Around 80-90% of the weight of wind turbines can be recycled, according to recent estimates, although, historically, very little of this kind of thing has been undertaken.1 That doesn’t mean people aren’t giving it serious thought, and a panel discussion in May – at the AllEnergy event in Glasgow – profiled efforts to adopt circular principles in this sector. There are huge opportunities for the UK, but significant obstacles to be overcome, as Envirotec discovered.
As one panellist observed, “the uncomfortable truth” of wind power – a putative green energy source – is that “the aftermarket remains largely non-green”.
The situation is growing more urgent as the sector prepares for many onshore turbines to reach the end of their 20-25 year lives from around 2024.2 Offshore wind is more resource-intensive than onshore, and its first wave of deployment will also be ready for decommissioning within the decade.3
But there might be positive signs afoot. March saw the announcement in Scotland of the Coalition for Wind Industry Circularity (CWIC) – bearing the strapline “no time to waste” – in what seems an intent to send a clear signal that the wind industry in Scotland is committed to circularity. Katie Wallace-Lockhart, head of sustainability with SSE Renewables, one of the founding members of the group, opened the panel session at the AllEnergy conference, and was keen to talk up the economic opportunity, and signs she could discern of a shift in attitude from her own firm’s investors – the top 20 of whom had in recent months been seeking detail on the group’s circularity plans, with bid criteria on big projects now clearly incorporating this focus.
“We know that 80% of a modern wind turbine is recyclable so there are clear opportunities for wind farm operators to harness a circular economy by increasing the reuse of component parts from decommissioned projects.”
And the time is also ripe from an engineering and practical standpoint, she said, detailing SSE Renewables’ recent activity in sourcing remanufactured parts – specifically, yaw gears – as well as the benefits in terms of up-front costs (“less than buying new”), greater accessibility (“wait one month rather than three”), and the carbon and waste reductions associated with remanufactured parts. There is also the social angle. And when it comes to firms’ meeting commitments on Scope 3 emissions – “obviously, circularity has a big role to play”.
One confusing aspect of this topic is the profusion of “R” words that all seem to mean something similar – reuse, recycling, remanufacturing. A section beneath this article (“Circular toolkit”) offers a more precise formulation of each.
While recycling is often what people understand by circularity, it’s just one circularity strategy among many. Others promise to have a greater environmental impact than recycling, in the wind sector, including improved component durability, repair, reuse and remanufacturing.3
Recycling of wind equipment can also be water- and energy-intensive, and impossible to achieve without losing material quality and quantity.4
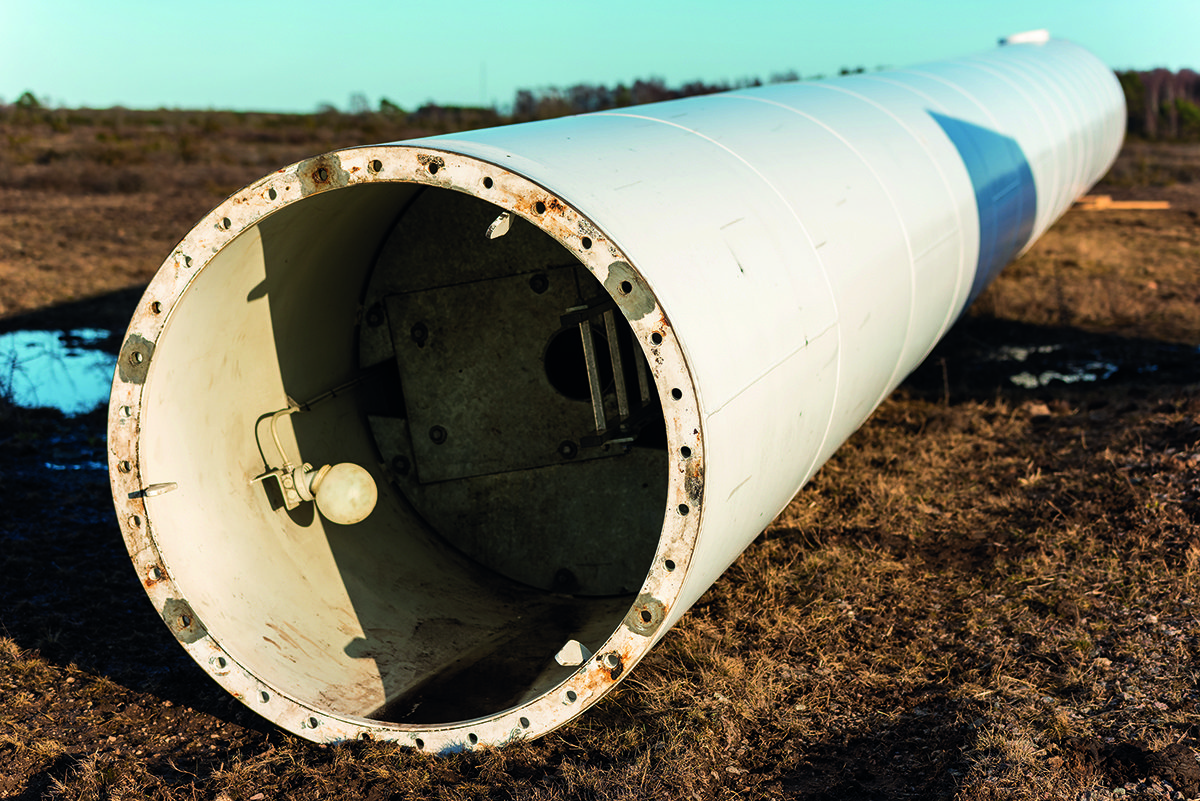
What is “circularity”?
Much of the session looked at immediately practical steps, such as beginning to use remanufactured parts, and decommissioning wind turbines that were not designed with circularity in mind – dealing with the messy status quo, in other words. But circularity obviously implies something more idealistic and ambitious; in other words, re-thinking the entire lifecycle of a product like a wind turbine from the initial extraction of raw materials to the decommissioning or reuse of the product at end-of-life. The point ultimately is to “reduce the amount of materials taken from the natural environment”, as Dr Anne Velenturf of the University of Leeds put it, pinpointing the aspect of the concept she felt to be most important.
The resulting, more idealistic framing maybe tends to get lost as the word “circular” gains traction as a box-tick item in marketing communications. So many industries – including renewables like wind, ironically – still appear largely committed to a linear production cycle.
Velenturf’s presentation called for more pragmatism and realism about what people are doing under the banner of circular economy – for example, she said “I don’t believe in 100% closed loop”, and she attributes5 the concept’s inaccuracy to the inevitable loss of material quality during recovery, and the fact that these processes require energy.
Elsewhere she has explained that this misconception and others seem to underpin the “butterfly diagram” referenced widely in circularity literature, and which has helped shape legislative programmes like the EU’s Circular Economy Package.6 A 2019 paper attempts to broaden the scope of the term circularity to include things like the impact of the extractive sectors and the initial processing of materials. These are “largely excluded” in the butterfly diagram, despite being “the largest waste producers and energy consumers in the production-consumption system”.7
And it gets worse when you consider that the amount of material going into wind power is set to increase fourfold in the next ten years.
Offshore wind, for example, will require much larger amounts of material for the foundations (like concrete, steel, copper and glass fibre). The larger size of offshore wind turbines may also equate to more material per unit of power generated.
Velenturf produced a slide showing the materials in use in offshore wind in the UK in 2019, drawing upon information from a recent study,8 and covering a total of 2,555 turbines, with a materials tally that includes 1.7 million tonnes of steel, 23 ktonnes of copper in cables (equal to two return flights between London and Iceland), 152 ktonnes of blade materials, and 55ktonnes of nacelles material (including steel, aluminium, copper, and rare earth elements).
“One material we don’t talk about enough is cement”, she said, adding that she didn’t think the UK would have enough to meet its demand for offshore turbines.
The turbine blades themselves have been a locus of concern because of a lack of available methods for recovering these composite materials (typically, a composite of epoxy resin and glass, or carbon fibre), which have tended to end up in landfill (one 2018-19 study cites a diversion rate of only 10%),7 or incineration.
Siemens Gameza announced it had developed “the world’s first recyclable offshore wind turbine blade” in early 2022,8 seemingly underpinned by a new epoxy resin that could be easily separated from the other materials comprising the blade. The recycling process requires only acetic acid (i.e., strong vinegar) and 80ºC. These recyclable blades are available at a slight premium, and the value proposition is partly about insurance against future disposal costs. Several European countries already have put bans in place against landfilling wind turbine blades, and more are expected to follow. The FT reported the work in a positive light but suggested that a definitive judgement may have to wait 20-25 years until these new turbine installations reach end-of-life.
Modelling scenarios
How might we lessen the resources consumed by wind power? Velenturf cited a recent study, modelling material flows in and out of the offshore wind sector until 2080. It explores seven scenarios deploying different circular economy strategies (increased recycling, two rounds of repowering, remanufacturing, robotics-enabled operation and maintenance, and all of these strategies combined). These are compared against a baseline of “business as usual”.
Findings in relation to carbon included:
• that carbon and material use closely correlate.
• Increasing the amount of material recycled immediately reduces carbon.
• Circular strategies can reduce material demand
• Repowering on reused foundations can more than halve material use in the 2050s, but it requires 5-10% more material around 2030.
• We can hit zero embedded carbon in 2060s
And in relation to jobs:
• Only remanufacturing increases jobs (and by c. 7% compared to BAU)
• Other circular strategies may delay overall job creation
• But the increase in jobs may fall outside the wind industry, in the resources and decommissioning industries
And in relation to capital costs:
• All the circular strategies combined can lower these fivefold in the 2050s.
• O&M robotics has the largest potential to reduce capital costs over time (but can also cause an increase in costs)
• Repowering on reused foundations can consistently lower costs by c.30% in the long term
Obstacles to circularity
One of the mysteries is that reusing and remanufacturing components hasn’t caught on in wind, until now perhaps, despite offering so much promise.
There seems to be 100% awareness of the availability of remanufactured parts, as David Butler of Strathclyde University explained (preferring to call them “recirculated” parts), quoting a study of the wind sector.
Around half of firms have a procurement model already in place towards these parts, and 40% have a specific policy that defines their use. But 81% of participants said they perceived some hesitation about using them.
One reason might be to do with perceptions about safety, but he said, most of us happily fly in aircraft whose engine parts have been remanufactured every couple of years.
There are so many benefits to using them. Aside from price and availability, developing this kind of expertise helps firms better appreciate why a particular part has failed, and how to make it better next time. And of course, there’s the environmental impact and the potential for job creation.
Brexit and Covid “have had a massive impact on supply chain agility”, and that certainly hasn’t helped. Remanufacturing requires greater cooperation between stakeholders. Butler’s study cited 47% of participants having reservations about collaborating with other groups on research (while 53% already collaborate in this way to achieve sustainability goals).
What parts are currently being remanufactured? James Bary, chief executive of Renewable Parts – the firm supplying remanufactured yaw gears for SSE Renewables – said only around half of the components that could be replaced during a turbines life were being replaced. “That should make us uncomfortable,” he said. This 47% share (“minor components” in the pie chart he shared) were parts outwith the gearbox, generator, converter and transformer.
His own background in aerospace seemed germane to the discussion, and it seems to provide a model that the wind sector could emulate without needing to reinvent the wheel. There are obvious similarities between the two – in both cases the operators don’t generally own the asset, for example. The UK is the third largest aircraft decommissioning centre in the world.
So aerospace is an area where the success of remanufacturing has been proven. “80% of turbine engines on aircraft are refitted,” he said, “so any notion of these parts being risky or inferior is completely misplaced.” He said data and test results prove this, and could be used to change attitudes.
Wind could follow a similar model, whereby a business designs a product, then designs thousands of repair schemes, and sets up a system of tiered suppliers who can deliver it.
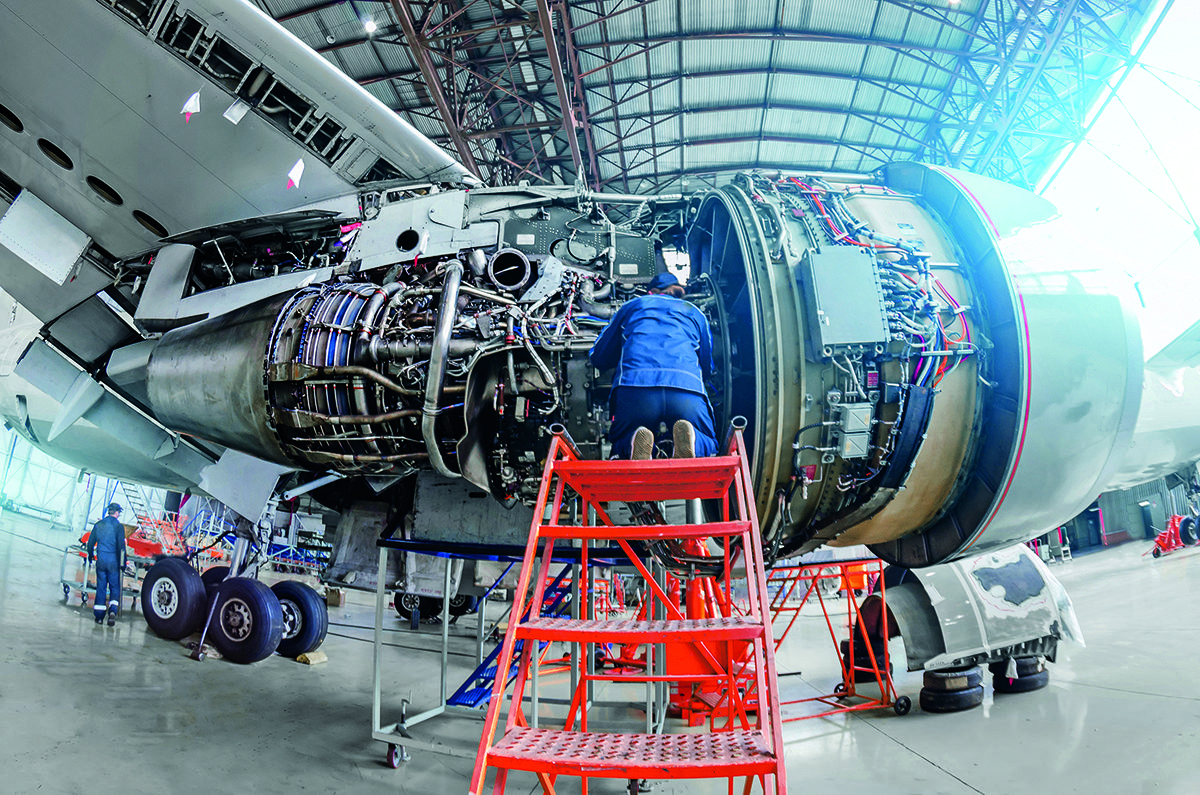
What next?
Data is a crucial underpinning, said Bary. For example, to get a better handle on which parts are likely to fail. So much data has to be acquired, validated, shared, certified and so on. Manufacturers need assurances about the qualities of particular components to enable reuse, remanufacturing and repair – this needs to be accurate and verifiable information. “You’ve got to have the paperwork to give customers confidence.”
At this stage there are questions around the standardisation of such data – who should provide that? The OEMs hold most of the data, so they have the control, and it really requires their participation for things to move forward.
For parts reuse to become the default option for operators, a few factors need to be addressed. Parts availability must be above a threshold to make it operationally expedient and scalable. The sustainability benefits of reuse must be “tangible and monetised”. Is it about cheaper parts or lower aggregate cost? There should be clarity on issues like these. And finally, perceptions around performance and technical rigour need to be overcome.
Up until now, wind turbine components have been designed for performance, and also to allow maintenance. They haven’t been designed for remanufacturing, but “we’re trying to figure out how to do it”, said Bary.
New technology will play a key role, and this sector will be less about metal bashing and more about advanced engineering, and applying techniques like additive and hybrid manufacturing in innovative ways. How do you apply it to components that have failed? The National Manufacturing Institute Scotland (NMIS) – another founding member of the new CWIC group – has expertise that could be instrumental, said James. Advanced technology needs new and advanced skills, he said, and remanufacturing is not the same as manufacturing. “But we’ve made appreciable inroads already.”
We’re currently short of the people needed to do this, but we’re not the only country that is, said David. James also noted that the UK seems to be “squeamish about manufacturing.”
“For some reason, we decided we didn’t want to develop the design and manufacturing of wind turbines, yet we buy them.” And while “that ship has sailed”, he said, we can get in at the start of this new sector, remanufacturing.
Notes
[1] https://www.circularonline.co.uk/research-reports/towards-a-circular-economy-framework-for-offshore-wind/ [2] ibid [3] https://www.mdpi.com/1996-1073/14/17/5540 [4] https://www.sciencedirect.com/science/article/pii/S0048969719330220 [5] ibid [6] ibid [7] https://www.sciencedirect.com/science/article/pii/S0048969719330220 [8] ibid [9] https://www.mdpi.com/1996-1073/14/17/5540 [10] ibid [11] ibid
Circular toolkit – SIDE PANEL
Recycling appears less important in the wind sector than other circular strategies, some of which are outlined in more detail below. Anne Velenturf of the University of Leeds has attempted to itemise the circular strategies relevant to wind (eighteen at the last count),9 including those listed below. Some of the definitions draw on a recent paper presenting her work.10 Why do so many of them begin with “R”? We can’t answer that one.
• Remanufacturing. Often held to be an activity that involves rebuilding, repairing or restoring end-of-life products to get them to a level that meets or exceeds the original performance specifications. The lack of a commonly accepted definition and standards has itself been an obstacle to acceptance of this emerging activity.
• Refurbishing. Described as “less rigorous in nature” than remanufacturing, and an activity in which “the overall structure of a large multi-component product remains intact, while many components are replaced or repaired”. Velenturf’s taxonomy considers “Refurbish and Remanufacture” as a single circular economy strategy.
• Repair and maintenance. One accepted definition is “restoring a product to a sound/good condition after decay or damage.” Maintenance on the other hand, is considered to be “the performance of inspection and/or servicing tasks at regular intervals, to retain a product’s functional capabilities and/or cosmetic condition.” One recent paper defines strategies under this heading as aiming “to increase the duration over which a component — and, thereby, a whole infrastructure — is in operation.”
• Reuse. Velenturf et al defined component reuse as constituting “operations through which products or components that are not waste are used again for the same function and may involve ‘checking, cleaning, repairing, refurbishing, whole items or spare parts’ to prepare for reuse.” Seemingly important enablers include designing components for durability, and ongoing maintenance and repair to help extend lifetime.
• Repurposing. Distinguished from reuse and relevant to where a component or product is used for another function. For example, reusing part of a turbine blade as a construction material or architectural feature.
• Recycling. Velenturf notes that recycling “is not clearly defined in the waste hierarchy”, and definitions often involve a material that has been designated as waste being repurposed or used again in some way.
• Repowering. Velenturf’s taxonomy describes it as “a way of extending a wind farm’s service life by replacing either wind turbine components or existing wind turbines with new, more powerful machines.” Some part of the wind farm infrastructure will be reused – the subsea cabling, for example. Or the same foundations might be used to repower with a smaller turbine, if there are concerns about structural integrity, and to postpone decommissioning costs.
• Decommissioning. This is the process where wind farm systems are de-energised and disconnected, and removed. This seems to be an activity that looks very different when you apply circular principles, and a more proactive approach involves designing offshore wind turbines with decommissioning in mind. Rather than simply considering the various parts as waste materials (destined for “recycling”, incineration or landfill), they should be designed to allow reuse and remanufacturing. Regulations needs to develop too, suggests one paper,11 to take a more proactive approach to salvaging components, and to understand that component reuse is something quite distinct from recycling.