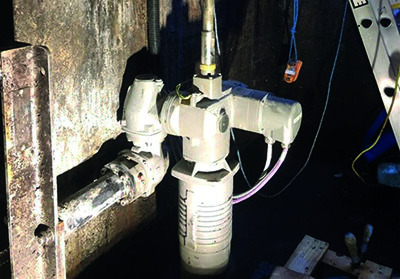
A new automated shutdown system that helps protect local watercourses has been installed by AUMA Actuators in a wash-down area for de-icing commercial airliners at a London airport.
The firm designed, installed, tested and deployed a new automatic shutdown system that prevents a high concentration of glycol from entering the watercourse, in the event of a higher-than-normal level in the aircraft wash-down mixture.
Colin Borrows, Operations Manager, AUMA Actuators Limited, said: “This was a really interesting and technically challenging project, which had at its heart the integrity of the local watercourse.
“A pair of manually controlled penstocks was already installed in an underground valve chamber with severely restricted space. Our specialist confined space team was tasked with automating the control of the penstocks, whilst retaining the option to manually control the penstocks in the event of an electrical failure. We achieved this using AUMA’s handwheel extension drive to allow valve key operation, alongside the ability to remote mount the control heads.”
The system comprises four main parts; the actuators with remote-mounted AC control heads; the existing penstocks; a bespoke control panel; and a glycol analyser.

It operates by opening and closing two penstocks mounted below the airport apron, which diverts wash-down water to an interceptor holding tank in a controlled sequence triggered by a glycol analyser. The analyser constantly monitors the glycol water mix. When high glycol concentration is detected, a signal is sent to the control panel, which initiates the shutdown sequence to the actuators.
AUMA technicians built a custom panel to control the actuators, in line with the glycol sample station. Two AUMA SA07.6 (actuators), AC01.2 (controls) and GK10.2 (gearbox) actuators and gearbox combinations were installed in the underground valve chamber, with cable set run to the airport’s kiosk, plus mounting of control heads.
Field technicians removed the old gearboxes, driveshafts and mechanically installed the replacement gearboxes and actuators. The cable sets were then run in the cable ducting and fed into the kiosk. The control panel, local isolators and control heads were mounted and connected in the kiosk. The SA type actuator range is for open-close duty and positioning duty and are rated for class A and B or types of duty S2 – 15 min. A special version for longer running is available for S2 – 30 min duty. Actuators can be combined with various controls from simple OPEN-CLOSE controls to the micro-controlled versions with logging of operating data or fieldbus interface.