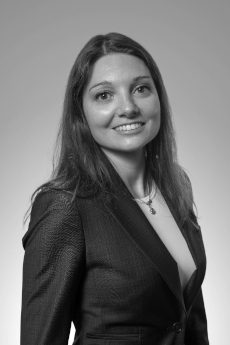
5th July marked one year since the launch of ConcreteZero, a global, industry-led initiative to achieve net zero concrete by 2050. Rossella Nicolin reflects on progress made towards this goal over the last 12 months and provides a look ahead to what’s on the horizon.
Concrete production accounts for 8% of global annual carbon emissions – if it were a country, it would rank somewhere between the US and India in terms of its carbon footprint.
As the most used building material globally, demand for concrete is significant, and growing, meaning that the concrete industry’s road to net zero will be critical to meeting global decarbonisation goals.
This transition to net zero concrete will require large-scale collaboration, which is precisely the challenge that ConcreteZero was launched to address. With diverse membership from across the concrete and construction value chain, ConcreteZero has three ambitious targets: to deliver 30% low carbon concrete by 2025, 50% low carbon concrete by 2030 and net zero concrete by 2050.
By facilitating engagement from a range of businesses, ConcreteZero is championing solutions that will accelerate decarbonisation and shift global markets, investment and policies towards the low-carbon production and sourcing of concrete.
But this progress will not be achieved by one solution alone; a holistic approach must be taken, consistent with the Institution of Civil Engineers’ (ICE) Low Carbon Concrete Routemap. At Laing O’Rourke we embrace this thinking, and are pushing the boundaries of how we build by focusing on the combined effect of addressing three levers: materials, design and systems.
Innovation in materials
An important step in the concrete decarbonisation journey is to focus on the optimisation of existing materials – exploring how to best use alternatives to Ordinary Portland Cement (OPC), the most carbon intensive material within concrete. These alternatives are known as Supplementary Cementitious Materials (SCM) and can be blended with cement to achieve a lower carbon footprint than traditional concrete. The most widely used SCMs derive from industrial waste; however, a host of more promising and more long-term alternatives are already in development and being trialled.
One of these alternatives is cement-free geopolymer concrete, a solution that we have successfully trialled at our in-house testing centre and at the Laing O’Rourke Centre of Excellence for Modern Construction (CEMC), our offsite manufacturing facility. These trials have provided sufficient confidence in the material technology and our manufacturing capabilities, enabling us to offer this solution to clients, and work with industry bodies – like ConcreteZero and ICE – to ensure that technological developments and global best practice are reflected in our standards.
As part of our ongoing research into low carbon alternatives, we are also investigating and trialling the switch from industrial waste to natural SCM replacements, such as calcined clays or volcanic pozzolans, which are abundant materials and not subject to longer-term supply constraints. We are also closely following the trend towards ‘next-gen geopolymers’, which are cement-free concretes that use natural pozzolanic materials. While the market for geopolymer concrete is still in its infancy, it presents an opportunity to reduce carbon in a responsible way, rather than relying on waste from declining industries.
Looking towards 2030 and beyond, carbon capture and utilisation (CCU) through CO2 mineralisation is an emerging solution. This technology involves capturing CO2 during industrial processes to produce carbon neutral or negative cement replacement materials and aggregates. We are supporting a number of technology companies in this arena and are applying our concrete and construction expertise to assist in developing and accelerating roadmaps to deployment.
Designing efficiently through whole systems thinking
While investment in lower-carbon materials will be vital to accelerating decarbonisation, the priority must be to deploy more focus, investment and ingenuity to create smarter, more efficient designs and systems, where we can eliminate material use from the start.
This will require transformative thinking to reinvent how we engineer, but the solutions can be simple. Take flat slabs of concrete for example. These are frequently used in construction, but are far less efficient than ribbed slabs or compression shell designs, which can significantly reduce embodied carbon. We are working with clients and designers to implement these low-carbon solutions, like our prototype compression shell solution, which was developed and built in partnership with Arup.
Another opportunity lies in reinforcement. Steel is used to reinforce concrete, increasing levels of embodied carbon. While the use of recycled steel is one solution – and one that we deploy extensively today – we are also trialling alternative materials like basalt and fibre reinforcement, as well as composite systems such as timber-concrete.
Embracing a holistic approach
It is only through a combination of low-carbon innovation, efficient designs and the evolution of existing systems that large-scale industrial decarbonisation can be achieved. At Laing O’Rourke, we are working to embed this thinking into all that we do. We have a longstanding and comprehensive research and development programme, strengthened by our in-house expertise and strategic partnerships.
From our specialist concrete technologists, technical engineers and dedicated technology and innovation team, to our industry-leading UK facilities – including a testing laboratory, concrete batching plant and CEMC – we have the skills, technology and premises needed to trial pioneering technologies, prototype solutions, take those new solutions to market and deploy on live projects.
We also work with academic partners, including the University of Cambridge, Imperial College London, and the University of Sheffield Advanced Manufacturing and Research Centre (AMRC), to advance our work. These partnerships have not only enabled us to collate learnings and enhance our techniques, but also to implement milestone decisions within our business.
Most notably, in April of this year, we announced a flagship initiative to mandate the use of low carbon concrete on all of our new UK projects. Following extensive research co-funded by Laing O’Rourke and Innovate UK, we have proven that low carbon concrete mixes can be deployed on all projects as a like-for-like substitute for traditional concrete. The concrete mix used will vary on a case-by-case basis, however all must align with the ConcreteZero and ICE definition for low carbon concrete – Grade A or better.
Looking ahead
We recognise that our in-house expertise gives us greater agility. It means we can adopt new methods and technologies fast and implement them more smoothly. And it also aids risk management.
We utilise these strengths to progress research and development of ultra-low carbon materials, design and systems. And we collaborate and share knowledge with our partners, with our industry peers and with our clients, in pursuit of making quicker progress towards the common goal of decarbonisation.
Our industry is pushing in the right direction, and ConcreteZero has been a catalyst for greater collaboration and new action. But there is much to do before 2050, and the importance of industry, academia and government partnership to making net zero concrete the norm, as well as making decarbonisation progress in other areas, cannot be understated. Working across the concrete and construction industries to test and commercialise new, decarbonised solutions will be the ultimate measure of success.