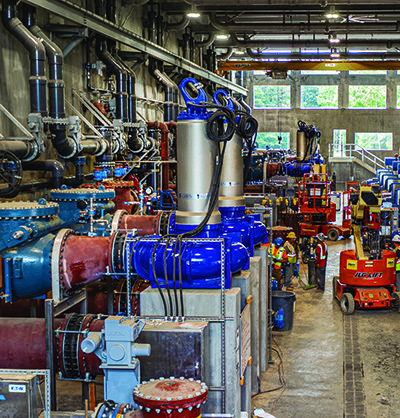
A water reclamation facility in Georgia has been the focus of an ambitious upgrade, providing an opportunity to deploy the latest technology. Bryan Orchard takes us through aspects of the revamp including the specification of pumps.
When aging wastewater treatment plants reach a time when they are in need of upgrading or expanding to meet increasing demands on their capabilities, opportunities arise to consider introducing new technologies to replace old equipment and build new facilities that improve operational reliability. Where a plant is several decades old, it is possible that certain mechanical elements of the original build may no longer be available, or have been superseded by new designs and technologies.
The Big Creek Water Reclamation Facility in Fulton County, Georgia, USA now in its final stages of construction is making the most of the latest technologies on the market. Constructed in the early 1970’s, Big Creek had at that time a daily flow capacity of 2,840m³ (0.75 US mg). However, by 2015 the facility had reached 80% of its average daily flow capacity so by law its operators, Fulton County Public Works Department, had to formulate plans to upgrade and increase the capacity of Big Creek. The plans had to ensure that the project would improve operational reliability, meet existing and future drinking water and wastewater treatment demands, and comply with strict discharge levels into the nearby Chattahoochee River.
The result was the implementation in 2018 of a $300 million progressive design-build upgrade incorporating advanced Membrane Biological Reactor (MBR) technology. This technology will produce significantly cleaner discharge water and contribute to increasing the current flow capacity from 91,000m³ per day (24 US mg) to 144,000m³per day (38 US mg) and be fully operational in 2024.
Handling the vastly increased flow levels has inevitably involved a major review of the existing fluids handling capabilities and those associated with the Returned Activated Sludge (RAS) produced by the MBR process. This aspect of the project has involved Georgia and Alabama-based Pump & Process Equipment Inc. (P&PE), an authorised representative of KSB. P&PE has had a close working relationship with Fulton County over many years, supplying the Big Creek plant with several pump types, primarily wastewater process pumps manufactured by KSB.
An influential aspect of the new treatment plant is that it operates by gravity. Because the wastewater entering the plant is received from external pump stations, and taking into account the significant elevation change across the site, the design of the new facility reduces the need for pumping at several parts of the plant. This even includes the flow through the membranes of the biological reactor, resulting in significant long-term operational savings as fewer pumps reduce power costs.
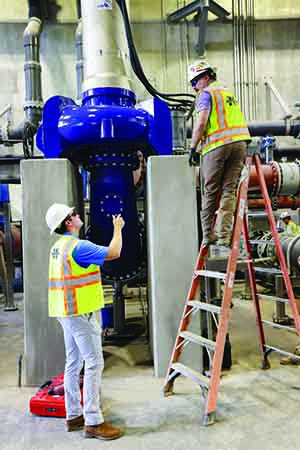
However, certain special process applications do require pumps. Power is a major issue for operating the RAS pumps and the blowers used for process aeration and membrane cleaning. This equipment requires large pumps with motors up to 250hp.
When the expansion project was first discussed in 2018, P&PE was in place to present the capabilities of KSB pumps for the process fluid handling applications around the new plant. The MBR plant using Kubota technology provided the opportunity to highlight the proven capabilities of KSB’s KRT dry pit, internal self-cooling submersible pumps for handling RAS (Fig.1). Working with Kubota Engineers and KSB, proposals and design data including recommendations for RAS and CIP pumping requirements were submitted to Fulton County and Brown & Caldwell (the project engineer). The advantage of KSB KRT dry pit submersible pumps was that they met Fulton County’s requirement to reduce the use of wastewater for cooling.
High-spec sludge handling
“The KSB KRT pump (Fig.2) has been designed specifically for wastewater treatment applications where solids-laden fluids are encountered and clogging is a challenge,” explains Bill Uhrig, Vice President at P&PE. “Suitable for both dry and wet pit installations, this robust pump series provides a variety of material offerings, several types of impellers and premium efficiency motors. These cutting-edge technologies were detailed in the project tender specifications drawn up by the plant’s design engineers, Brown & Caldwell.”
Selecting pumps for RAS has been treated by P&PE as a separate project, largely due to the complex design and operating requirements of the station. “Our response to the brief was to supply eight vertically mounted KRT 235HP dry pit submersible pumps (Fig.3) for recycling biologically active sludge from the membrane basins back into the treatment process at the Biological Nutrient Removal (BNR) basins,” explains Bill Uhrig. The pumps are located in the membrane gallery and share the space with all of the large aeration and agitation blowers
Accommodating high flow
The RAS pumps are the largest pumps at Big Creek. “Utilising duplex stainless steel, three-vane non-clog impellers, each pump has a 20-inch discharge and a 30-inch suction line feeding them,” says Nick Abbatiello, KSB’s Southeast Water Market Regional Manager. “The rated duty point is 658m³(17,385 US gpm) @ 31.3ft TDH and the pumps will run at different speeds to accommodate the initial flows, but are sized for the ultimate build-out of the facility,” says Abbatiello. “The challenge of this application has been accommodating the very high flow when there is only 32ft of head. This means that each of the pumps is brought on stream in sequence as the flow increases to handle the demands of the plant.”
Two KSB Sewatec 50HP end suction centrifugal pumps have also been installed in the MBR gallery for membrane CIP chemical cleaning. These are rated for 5.68m³(1,500 US gpm) @33ft TDH and when activated they re-circulate the cleaning solution for future reuse.
Process duty pumps
P&PE has also provided contractor Archer Western with a range of KSB KRT pumps for specific process duties. These comprise three different types of impellers for various applications, together with three different types of motors to meet all specific requirements. The design of the K-type, E-type and D-type impellers and the pump housing ensure a free flow of solids-laden liquids and combined with high-efficiency motors, they deliver significant operating cost savings.
In the majority of applications the pumps incorporate K-type impellers and come in various sizes and flow capabilities for handling different processes throughout the rest of the treatment works. These include pumps for digester basin recirculation pumping, servicing the de-watering, filtrate and building drainage system, servicing the equalising basin return water, anaerobic feeding, fine screening, RAS anaerobic screening and RAS rescreening. Three of the six areas of use are being equipped with closed-looped, internally recirculated glycol for a dry type installation. These are similar to the RAS pumps, but on a much smaller scale.
The fine screening pumping application uses E impellers (single vane non-clog design), providing high pumping efficiencies, low HP requirements and use premium efficient motors. Elsewhere, D impellers (open, diagonal single vane design) are being used for digester basin pumping. An ideal solution for pumping fluids with higher solids contents, these pumps are also being provided with special high-temperature rated motors, good for liquids up to 60⁰C (140⁰ F).
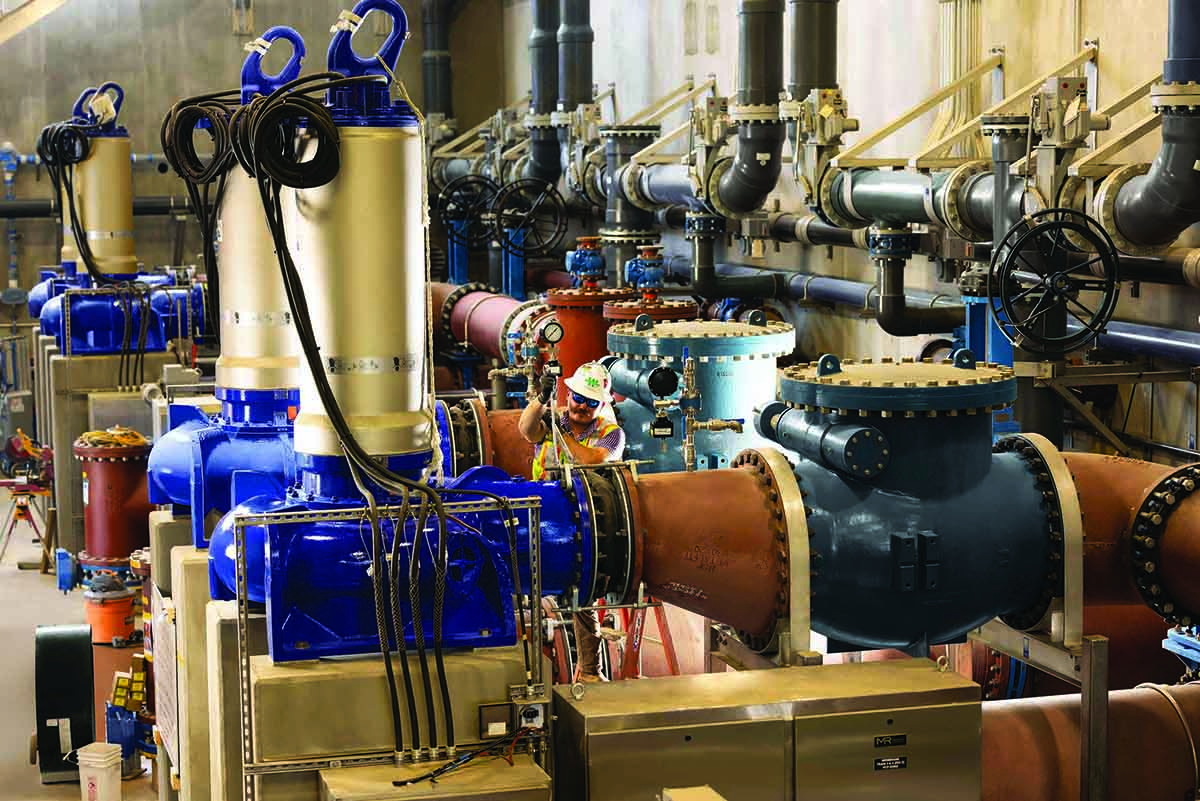
Serving one of the fastest growing regions around the Atlanta, Georgia area, the Big Creek Water Reclamation Facility upgrade and expansion, with a service area of 70 square miles, is the single largest project in Fulton County’s history. Through years of planning, collaboration, and a culmination of vision, engineering, and equipment, Fulton County businesses and residents will soon be the beneficiaries of this sweeping design-build project providing plentiful and clean water and waterways for years to come.
“By the middle of 2023 we had supplied 45 KSB pumps,” says Jimmy Mulvaney, President of P&PE. “Throughout the year-long intensive process of design considerations for the RAS pumps in particular, and through collaboration with the Design Build Team consisting of the Engineer (Brown & Caldwell), the contractor (Archer Western), Fulton County Engineers, KSB Inc. and their colleagues in Germany, we have been able to meet the difficult hydraulic conditions to the satisfaction of all the involved parties.”
Cooperative effort
Commenting on the project, Roy Barnes, PE, Deputy Director of Public Works, Water Reclamation says: “We have been impressed by the relationship between all the parties involved in the project, which has been well managed by the contractor. I am grateful for the effort that KSB exerted particularly during COVID, as this gave us concerns about delivery dates being met. Because of access to parts of the plant, it was essential that the pumps had to be installed while the building work was going on. They worked it out and the pumps arrived right on time.”