This article contains paid for content produced in collaboration with HRS Heat Exchangers
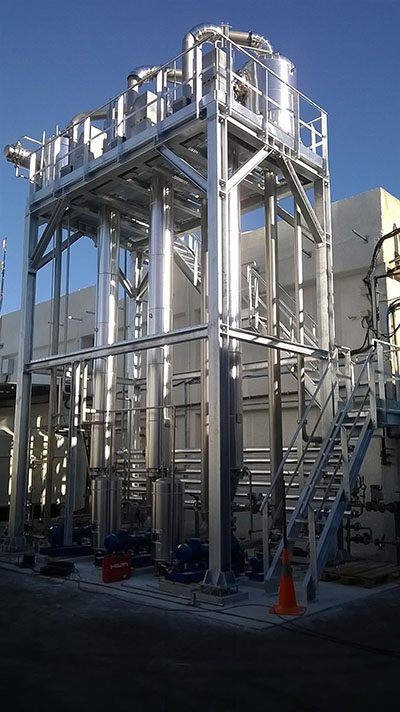
Heat exchangers often play a key role in wastewater treatment, and all but the most basic heat exchangers are created to a bespoke brief, designed to take into account the materials being heated or cooled, the heating or cooling medium, the amount of effluent being processed, velocity, risk of fouling and other factors.
The first consideration to bear in mind is the nature of the material being processed. The simpler and less viscous the material, the simpler the heat exchanger can be. As materials become thicker, or contain suspended particles or large solids, then heat exchange becomes more difficult, and more sophisticated designs are required. Starting with simple multi tube designs, the range moves through double tubes – where viscosity is higher or solids are present – with the most challenging materials (such as very thick digestate sludges) requiring the use of scraped surface heat exchangers.
Another consideration is what happens in the event of a leak. A leak can be business critical or cause significant environmental damage. In such cases, double tubeplate multitube heat exchangers should be specified, as these provide leak detection in order to avoid cross contamination between the service and product fluids.
Most heat transfer applications will require the use of corrugated tube heat exchangers. These offer a number of benefits over smooth tube designs – in particular, heat transfer and energy efficiency are increased (making them better for high-capacity heating or cooling). Fouling is also minimised meaning that units can be more compact and economical, and cleaning and servicing requirements are reduced. For the most challenging applications (such as when using materials with high fouling potential), scraped surface heat exchangers are used. Double-tube heat exchangers consist of a tube within a tube and are among the most versatile corrugated tube heat exchangers. Multitube heat exchangers are the simplest design and carry the product in more than one interior tube, while the service fluid flows through the surrounding shell. Scraped surface heat exchangers (SSHEs) are the preferred choice for difficult heat transfer applications; for example, those with high viscosities and where fouling can become a problem.