come to me with other solutions,” concluded Quehl.