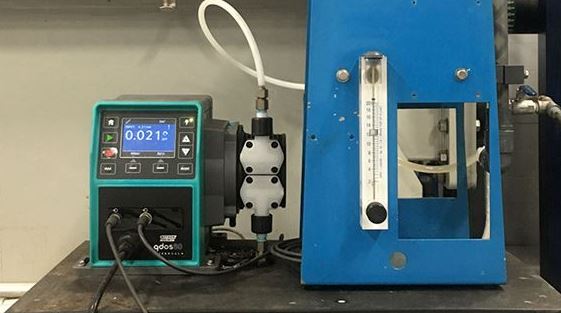
Polymers play a key role at municipal/industrial water and wastewater treatment plants, but also bring the risk of major disruption and extra expense if they are not handled with reliable, leak-free equipment, as pumps manufacturer Watson Marlow explains.
A polymer leak will halt production and is costly, time-consuming and labour-intensive to clean up, and also creates a safety risk. Wastewater treatment operators want to avoid the disruption of maintenance downtime while also abiding by strict regulations for harmful chemicals, pharmaceutical residues, and microplastics.
In Germany, these regulations mean opportunities for reusing wastewater sludge as agricultural fertiliser are being increasingly limited. Sending it to landfill, on the other hand, is usually not permitted. This means thermal recycling is becoming more and more accepted as a method of sludge disposal, but the required sludge dewatering and polymer dosing during the sludge conditioning process can add significant cost. Therefore, identifying cost-efficiencies in the dewatering process can mean significant savings for wastewater treatment plant operations, and reduce the amount of sludge produced and polymer used.
The operator of a wastewater treatment plant in Heide, Schleswig-Holstein, Germany, changed its chemical dosing pumps after experiencing maintenance interventions and polymer leaks with progressive cavity pumps. Also, there was no leak detection system in place, so if a tube failed the entire polymer contents in the container could leak out. This meant a loss of expensive polymer, additional maintenance, and time to clean up leaked chemical. Additionally, the amount of time and effort involved in servicing the screw pumps, due to the different parts that come into contact with the polymer, was a growing problem.
Peter Dohrn, wastewater treatment manager and technical department manager at Abwasserzweckverband Region Heide (AZV Heide), said: “A slippery mess on the floor would require intensive cleaning. Every servicing run involved several hours of work [with the screw pumps]. Also, the extremely heavy progressive cavity pump was hard to move around, and its working principle meant it couldn’t achieve the dosing accuracy of other pumps due to its design.”
Spill prevention – avoiding high cleaning costs and environmental damage, while ensuring safety of workers – is a key consideration when deciding which pump solution to use for handling polymers.
Water treatment operators therefore need to consider prioritising the adoption of dosing solutions that avoid messy polymer leaks because of the following:
• Cost: Wasting polymers is expensive. Major producers of specialty chemicals recently announced price increases in products like polyacrylamide (PAM). Then there is the cost of cleaning products in the event of a polymer leak.
• Sustainability: To ensure a sustainable use of polymers is achieved by minimising polymer use with accurate dosing pumps. Also, by eliminating chemical waste through leaks, and avoiding the need for cleaning chemicals in the event of a spillage.
• Safety: Spilled polymer is extremely slippery and difficult to clean, with the possibility of some residue left behind causing a safety risk of slipping for operators if it gets wet.
• Maintenance: Water treatment operators are under increasing pressure to produce more clean water so cannot afford downtime. Some rural plants also have a small workforce where regular, unplanned maintenance is a challenge.
• Accuracy: Reliability of the dosing pumps is critical to thickening the sludge in a cost-effective manner.
The Heide water treatment plant replaced its screw pumps with a Qdos 60 PU peristaltic pump, from Watson-Marlow Fluid Technology Solutions (WMFTS), which has been specially designed to dose hard-to-process polymers, and other hydrocarbons, with high-precision accuracy, for use in the sludge conditioning process.
ReNu PU (polyurethane) pumpheads for Qdos® peristaltic pumps are designed to avoid messy situations by safely containing polymer spills in the event of tube failure.
ReNu PU pumpheads are now available in two sizes: Qdos 20 PU up to 28 L/hr at pressures up to 4 bar), and the recently released Qdos 60 PU (up to 60 L/hr at pressures up to 5 bar). Specifically designed for polymers, the polyurethane (PU) tubing element is not damaged by the chemical.
The specialised tubing sits within the sealed housing of the pumphead, so if there is a leak, the pumphead contains the polymer spillage which minimises chemical waste and stops creating a safety risk which has been important for operators at Heide in Germany.
“In comparison to our previous pump, the Qdos has a much higher level of safe chemical handling and operational safety,” said Dohrn.
“Thanks to its highly effective suction capability, the self-priming Qdos pump can extract polymer from the IBC (intermediate bulk container) from above by means of a suction tube. The pump handles the suction height of just under a metre with ease. The pump can also empty the polymer almost completely reducing the risk of leakage during changeover.”
Chemical compatibility priority
As well as containment, water treatment operators must consider chemical compatibility for successful handling of polymers at their plant.
Water-soluble polymers are commonly used in wastewater treatment to remove suspended solids and contaminants. Polymers attract the suspended fine particles to form larger groups, which settle at the bottom as a sludge to be removed, leaving clear water.
Polymers in liquid and dry form are employed for coagulation, flocculation, clarification, thickening and dewatering at water at wastewater treatment plants.
When polymer molecules are uncoiled and extended, they become fragile and can fracture by high-shear pumps such as diaphragm pumps. If agitated and mixed prior to use, polymer chemicals will not work as intended.
But it is not just polymers which can get damaged. Complex polymers such as polyacrylamide (PAM) present challenges for some pump types and tubing, such as diaphragm metering pumps, and can lead to equipment failure, with clogging and spillage requiring regular maintenance.
Precision Chemical LLC supplies advanced water treatment technology, including customised water chemistry programmes, to industries ranging from power plants, pharmaceutical plants, automotive, plastics, rubber, food and dairy, to commercial and institutional HVAC systems. The Indiana, US-based OEM maximises system efficiency for its customers who would be extremely inconvenienced by a polymer spill.
Fred Shurtz, President of Precision Chemical LLC, said: “It’s a pain cleaning up polymer because the product basically multiplies by magnitudes when water hits it. So, when we have to clean up a mess, we have to get lots of oil dry compound and then soak up the polymer and shovel it into a dumpster. It’s really no fun at all. But the big picture is we are not delivering the product [polymer] to the system which causes a disruption in operations. It sometimes takes days to get back to ‘normal’ operations following a spill.”
Dosing-pump switchover
Precision Chemical LLC switched from another pump type to Qdos 20 PU for handling polymers at a power plant in southern Indiana over 18 months ago. It is being used to deliver an emulsion polymer to both a thickener and to some tanks prior to a vacuum filter operation.
Shurtz added: “I was previously using a Qdos competitor’s product and was having issues with reliability, plugging, and tubes bursting. I switched to Qdos 20 PU because it was explained to me in detail why this pump would work when the other did not.
“The Qdos 20 PU has worked very efficiently and reliably since my purchase. I used to have big emulsion polymer clean ups with the other systems due to breakage and I have not had any since switching.
“My previous polymer pumps would burst the tubes every two months. This meant clean ups and messes that the customer does not like to see. Plus, during this downtime, I’m not clarifying the water as I am supposed to be which causes other issues. With the Qdos 20, I went a full year before I switched out the head and when I switched out the head, it was not because it failed, but instead I felt like it may fail so I changed it out. Twelve months is a long time to go without changing out a tube with an emulsion polymer.”
The ReNu PU pumphead is a tube technology that increases the chemical compatibility range of Qdos pumps. Qdos 20 PU and Qdos 60 PU transfer polymers accurately (±1%) in a low-shear, gentle pumping movement that do not damage the chemical, which is critical with polymers.
The only part of Qdos pumps which need to be replaced is the patented ReNU pumphead. Maintenance, when required, is quick and simple with no-tools pumphead replacement. The polyurethane tubing pumphead is designed for simple one-minute maintenance, providing a safe solution and enhanced productivity in PAM metering, and other flocculants and coagulants used in water treatment.
A polymer spill is an incident that is worth taking steps to avoid and a leak-free chemical dosing pumps such as the Qdos 20 PU and Qdos 60 PU are specifically designed to eliminate those concerns while also providing accuracy, repeatability and minimal maintenance. Partnering with Watson-Marlow means you can rely on the polymer handling expertise of our team for support in navigating environmental regulations and how to avoid leakage.