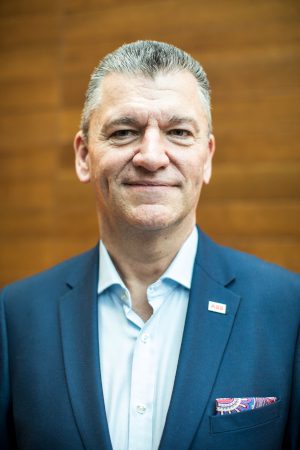
Efforts to ensure the continuity of today’s mission-critical industrial operations are blunted by the burden of aging and increasingly complex electrical systems. ABB’s Lee Todd explains how forward-looking approaches to equipment maintenance can reward organizations with optimized business continuity and greater sustainability as well as reduced costs.
Unplanned loss of production is a contingency that’s seldom welcomed by organizations, their customers and shareholders. Halting a chemical, pharmaceutical or other industrial process due to sudden electrical failure means an immediate loss in revenues. And aside from the short-term commercial penalties, businesses like data centers – where five-nines uptime is an imperative rather than a nice-to-have – face the prospect of deeper and longer-term impact to their corporate reputation.
Even a highly experienced maintenance engineer or plant operations manager may have little or no prior indication that critical electrical components are about to fail. While the first sign of an impending problem is often a tripped circuit breaker, that isolated event reveals next to nothing about the underlying cause of the issue. Reclosing the breaker may allow production to resume in the immediate term. But it won’t fix the underlying cause of a serious underlying issue that’s about to get a whole lot more expensive very soon.
The nature of modern business highlights the intrinsic problems associated with traditional electrical maintenance strategies. Routine equipment inspections are typically conducted at periodic intervals, typically accompanied by the prescriptive replacement of equipment or individual components according to a specified timetable. This regime assumes a mean time between failure for components that’s consistent and predictable. And this is a presumption that is far removed from the realities of plant operations where failure can, and often will, occur long before – or after – the manufacturer’s specified estimate.
Time-based maintenance strategies cannot guarantee that a particular part won’t fail before its allotted time. Equally, they’re an expensive and sometimes ineffective use of company resources. Replacing an aging component that’s still in perfectly usable condition, regardless of its stated working life, achieves little. It’s costly in terms of resources and human capital, tying up operations and maintenance staff on an unneeded swap-out while consigning a fully functioning part to landfill, months or years before its allotted time. And whether it’s needed or not, scheduled maintenance often brings productivity to a standstill for hours or days, biting into revenues and profitability that most businesses can ill afford.
Reflecting the increasing scale and sophistication of modern plant operations, the limits of time-based and reactive maintenance schedules are amplified further as electrical systems become larger and more complex. Industry’s progressive digitalization poses additional challenges, heightening the need for electrical systems to perform without interruption to avoid the risk of losing precious insights collected from instrumentation and control systems about process and plant performance.
The challenges of securing production continuity and resilience are further exacerbated by the need for organizations to embed sustainability and circularity across all areas of their operations. Competitive pressures and regulatory scrutiny mean that business owners face an imperative to improve their energy efficiency, reduce carbon emissions and minimize waste. Coupled with continued volatility in energy prices, these factors are encouraging more industrial organizations to power their critical electrical systems using renewable sources of energy. This can either be achieved by purchasing green electricity directly from utility companies or, increasingly, by businesses generating their own electricity on site. Installing generation capacity, often in the form of wind turbines or solar arrays, affords plant owners greater energy security as well as the opportunity to save on buying electricity from other sources.
But while this ‘self-serve’ energy strategy pays dividends for organizations’ sustainability – and their bottom line – it introduces its own additional challenges. Ensuring the reliable operation and management of a plant’s critical electrical systems becomes an even more complex undertaking when integration of renewable sources is added to the picture. In a survey of industrial organizations conducted by ABB in 2023, a significant proportion of respondents confirmed that they are struggling to deal with the complexities of managing multiple sources of energy including renewables. In the case of data centers, for example, 40% of those surveyed cited protecting the integrity of their power supplies as being among their most daunting challenges.
In common with many engineering-led industry sectors, an increasing skills shortage is making it harder to identify and retain suitably skilled personnel. Tens of thousands of veteran electrical systems experts are retiring, taking with them decades of practical experience and deep knowledge of highly specialized electrical systems found in factories, power plants and other industrial facilities. This pool of expertise is leaving the industry faster than it’s being replaced, leaving employers across many industries struggling to fill a yawning talent gap. Without this in-depth knowledge of complex electrical systems and their interactions with wider plant operations, a younger generation of newly-qualified can struggle with the challenges of optimizing and maintaining legacy electrical systems that may have been originally specified and installed before they were born.
In-house engineering and maintenance staff can also struggle with the rapid pace of electrification technology. Components, working practices and regulations are constantly evolving, with the result that specialist knowledge about complex systems can become quickly outdated. This is notably with the case with traditional reactive maintenance that’s heavily reliant on scheduled manual inspections. Staff often rely on their ‘gut instinct’ – honed with years or decades of practical experience and training – to make an accurate diagnosis and prescribe the most effective course of action. And if an unscheduled outage does occur at any time, the costs of lost production can mount quickly while locating a suitably qualified expert to attend site.
This changing operational landscape opens up new possibilities for industrial organizations to tap into the technical resources, innovation and experience of a world-class partner like ABB, complementing and enhancing their own capabilities. Through a consultative approach ABB can help shoulder the burden of caring for and optimizing complex electrical systems. With the provision of technical expertise and support services, this consultative approach frees up businesses to focus on KPIs like plant uptime and sustainable growth as they embrace the opportunities of energy transition and a net zero future.
ABB, for example, is helping industrial organizations proactively manage their efficiency and sustainability challenges through its Electrification Service business. This offers a holistic approach to maximizing the health of electrical systems via an overarching view of customers’ operational, commercial and wider strategic goals. Remote monitoring can be used to track the baseline health and condition of systems, assisted by data analytics to unearth critical insights about system performance. This intelligence can be harnessed to identify opportunities for energy savings and more efficient working practices. Just as importantly it can inform condition-based maintenance strategies. These prescribe service interventions on the actual performance of a device and its likelihood of impending failure, rather than relying on manual inspections performed at arbitrary intervals. As well as reducing the likelihood of unexpected system outages, this condition-based approach can offer significant cost savings, with fewer parts that are still perfectly serviceable being needlessly thrown out or sent to recycling