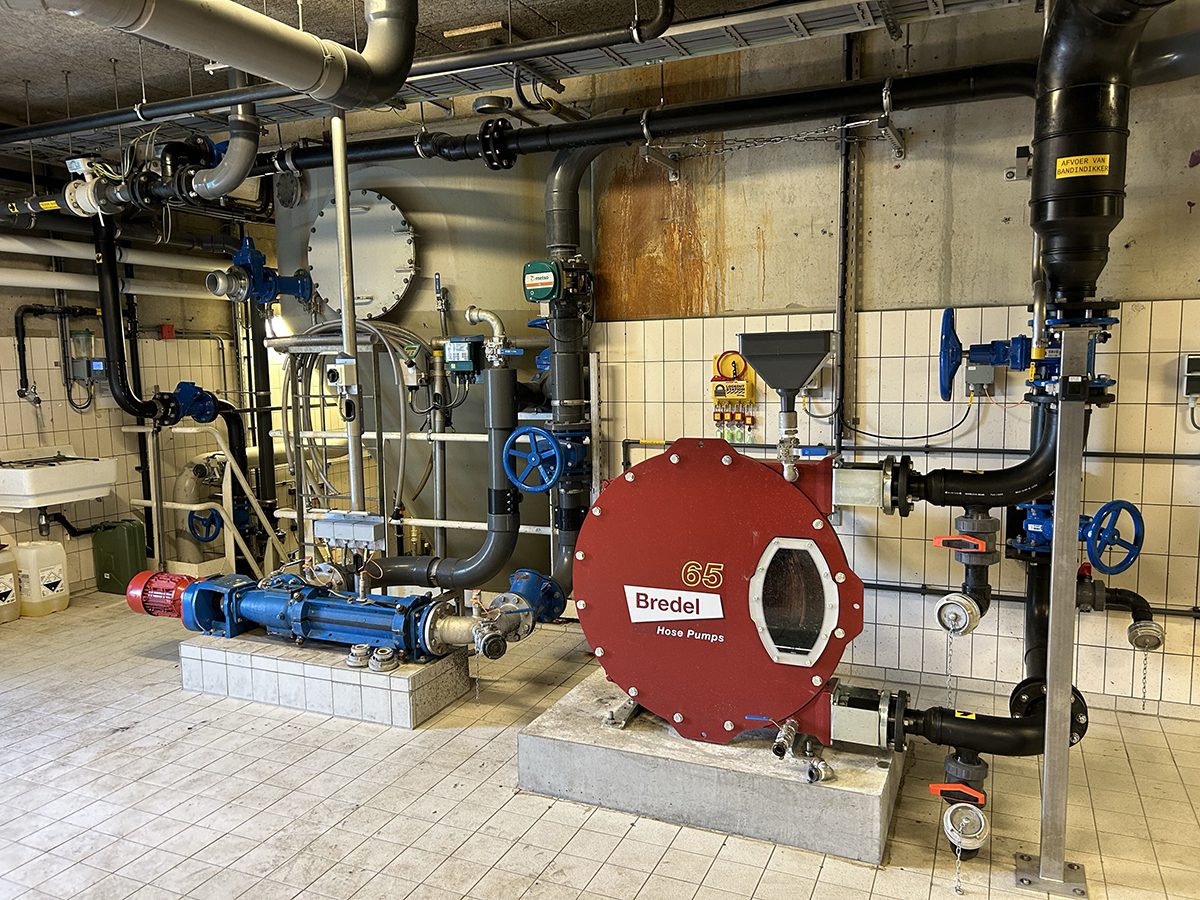
A Bredel hose pump has replaced a faulty progressive cavity pump at a water treatment plant in the Netherlands. Pumps manufacturer Watson Marlow provides details of the new solution and the goals of the associated redesign.
The new pump is being used to transfer thickened sludge in the production of biogas for Scheldestromen water board (Waterschap Scheldestromen).
Specifically, a Bredel 65 hose pump is transferring polymer-thickened sludge of 6 to 8% to tanks for fermentation at the water board’s treatment plant in Terneuzen, Zeeland.
A progressive cavity pump was proving too costly with a short lifetime for transferring sludge, lasting two and a half months on average for a stator and stator rotor, which resulted in maintenance downtime.
Dimitry Loof, Work Planner at Scheldestromen water board, said: “It was a consideration between costs and benefits to change pumps, and also a short service life of the progressive cavity pump. We wanted to extend the service life of the pump for this application.”
Over the course of the three months, the progressive cavity pump’s capacity continued to decline. This meant Scheldestromen water board had to speed up the progressive cavity pump to be able to use the same flow rate. When the pump was running at the end of its range, Scheldestromen water board could no longer absorb fluctuations in the process, resulting in a failure and a backlog in its total sludge processing. flow.
Longer lifespan means lower cost
The progressive cavity pump suffered a lot of wear in the stator and rotor due to sand, which caused pressure loss and a decrease in capacity. To replace a stator and stator rotor cost Scheldestromen water board a total of 3,000 euros (excl. VAT), as well as the time it took staff to do the pump maintenance.
The water board had to replace the stator and rotor with the progressive cavity pump three or four times per year.
Gertjan Dijkers, Process Operator at Scheldestromen water board, said: “The progressive cavity pump’s problems were largely caused by sand and the pressure pipe that was too small. The pressure pipe had a relatively high resistance. This was partly due to the long distance, a number of right-angle bends in the pipe and a relatively small cross-section of the pressure pipe (100 mm). This, in combination with a dry matter content between 6% and 8% (sludge and sand), ensured that the pump had a high back pressure. This caused the pump to wear out quickly.”
Due to the unreliable operation of the progressive cavity pump, Scheldestromen water board could not be certain it could process all the sludge supplied from the treatment plants.
Looking for a better performing pump with a longer service life, Scheldestromen water board met with Watson-Marlow Fluid Technology Solutions (WMFTS) to explore how Bredel hose pumps could be a solution. They also contacted another peristaltic pump supplier, a lobe pump manufacturer and a progressive cavity pump manufacturer.
Gertjan Dijkers, Process Operator at Scheldestromen water board, said: “We just wanted to be able to run for at least three months with the flow rate that we have to run. We have found that a Bredel hose pump can run for over three months before its capacity starts to decrease. The biggest advantage is that the hose pump simply does what it is supposed to do for over three months.”
Bredel hose pumps have no rotating parts to clog or wear with the sand, which considerably reduces maintenance and labour costs. As well as costs, the Bredel hose pump brings ergonomic benefits. Scheldestromen water board did not have to increase the diameter of the piping, which built up too much with the progressive cavity pump. The accessibility of the pump is much better with the Bredel, and because of the suction capability of the Bredel it is located on the ground floor.
Scheldestromen water board calculated it can have a return on investment on the Bredel pump in four years and make considerable savings on maintenance compared to the previous progressive cavity pump.
Maintenance costs and labour costs of the progressive cavity pump per year (average taken over six years) were 9,420 euros, according to the water board. The group also calculated it will make 42% savings in annual maintenance costs with the Bredel hose pump, compared to the previous progressive cavity pump. Another benefit is that a single operator can now change the pump hose without another co-worker’s assistance.
Ed Zorg, Industrial Sales Engineer for WMFTS in Netherlands, said: “The other options were not a solution. The lobe pump had difficulty delivering high pressures above 4 bar, and the parts would wear out. The other manufacturer of peristaltic pumps did not have a pump available with the right size for this application as a test setup.
“Another important reason why Scheldestromen water board chose us was the relationship we developed with them. We were able to quickly provide a demonstration pump from our Bredel factory, so they could look at it, and then we were able to make some tweaks to the pump for them before delivering it. That collaboration and quick response for a demo pump was important.”
Biogas production
Biogas produced by the fermented sludge is burned by the treatment plant’s own combined heat and power plant. As a result, 80% of the treatment plant is supplied with self-generated electricity. The fermented sludge is processed into solid digestate and then burned. As the Bredel can pump more thickened sludge than the progressive cavity pump, Scheldestromen water board can now produce more biogas.
Dimitry Loof, Work Planner at Scheldestromen water board, said: “If we ran into problems due to the progressive cavity pump, we were forced to change to slow down the thickening process and thicken below 5% dry matter, which could jeopardise the entire process. If we pumped too little dry matter to the fermentation tank, the residence time in the fermentation tank was shorter. We want the organic matter to be broken down as much as possible, and that requires a longer residence time. The disadvantage of a shorter residence time in the fermentation was that we also produced less biogas. And because of the limited operational reliability of the progressive cavity pump, the maintenance costs were also higher than normal.
“With the Bredel we can run higher dry substances on the belt thickener and we can even send a higher flow rate to the belt thickener.
“With the Bredel we don’t run with a little lower in dry substance, we just stay high, which is also an advantage. When you put higher dry matter into your fermentation tank, it results in better fermentation. The more water you put into fermentation tanks, the more you must heat. The drier the dry matter content, the less water you have to heat. This means it costs less energy to heat the fermentation tank. In the summer this problem does not occur, but in the winter you save a lot of energy because you have to heat less, so that is a big advantage.”