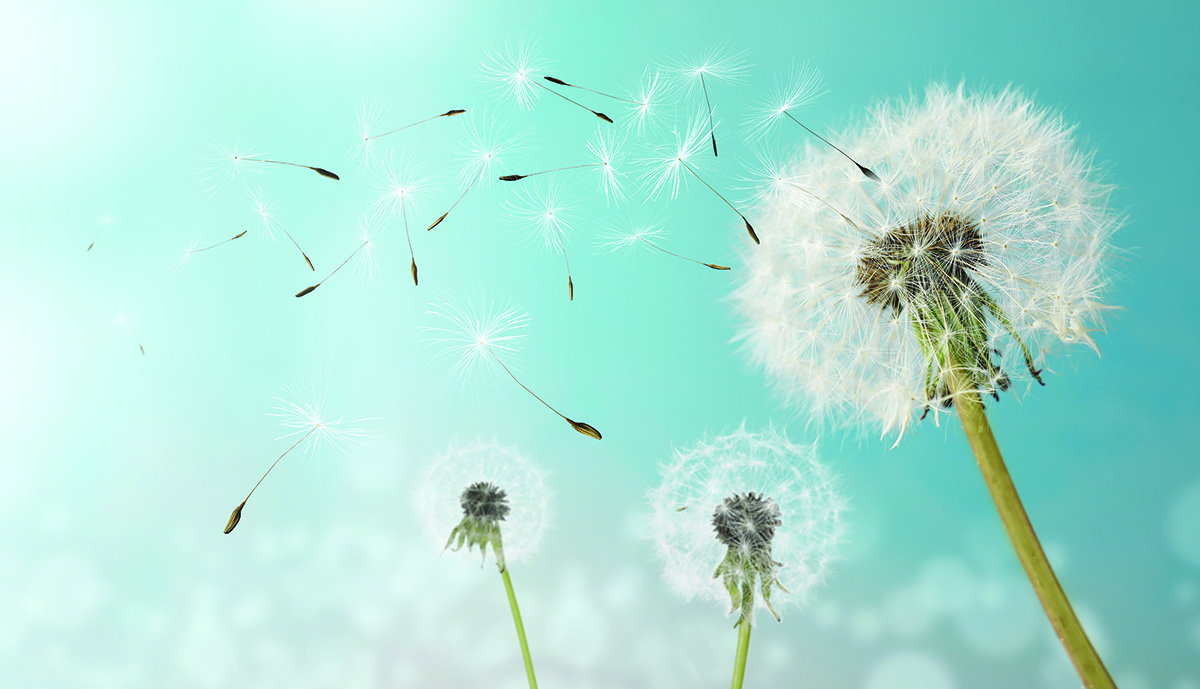
Bio-inspired engineering has grown in profile in recent years, and is being used to address traditionally intractable problems, as Envirotec discovered.
Engineers have been borrowing ideas from nature for a long time. Leonardo da Vinci’s ornithopter flying machines – based on observations of birds – are a classic example. It took a while for engineers to realize there were easier ways to launch a machine into the air than flapping a set of wings, but we got there in the end.
Such has been the relationship between these two domains: not a trouble-free marriage by any means, but an increasingly fruitful one. Recent decades have seen its formalization as a distinct branch in engineering.
A recent talk on the subject by Professor Adam Stokes conveyed some of the excitement and sense of possibility the field is currently generating, and showcased examples of the work being undertaken by his own Soft Systems Group, part of the Institute for Integrated Micro and Nano Systems in The School of Engineering at The University of Edinburgh.1
Stokes’ title of “Personal Chair in Bioinspired Engineering” is a nod to the fields’ growing recognition. His own multi-disciplinary pedigree – with a CV buttressed by no less than three undergraduate degrees (in biomedical sciences, engineering and chemistry) – hints at its enormous breadth, and inherent challenges.
Biology and engineering seem to stand apart, as approaches to understanding the world. The difference is breezily summed up by Professor Julian Vincent of Heriot-Watt University in a recent paper, with the observation that engineering is numerate, while biology is descriptive.
But a tangled provenance is undisputed: Electrical engineering, for example, has its origins in observation of the natural world, and the electricity present in the nervous systems of animals.
Stokes’ talk contrasted the two fields at one point with a slide showing an octopus tentacle next to a six-axis robotic arm – exemplars, perhaps, of their respective domains’ attempts to grapple with the world.
Engineers generally build things using components or sub-systems (like motors and rotary encoders) and in a manner that affords high precision and accuracy. It’s an approach that has yielded useful machines for performing dull, repetitive jobs, and which can work in dangerous or inhospitable environments, as he explained.
But you can’t build an octopus tentacle like that. The available sub-systems – motors and encoders, for example – can’t possibly match the ambition and sophistication displayed by this system. And just for good measure Stokes showed a video of an octopus squeezing through a tiny hole the size of a ten pence piece.
“As an engineer, I don’t know how to do this,” he said, adding that you can’t build something like this from motors and encoders. “What is it nature is doing that we’re not able to do? How can we copy it?”
Rather than simply relying on serendipity or open-ended brainstorming, recent years have seen developments towards a more disciplined approach. Julian Vincent, for example, has popularized methods like TRIZ (Theory of Inventive Problem Solving) in this field. TRIZ works with a set of 40 “inventive principles” – a finite list that purports to represent the available ways of solving problems.
He has constructed a database of the ways biology has managed to solve different problems – or “tradeoffs”, specifically (for example, speed vs accuracy, strength vs weight, and so on). Developers in this field can search the database when in need of inspiration. As Stokes explained, as long as you can phrase the problem appropriately, Julian can spark off ideas about how to solve it.
A flying start
One problem that nature seems to have solved, for example, is the ability to remain airborne without much energy or effort – exemplified by natural flyers such as dandelion fruit. By studying this natural capability, one project – called “Dandidrone: A Dandelion-Inspired Drone for Swarm Sensing” – hopes to overcome some of the challenges of using airborne sensors to monitor natural disasters or other inaccessible sites.
Recent work has shown that the porous wing of the dandelion leads to the formation of a fluid vortex, never previously observed. As a description on the project’s website puts it, the aim is “to unveil the underlying fluid mechanics mechanisms that allow the dandelion to remain airborne by exploiting the energy in the wind.”
The mathematical underpinning of much of today’s practical robotics is the Jacobian matrix, which allows engineers to map inputs to outputs, and thereby describe (mathematically) the behaviour of a control system like a robot arm.
A system like a six-axis robot arm will be describable using matrix calculations. The two distinct movements of rotation and translation (i.e., moving an object from one place to another) can be encapsulated in mathematical terms by matrices for rotation and translation, respectively.
Soft robotics brings in two additional matrices to describe scaling (i.e., what happens when something changes size) and shearing (i.e., when objects change shape but not size, as when a square becomes a parallelogram). These kinds of movements introduce the new capability for interaction – which, as Stokes puts it, “is very likely the answer to the question: ‘What do we want soft systems to do?’”
Do be soft
Being able to interact with the world opens the door for robots to provide support with care-giving and similar roles. One member of the group recently won a Scottish Edge award of £80k for his company, Konpanion, which offers a soft robot device that is intended to help people combat loneliness and anxiety.
Another company licenses the Edinburgh group’s patents to make grippers used in food processing – for handling products like seafood and chicken. The compliance (i.e., softness) of these grippers removes the need for precision, so the grippers can move very rapidly and grab a bit more wildly at an object. It’s much simpler than the alternative option of using suction devices, which also present a need for regular disinfection and cleaning because the open gas line sucks in bits of food and debris.
Building these kinds of systems seems to proceed along less deterministic lines than traditional robotics, where stable, known components give rise to predictable behaviour at the system level. Building soft robots involves more of a “let’s see what happens” approach, in Stokes’ telling. And the emergent behaviour can be interesting and complex, with potential utility that only becomes apparent after you’ve tried it.
Stokes gave examples such as the use of a simple balloon actuator. It can be constrained along one axis so that, when it inflates, it does so along one side more than the other. This can be used to create a robot with something like a back and four legs, which can walk around, and even do things like flattening down to limbo under a narrow gap.
When Stokes’ group first submitted these kinds of experiments to journals, about 12 years ago, one of the first comments to come back was “I don’t know what this is, but it’s not robotics.” Since then, he said, the field has grown, and there are now international conferences about soft robotics.
Soft actuators also seem to draw upon quite different materials to traditional robotics, including fluids, shape memory alloys, and electro-active polymers. Although Stokes’ excitement also seemed to derive from the possibility of using cheap, disposable materials – and this also changes the use case of robotics, introducing the possibility that it can be disposable. His own group has built robots from balloons, rubber bands and drinking straws, picked up from a local newsagent.
“Why? I don’t know,” he said. “Sometimes it’s worthwhile doing things because they’re interesting.” You can judge the utility once it’s been built.
Interestingly, he said, these are also robotic systems that can’t be simulated, involving as they do, things like complex thermodynamics in the compression of a gas, the complex properties of different elastomers (and how they behave under strain) and so on.
And it’s in the emergent properties where the useful behaviours appear, the stuff that might have some practical application. One video during his talk showed a starfish-like plastic robot that learned to kick a ball. Rather than a design approach where you’re specifying a precise movement in space for an end effector (like a robotic foot), you can allow the system to work out how to do it. In this case the robot could be asked to kick a ball, and to do so in the most efficient way. The project combined robotics, AI and reinforcement learning.
Novel materials seem to be an enabler. One focus of recent experimentation is the use of actuators that feature a continuous flow of fluid within the structure, in a closed-loop system. This allows very specific deformations of the material, and a high level of flexibility and versatility in the actuator – an advance on flow actuators that simply use a cyclic or rhythmic flow of air or liquid.
The group at Edinburgh has been working with “Fluidic Flowbots”, which exploit this kind of continuous fluid flow. And they have shown that complex robot behaviours can be designed with a much simpler control architecture. A recent paper demonstrates things like a bidirectional actuator, a gripper and a quadruped swimmer.
The design can be much simpler because complex action doesn’t necessarily require complex input or processing, unlike in conventional robotics where everything scales linearly (i.e. if you move from having five actuators to having 1,000, you will require 1,000 control lines, 1,000 transistors and so on). Nature doesn’t build things in this way – in other words, with the control system and the embodiment constructed separately. In nature these things are intrinsically blended with each other. “Nature does a good job of hiding complexity,” he said at one point.
This kind of soft robotics can be built from one material, without moving parts, and can even be biodegradable, said Stokes, holding forth the possibility for systems to be transient, and capable of being left to perform an action in an environment like the sea, and allowed to biodegrade.
Hydraulic logic
These fluidic systems can also be used to build circuits that perform the same functions as computing or digital logic – for example, logic gates, memory processors and the like. Stokes said these components “can be stacked together and embedded within these soft machines”. In this way, you can build systems with electronics-like functionality but without any actual electronics, or even metals. Such systems can be used in places where there is a high risk of explosion, or where there are very high magnetic fields (inside MRI machines, for example), or where there is a high level of radiation.
Nuclear decommissioning is one application where soft robotics can fulfil an urgent need. In places like the Fukushima Daiichi Unit 2 Reactor, conventional field robotics is needed to carry out essential maintenance tasks, using expensive and complicated equipment with a lifespan severely limited by the high levels of radiation. Much of its time is preoccupied with the processor-hungry business of simply navigating from point to point, with all the difficulties of robot navigation in an unstructured environment.
Instead of using conventional robotics (based on electronics), a project called Connect-R is using a system where everything inside is hydraulic. Modular robots build a cubic structure out of discrete blocks – a kind of “3-D Scalextric track in free space”, as Stokes puts it – which can then pass power and data to the different parts of the system. Small robots can move along tracks in the structure – using a standardised and simple form of locomotion – and perform tasks, without having to spend time planning how to get from one place to another.
Connect-R is a flagship project funded by Innovate UK, and undertaken by a partnership of industry, government and academia (including the University of Edinburgh and Royal Holloway University of London).
The future of robotics will be in hybrids, said Stokes, which combine elements of hard and soft robotics. Hard is best for precise positioning while soft robotics brings in opportunities for compliance (i.e., with the surface of another object), as well as speed and low cost.
Notes
[1] The talk “Following Nature’s Lead: Bio-inspired Technologies” was given on 5th December 2023 at the University of Strathclyde, an event organised by The Institution of Engineers in Scotland (IES). See https://engineers.scot/events/.