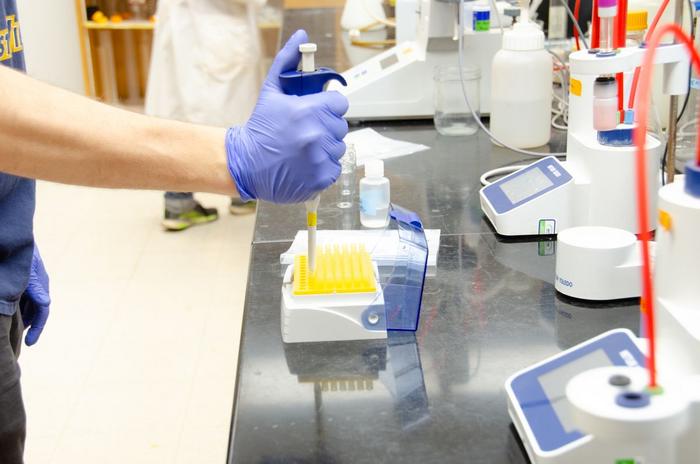
Simulations demonstrate the use of two kinds of industrial wastewater to decontaminate each other has the potential to slash a power plant’s total water use, according to a group at West Virginia University, which has published a paper on the topic.
The researchers modeled various scenarios for using “cooling tower blowdown” and “produced water” to treat each other. Cooling tower blowdown is wastewater produced by thermoelectric power plants, while produced water is created by hydraulic fracturing mining for oil and gas. The cotreatment process yields valuable byproducts as well as water that’s clean enough to be reused in power plant cooling operations. The study’s findings were published in the journal Desalination.
According to lead author Hunter Barber, a doctoral student in chemical engineering at WVU, no other industry in the U.S. uses as much water as thermoelectric power generation.
“Our cotreatment process reduces demand for chemicals to soften wastewater,” Barber said. “The treated water also has very high potential for reuse — treated water can be directly reused after cotreatment to make up 99% to 100% of the original volume of blowdown water, and that’s without optimizing or exploring different designs.”
Presently, power plants draw fresh water from a surface water or groundwater source, run it through the cycle to generate steam and electricity, then minimally treat it and discharge it back to surface or ground water.
“Our approach is looking to close that cycle,” Barber said. “Instead of discharging the water, we treat it, and instead of drawing from fresh water, we recycle treated water back through.”
The project cuts down on ther quantity of purifying chemicals required to treat the largest wastewater byproduct of the oil and gas industry, known as produced water, which is used in treating the power plant’s cooling blowdown.
“In the Southwest especially, but also in the Marcellus Shale and Appalachian regions, you have oil and gas wells drilled deep into the ground,” Barber said. “Once you pull all oil and gas from a well, it’s just an open cavity in the earth. You have polluted produced water that will take a high effort to treat or you can inject it back in that reservoir. However, injecting it involves seismic activity risk and contamination risk from heavy metals leaching into the ground.”
Co-author Lian-Shin Lin, professor and chair of the Wadsworth Department of Civil and Environmental Engineering, has led the development of the cotreatment process. He pointed out that produced water is saltier than ocean water. “Treating or disposing of that water is difficult and expensive. And an energy producer’s business is focused on producing shale gas and oil — they don’t want to care about water. It’s a liability for them,” Lin said.
“This cotreatment scheme offers a way to manage produced water and recover resources from it. For the energy industry that means, essentially, their produced water problem can disappear.”
Lin’s lab works with produced water from a shale gas well near Morgantown and cooling tower blowdown from Longview Power Plant. Because the experimental samples Lin uses are small relative to the volume of water a power plant requires, Fernando Lima, associate professor of chemical engineering, said they saw a need for a techno-economic, environmental and process systems analysis that would “scale the cotreatment concept up as much as possible, so it can be integrated into power plants or other wastewater treatment solutions and optimized with regard to operating costs, capital costs and energy utilities.”
Through process modeling, the researchers have been able to consider changes to power plant design and topology and evaluate different types of wastewater treatment processes before trying them in the lab. Simulations for different treatment processes allow them to optimize both the economics and the technical aspects of cotreatment.
“Collaborative research joining process modeling and experimentation is critical for the future of wastewater treatment because not a lot of detailed work has been done in modeling and optimizing these cotreatment processes, which involve very specific water chemistries that aren’t simple to capture,” Lima said.
Barber said he believes their model demonstrates plenty of upsides for power plants looking to implement wastewater cotreatment.
“A power plant likely already has dedicated personnel and equipment for treating its cooling blowdown. By becoming self-contained, they no longer have to draw from a water source. When they close the cycle, they no longer have to deal with potential negative economic consequences from discharging water that wasn’t clean enough according to EPA regulations,” Barber said.
“Instead, they can utilize the waste to make something beneficial and cost-effective. In terms of progressing the sustainability of many of our water demands, I think blowdown reuse is on the horizon for a lot of these facilities.”