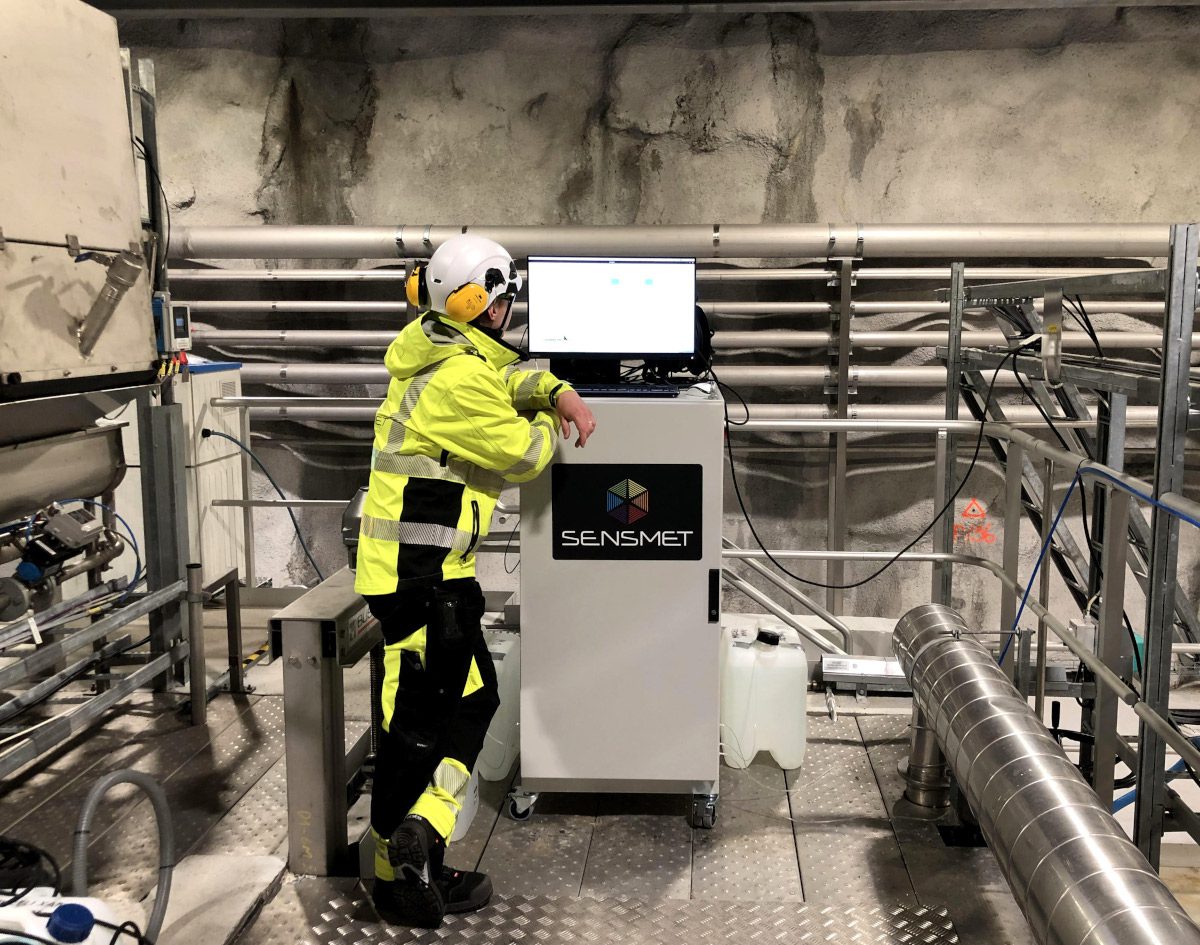
As global effort to fight climate change intensifies, the challenge for battery manufacturers and their supply chains is to find ways to meet the rapidly growing demand for electric vehicles (EVs). To help meet this challenge, a small start-up business in Finland, Sensmet, has developed an online monitoring technology that it says promises a step-change improvement in both the manufacturing and recycling of battery metals. Sensmet CEO Dr Toni Laurila, explains: “We bring the analytical performance equivalence of laboratory ICP-OES next to the production process where real-time metal concentration results are acutely needed. In comparison with laboratory analysis, Sensmet’s technology provides robust, fully automated online measurement, which offers enormous advantages for process management and quality control.”
Traditionally, battery metal manufacturers have had to rely on batch sampling and laboratory analysis in order to control their processes, but typically this incurs a delay of 4–10 hours. Sensmet has therefore developed a breakthrough online technology; Micro-Discharge Optical Emission Spectroscopy µDOES®, which is able to measure multiple metals, including alkali metals, such as any battery metal and their impurities, in real-time.
Laboratory analysis can take several hours for a sample to be collected and analysed in a laboratory, which means that process managers are unable to adjust dosing of chemicals efficiently. Consequently, raw materials are wasted and product purity – the most important product quality – is difficult to control, which is especially important because impurities significantly affect the performance of Li-Ion batteries. Sampling for laboratory analysis is also laborious, expensive and often rather challenging to reliably arrange 24/7. For all of these reasons, continuous monitoring has long been the dream in lithium manufacture, so with successful trials at several plants, the industry is delighted that the dream has become reality.
Background
According to the International Energy Agency (IEA), global sales of new electric vehicles (EV) grew from 3 million in 2020 to 6.6 million in 2021, and with increasing numbers of governments pledging to discontinue sales of petrol and diesel vehicles, demand for the batteries in EVs is set to escalate even further.
It has been estimated that 2 billion battery electric, plug‐in hybrid and fuel-cell electric light‐duty vehicles will be needed by 2050 to meet net zero targets. Each EV lithium-ion battery pack contains around 8 kg of lithium, and last year global lithium production was 100 000 tons. Lithium is also required for a wide range of other products, including mobile phones, laptops and energy storage systems. Consequently, there are enormous demands for lithium production to be efficient, high-quality and fast. Similarly, it will be necessary to recycle the components of EV batteries that have reached the end of their useful service.
High purity lithium hydroxide or lithium carbonate is required for battery manufacture. Impurities represent a significant challenge because they cause: poor charging performance, which lowers the range of EVs; more frequent charging; poorer performance in cold temperatures; and in some cases, they can cause batteries to overheat.
Continuous multi-metal monitoring technology
Sensmet’s Micro-Discharge Optical Emission Spectroscopy, µDOES®, enables the multi-metal real-time analysis of aqueous samples. In addition to lithium manufacture, the technology is also suited to the ‘black mass’ recycling of battery metals.
The patented µDOES® technology is based on atomic emission spectroscopy. A micro-discharge (electric spark) is created directly inside the aqueous sample, causing a microscopic volume of the fluid surrounding the spark to be flash-heated to 10 000 °C. Molecular species in the micro-discharge are dissociated into atoms, which are excited to their respective higher electronic states. Upon returning to their ground state, these atoms release their excess energy by emitting light at their characteristic wavelengths. The µDOES® measures this atomic emission spectrum to derive quantitative analysis of the metals contained in the sample.
Data from the µDOES® analyser are displayed locally showing the concentrations and trends for each metal, and alarm levels can be set for each element. Results are transferred digitally to users’ databases and/or the cloud.
In hydrometallurgical processes which cannot be controlled by monitoring pH, direct measurements of dissolved metal concentrations are essential. There are alternative methods of monitoring, but all of these have major limitations. For example, online XRF is unable to measure light elements such as lithium and sodium, and it is almost impossible to calibrate XRF for low concentration impurity measurements.
Advantages of continuous monitoring
Given the large sums of money involved in lithium manufacture (raw materials and final product), the accurate dosing of precipitation chemicals is extremely important. For example, when sodium carbonate is added to a slurry containing beta spodumene under high temperature and pressure, lithium carbonate and analcime solids are formed. If insufficient sodium carbonate is dosed, some of the lithium will not react to form lithium carbonate, and unreacted lithium will be lost in the side product analcime sand. This is extremely undesirable because it represents a loss of revenue. Overdosing is also undesirable because it would result in a waste of process chemicals.
Continuous monitoring is also vital for the reduction of battery metal impurities such as sodium, potassium, copper, zinc and calcium; all of which can be measured by µDOES® at any stage of the hydrometallurgical production and recycling process. Strict monitoring and control can therefore reduce the impurity levels and thereby prevent the cost and delay incurred by retreatment.
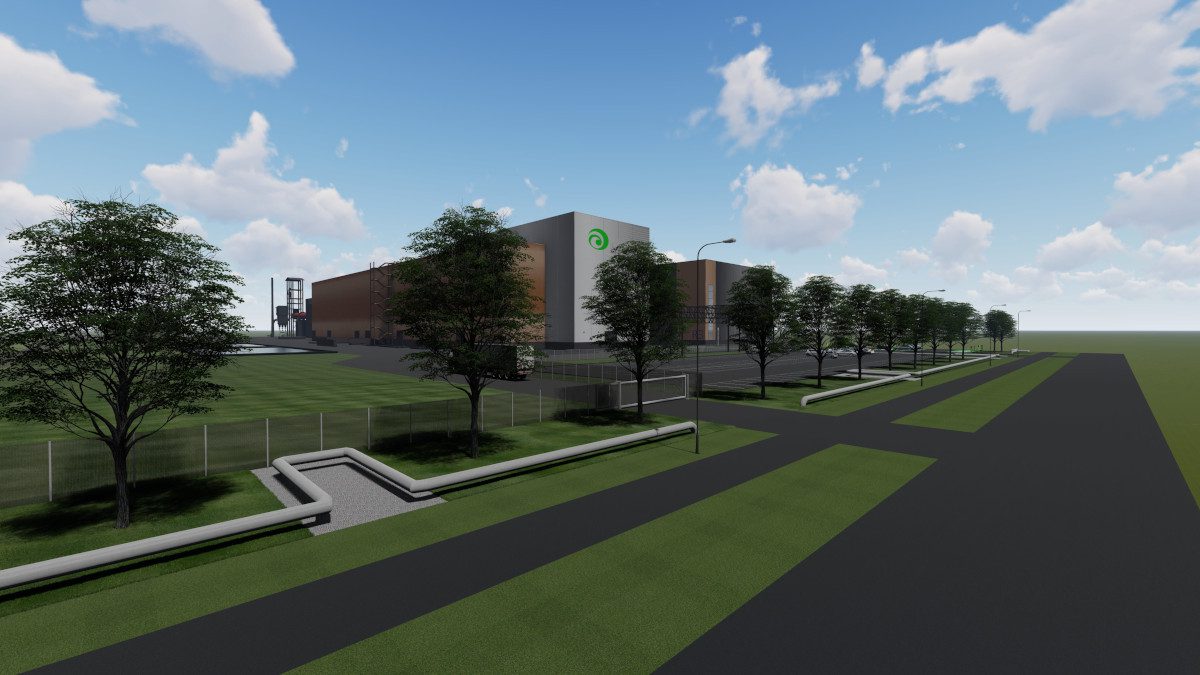
Case Study – lithium production from spodumene
Keliber, a subsidiary of Sibanye-Stillwater, used the µDOES® analyser in a pilot-scale test programme in 2022. During the project, battery-grade lithium hydroxide monohydrate was produced from spodumene concentrate treated by high-temperature conversion in a rotary kiln. A hydrometallurgical technology was developed to produce battery-grade lithium hydroxide monohydrate by soda pressure leaching. The pilot ran continuously at the demonstration plant for 400 hours, and achieved a total lithium recovery rate of more than 88%.
Keliber tested the analytical performance of the µDOES® analyser for the continuous optimisation of precipitation chemical dosing. Nearly 80 samples were drawn from the process and the sodium and lithium concentrations were analysed in parallel using both the µDOES® continuous analyser and a laboratory ICP-OES. The results showed an excellent degree of correlation between the µDOES® and laboratory analysis.
Commenting on the advantages of this new monitoring technology, Sami Heikkinen, Site Manager at the Keliber Lithium Chemical Plant said: “Chemical dosing based on reliable real-time data brings stability to the process, which is very important because it avoids drift and optimises both yield and quality while minimising cost.”
Conclusions
The switch from fossil fuels to electrically powered vehicles and renewable energy has dramatically increased the importance of battery technology. This, in turn, has created a major challenge for battery manufacturers and their supply chains. Consequently, there is a high demand for new technology that can help improve the quality and efficiency of production.
As the EV market develops, and global battery metal resources start to dwindle, there will be an even greater emphasis on the recycling of used batteries. Again, the online µDOES® analyser will help provide a solution because the processes involved with black mass recycling have to be closely monitored and controlled.
Sensmet says its µDOES® represents a breakthrough technology that will help the battery industry to realise its dream of effective process and quality control. Says the firm, the ability to conduct continuous, simultaneous measurements of multiple metal species in an aqueous matrix offers battery metal manufacturers the opportunity to improve process efficiency, lower costs, increase throughput, and improve the quality of the final product.