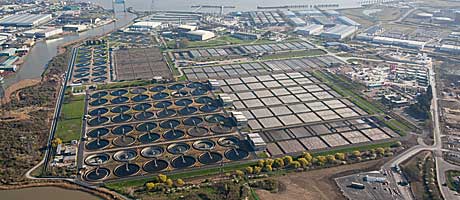
“We compared the dissolved oxygen meters from a number of vendors and chose the ABB meters as the most cost-effective solution,” explains Howard Smith, the instrumentation, control and automation manager on the project for main contractor Laing O’Rourke. “We were also working to a tight programme and the key was to deliver as fast as possible.”
The new installation includes 28 dissolved oxygen systems in total, made up of 16 AX480 single-input analysers and six AX488 dual-input analysers, all of which are controlled from a central computer using on-board Profibus communications. The rugged design of both analysers makes them suitable and safe to use in harsh environments. With little maintenance required, they were seen as ideal for the fully-automated control scheme at Beckton.
The site is one of the largest sewage treatment works in Europe, serving 3.5 million people and discharging its effluent into the River Thames. The new control system is part of a £190m programme upgrade that will enable the site to treat up to 60% more sewage by the end of March 2014. This will enable it to handle storm water as well as a serve a growing population.
ABB’s AX400 analysers satisfy a range of process monitoring and control applications. The complete range encompasses solutions for pH/Redox (ORP), conductivity and dissolved oxygen. AX48 instruments enable continuous measurements of one or two dissolved oxygen points with simultaneous local display and retransmission. They can be used with 9408 Series immersion, submersion and self-cleaning floating-ball sensors providing measurements that are said to give exceptional accuracy and performance.
AX400 Series units are available for either wall-/pipe- or panel-mounting and are rated to IP65. All versions are supplied with two, fully-isolated current outputs as standard, which can be assigned to the measured parameter, sample temperature or any appropriate calculated variables. The analyser range also comes with PROFIBUS DP capability, providing users with remote access to a greater range of process data at the field level.
Operating with dual inputs, the AX488 can monitor two continuous measurements thus reducing initial expenditure, saving space and minimising installation costs when compared to using two individual analysers, a capability that provides on-line validation of the process measurement. Making two simultaneous measurements and configuring one of the set points as a difference alarm provides continuous on-line checking and early warning of malfunction of the measurement. Alternatively, both measurements can be compared and an average value calculated and transmitted via the analog output.
The entire sensing loop is regularly self-monitored for short circuits and temperature element faults. The instrument incorporates a non-volatile memory, eliminating the need for battery back-up, and line-voltage supply filtering to minimise the effects of mains-borne interference.