Jeff Borrman of Bioscope Technologies reviews the fate of components and materials used in electronic printed circuit boards, and introduces a process that he suggests as a game-changer: bioleaching.
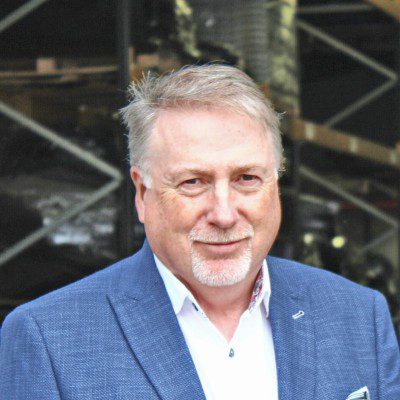
Many IT and electronics equipment manufacturers are still lacking when it comes to offering modular upgrades of equipment, leading to the rip-and-replace culture for hardware assets such as TVs, mobile phones, IT servers, laptops, network kit and cabling every 3 – 5 years. The underlying issue is that so far there’s been little or no incentive (financial or legislative) for manufacturers or their customers to facilitate asset reuse or recycling in a more sustainable way.
Manufacturers therefore remain vested in selling ‘net new’ rather than conserving or extending the life of existing hardware equipment.
Such wastage is amplified by a prevailing strategy to minimise the cost associated with IT disposal rather than find ways of maximising reclamation of components and precious rare earth metals which are in finite supply.
Here’s the thing: The pre-use manufacturing phase accounts for 70 – 90% of hardware equipment total embodied carbon. The virgin precious metals and rare earths being mined for use in PCB manufacture and their subsequent extraction at end of life through acids or smelting accounts for the majority of this. A PCB can contain as many as 60 of these components including gold, copper, silver and palladium. The UN puts the value of wasted rare and precious metals contained on PCBs at $62.5 billion per year.
Clearly, end users – consumers, businesses and data centre operators – do not have direct control over this. They are largely beholden to the supply chain stakeholders upstream who need to do much more concerning the longevity and reusability of equipment. However, their business customers along with lease finance providers need to be encouraged to accept and enable longer usage periods through regular maintenance programmes, refurbishment, resell and reuse. Furthermore, all concerned must pursue ethical and sustainable product end of life recycling practices.
In this regard, engaging the services of licensed and regulated WEE IT asset disposal (ITAD) operators can extend typical three-to-five-year product lifetimes by as much as another five years. Materials recovered such as gold, copper and steel can go back into manufacturing streams and once again become part of the technology manufacturing process, completely closing the lifecycle loop.
With this, a key success factor in effectively closing the loop is a more sustainable and ethical method of extraction and recovery of PCB materials. Currently the UK only recycles just over 30% of e-waste with all PCB materials exported overseas, the majority going to European, US and Far Eastern refineries which use non-sustainable pyro and hydrometallurgical processes – the rest end up in landfill or in the hands of unlicensed operators.
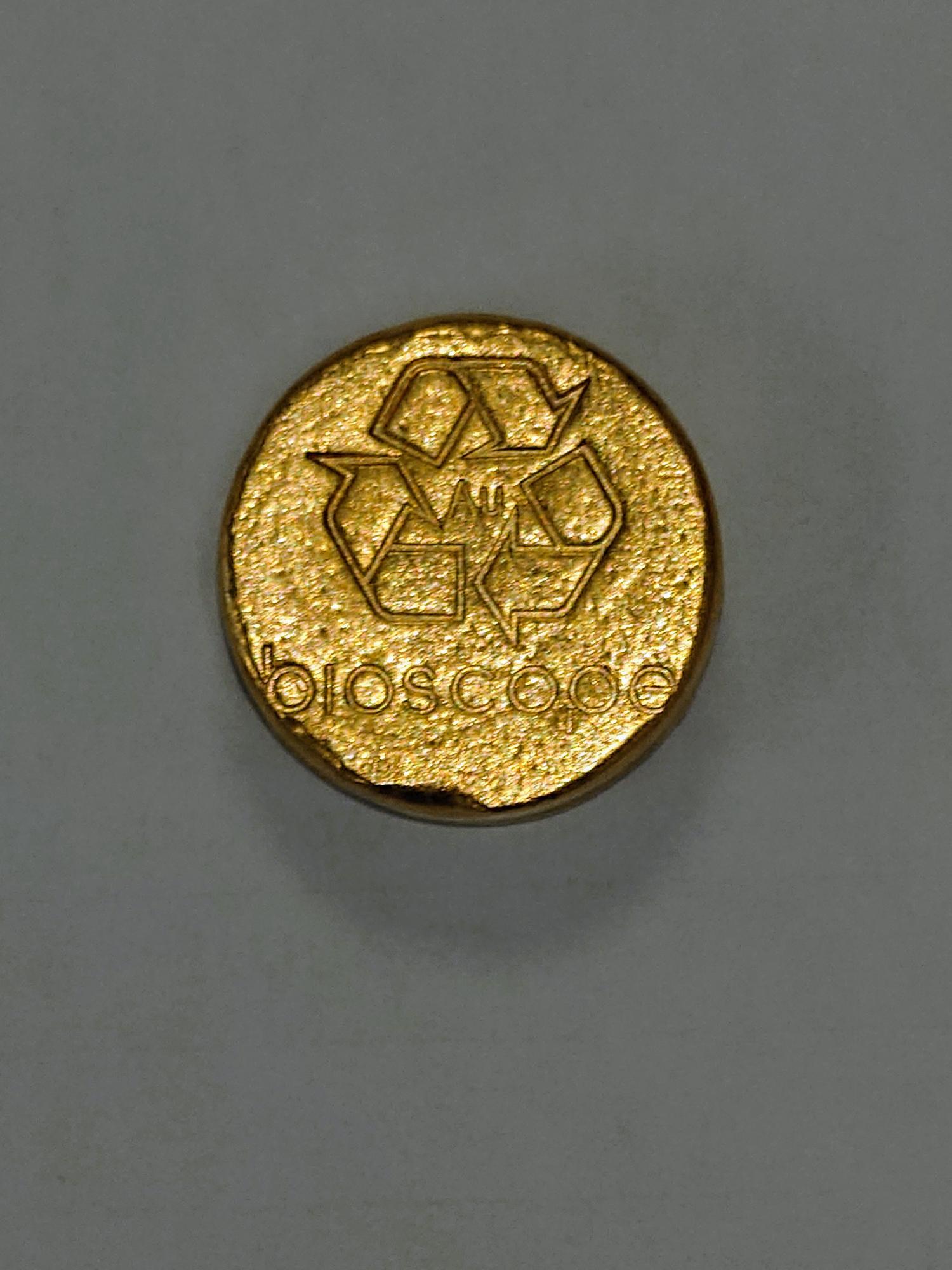
Bioleaching
To address this, bioleaching, a biotechnology process that uses bacteria to oxidise and leach out the metal content, is emerging as a potential game changer and an area which Bioscope Technologies is pioneering. The PCB materials are reclaimed and metal content recovered without use of high temperature smelting or harmful acids which use a lot of energy and water. The naturally occurring bacteria-based process therefore replaces traditional treatments and is as close to zero-emission as possible, without offsetting. By effectively creating a ‘soup’ the process dissolves metals and liberates them from the crushed circuit boards, followed by extraction via filtration and other means. It was important to create cyclical processes that can reutilise the reactive ingredients of the processes so minimising waste. We are now accelerating our bioleaching development to an industrial level, ensuring precious metals such as copper, gold, silver and palladium and other materials – including those in finite or limited supply – can be sustainably recovered and returned into the manufacturing supply chain.
Finding a way of recovering and sustainably patriating/repatriating the millions of pounds worth of valuable PCB materials currently going to waste presents a huge opportunity for both the UK’s and overseas’ governments. Putting this into some perspective, it’s estimated that 25 million mobile phones are discarded in the UK each year – recycling one million mobile phones can recover 16,000kg of copper,350kg of silver, 34kg of gold and 15kg of palladium.
For example, we’re working with the UK’s Critical Minerals Association (CMA) to jointly develop a long-term solution which will ensure many more critical PCB-based materials remain in the UK. Additionally, in Europe and North America, large recycling organisations, data centre operators, cloud providers and telecom companies will soon be able to access Bioscope’s patented industrial bioleaching processes and plant via licensing agreements.
Granular reporting
Underpinning any circular IT solution must be the ability to accurately measure and audit the entire Scope 3 C02e lifecycle for electronics and IT equipment. For business users and data centres, the equipment usage and post-usage stages of equipment lifecycle management are the only ways of reclaiming and redressing the energy expended during the IT equipment manufacture phase.
Until recently there has not been a data lake available that joins all these lifecycles together to enable organisations to form a net zero position. This is changing with the emergence of granular reporting tools that provide a full understanding of the environmental position. These will enable businesses and data centre owners/operators to drive decisions that support their own sustainability reduction targets as well as inform those of their customers – from equipment procurement to retention and at the disposal stage.
With the world’s generation of e-waste rising five times faster than the documented capacity to recycle it – 62 million tonnes of e-waste produced in 2022 – it’s time for governments, IT equipment manufacturers and business consumers to take more responsibility in helping solve the problem at scale and in a wholly sustainable way. Circular IT product lifecycle management is the key and as part of this, bioleaching. We believe for PCB metals extraction and subsequent refining it provides the missing link for closing the loop while helping ensure many more precious resources remain in use.
Notes
[1] UN GEM Report 2024