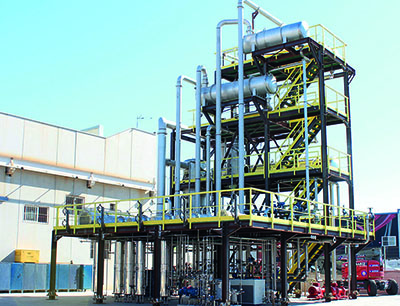
A new, combined evaporator and crystalliser has been developed by HRS Heat Exchangers to treat concentrated waste brine produced during reverse osmosis, and crystallised waste. Designed to form part of a zero liquid discharge (ZLD) system, the solution ensures the distillate which is produced, is returned as process water, and will help the heavy industry sector meet environmental regulations at the same time as reducing cavitation and corrosion issues while improving energy efficiency.
To meet the challenging specifications of the sector, HRS has pioneered the use of corrosion resistant titanium heat exchangers and developed a five-stage multistage flash evaporator. This innovative new system – including a preheater, de-gasser, main recirculating pump, five sequential heat exchanger sections and five sequential flash tanks as well as the final condenser – offers several benefits over forced recirculation.
Matt Hale, international sales and marketing director, said: “The new HRS Evaporator system only requires a single recirculation pump, instead of one pump for each effect, and the pump is installed at the lowest temperature level in the loop, significantly reducing the risk of cavitation and corrosion.
“The new design also means that a lower overall recirculation rate is required – this requires less energy for the pumping process and improves energy efficiency, helping business to reduce operating costs. “The last of the distillate is removed in the combined crystalliser unit and crystal ‘slurry’ can then be transferred to a mechanical separator. This final stage of the process helps businesses to ensure all distillate water is returned to the existing process, achieving a ZLD effluent treatment solution.” This is the largest combined evaporator and crystallisation solution manufactured by HRS to date, building on ZLD solutions developed by HRS for clients across the world.
www.hrs-heatexchangers.com