In what’s described as a landmark project for the construction industry, the first lower carbon concrete solution from sustainable technology firm, Recycl8 and construction materials company, Breedon, has been laid at Veolia’s Ling Hall Incinerator Bottom Ash (IBA) processing site in Warwickshire.
Veolia and Danish recycling firm Meldgaard’s joint operation at Ling Hall is processing IBA from the nearby Battlefield Energy Recovery Facility to produce 50,000 tonnes of secondary aggregates annually. This material is managed by Meldgaard and combined with Breedon’s specially designed concrete mix with Recycl8’s R8 Mix to deliver a high-performance, lower-carbon alternative to traditional concrete.
The IBAA/R8 concrete solution has been successfully laid on the extension pad at Veolia Ling Hall by TG Beighton. This initiative, the first of its kind in England, was undertaken with full permission from the Environment Agency (EA) as part of a collaborative effort to push the boundaries of sustainable construction.
The new concrete used at the Ling Hall site demonstrates the practical and environmental benefits of using IBAA in bound surfaces, says Veolia. While IBAA is widely used in the construction sector for civil engineering projects under the Regulatory Position Statement (RPS) protocol, this project is suggested as a step-change in proving IBAA’s viability in concrete production, and in providing a sustainable and performance-driven alternative to virgin aggregates.
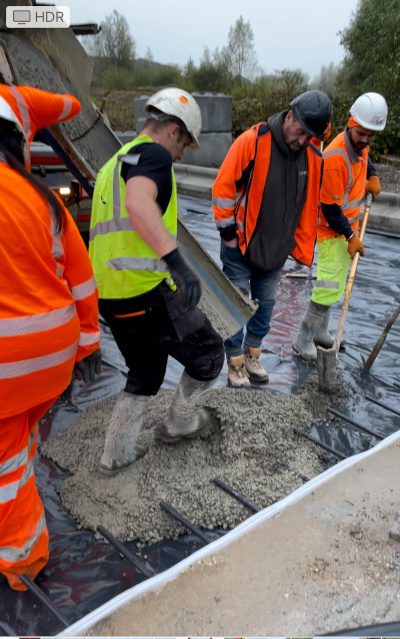
Designed to enhance the performance of IBAA in concrete, the R8 Mix is said to provide a proven, environmentally friendly option for construction companies looking to reduce their carbon footprint, as each tonne of IBA derived material saves around 30kg of CO2 emissions. Recycl8’s expertise in repurposing industrial waste into valuable construction materials ensures that the concrete is both environmentally sound and meets the rigorous performance demands of modern infrastructure projects.
Commenting on this latest development, Donald Macphail, Chief Operating Officer – Treatment said:
“To lower carbon emissions, and advance progress on the net zero targets, industry is rightly looking for new ways to lower the carbon footprint associated with construction. To support this aim it’s essential to deliver materials and solutions that can lower environmental impact, and this latest innovation is a clear example of how we can provide new sustainable alternatives.
By processing bottom ash, from the treatment of non recyclable waste, we can deliver an important source of secondary aggregates for the 90 million tonnes of concrete used annually in the UK, lower the dependence on virgin resources, and reduce carbon emissions”
Mark Gillespie, Managing Director of Recycl8 said: “We are thrilled to be part of this innovative project. This is a powerful example of how industrial by-products, when combined with cutting-edge R8 Mix products, can drive the construction industry toward a greener future. The Veolia Ling Hall extension pad project demonstrates the versatility and strength of IBAA/R8 Mix concrete in real-world applications, showcasing a true circular economy offering. With the support of the EA, this initiative sets the stage for further testing and validation, paving the way for IBAA to become a like-for-like alternative to part-replace virgin aggregate in concrete production.”
Nick Farrell, Regional Manager for Breedon added: “Collaborating on this project has allowed us to test a product that could truly change the game for sustainable construction. The IBAA/R8 Mix concrete which we designed and developed not only reduces the reliance on traditional materials, but also offers a high-performance recycled low carbon solution for the industry.”
Sarah Lakin, UK IBA Manager at Levenseat/Meldgaard said: “We welcome this exciting development. We continuously seek innovative ways to repurpose IBAA, a by-product of the Energy from Waste process. We’ve long seen the potential of IBAA, and combined with the R8 mix, we are confident that this material can play a key role in creating more sustainable, low-carbon construction solutions. We are very grateful to Veolia for affording us this unique opportunity to demonstrate the viability of our solution.”