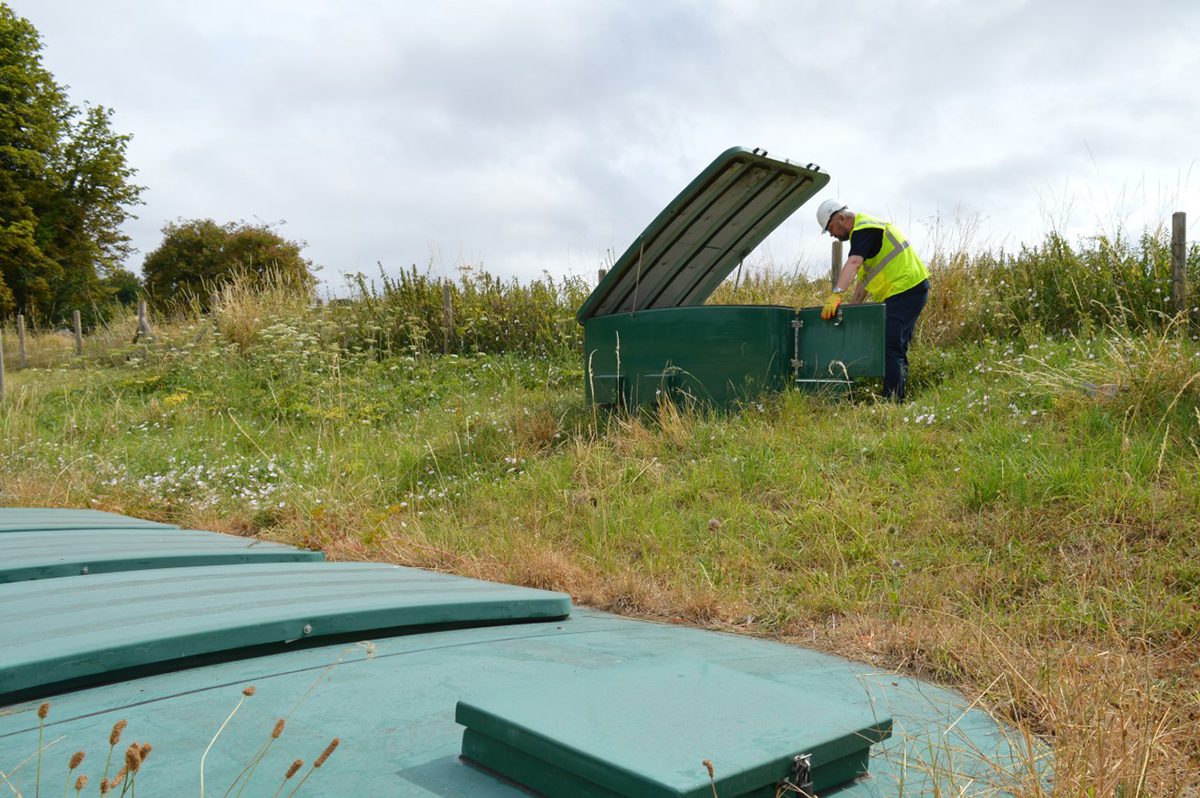
New energy saving measures developed by WCS Environmental Engineering (WCSEE) could reduce power consumption of its package wastewater treatment plants by as much as half.
The water recycling specialist has introduced automated timers to operate blowers in the biological treatment section of its patended HiPAF (high performance aerated filter) package treatment plants.
Blowers account for more than 95% of the energy used in a typical wastewater treatment plant. They usually operate 24/7 to blow air into biological treatment processes, providing oxygen to the bacteria that decompose organic substances in the wastewater, ensuring high standards of treatment are maintained.
Blowers in WCSEE’s HiPAF range are now timed to pulse air into the process, rather than operate continuously. The timers will be built in as standard to the HiPAF range of treatment plants, cutting the amount of energy used to treat effluent by up to 50%. This can contribute to companies’ net zero carbon emission goals, as well as bringing welcome reductions in energy costs.
WCSEE technical director Andrew Baird said: “Net zero carbon strategies are front of mind for businesses, with energy efficiencies critical to meeting climate goals. At the same time, businesses are facing huge rises in energy bills and cutting power consumption is now a priority for many to try and control costs.
“Building in timers to blowers has proven to be a simple and low-cost option to reduce power consumption by up to 50%, addressing the market need for both net zero and cost efficiencies.”
The timer concept was tested over three years by University of Portsmouth researchers at its facility at Petersfield wastewater treatment works, Hampshire, to ensure compliance was always maintained.
Baird said: “While the concept was simple, finding the right times to turn blowers on and off and for what periods proved more of a challenge. In general, we found the HiPAF only saw a reduction in dissolved oxygen after 20-30 minutes, allowing us to set timers to 15 minutes on and 15 minutes off.
“These intermittent pulses provide effective aeration for reliable treatment, while consuming significantly less energy. The 15 minutes intervals give the added advantage of not exceeding the on off cycles per hour required by the blower manufacturers, to maintain the blower guarantee.”
Research into process efficiency
WCSEE says the addition of timers has come as a result of part of its substantive research and development to enhance process efficiency of its HiPAF technology.
These studies have already achieved significant energy and cost savings with the introduction of the patented Hybrid-SAF (submerged aerated filters) technology to the biological treatment section, known as the biozone. The patented technology employs a submerged moving-bed, fixed-film reactor which can treat wastewater with greater energy efficiency compared to traditional submerged SAFs, in a tighter site footprint whilst meeting environmental compliance.
Baird said: “SAF treatment is traditionally viewed as a high cost process due to the energy requirement in delivering high volumes of air, and is generally not considered for larger schemes.
“At the heart of our Hybrid SAF technology are unique flow characteristics that have been patented. These ensure an even and continuous flow of nutrients up through the submerged, moving bed.
“The slowly circulating media gradually descends due to its increasing specific gravity from hosting biomass growth. Calculating the impact of gravity on the process results in a significant reduction in power consumption, improving overall efficiency and enabling a reduction in site footprint and a deployment of a more compact unit.”
Developments in hydraulic control and retention times have also enabled the patented process technology to consistently achieve final effluent ammonia concentrations of less than 1mg/l on a 95%ile basis.