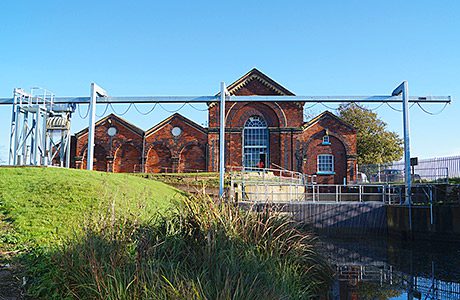
MAINTAINING the land drainage scheme in Lincolnshire is an important task for the Environment Agency (EA) and the pumping stations used to control water levels are protected by weedscreens to prevent damage to the pumps.
The equipment at the Dirtness station had been in service for over 60 years and was beginning to pose increased maintenance costs as well as potential health and safety concerns for the operators. The solution required the installation of a new, reliable system that would reduce the overall operating costs and improve safety.
Originally housing a beam engine produced by James Watt, the pumping station at Dirtness is a Grade II listed building which has been performing crucial water level control operations for nearly 150 years. The original steam equipment was replaced in June 1928 with the current equipment being installed in October 1952, which included a rotary screen designed to remove the debris from the water and deposit it on the bridge over the watercourse.
Problems with the old screen
The design of the old rotary screen required a small tractor to regularly remove the resultant debris from the bridge. However, as the tractor equipment had grown in size so the mechanised method had become impossible, so the more recent method had involved reverting back to the trusted wheelbarrow. In addition, when the temperatures dropped in winter, ice would build up on the screen and reduce water flow through the station. This required regular intervention by the maintenance staff to break up the ice to ensure the pumping station operated efficiently.
The solution: An automated weedscreen
The EA brought in ECS Engineering Services, with whom it has an on-going working relationship, to deliver an improved, more reliable solution which would reduce maintenance costs and provide an automated weedscreen solution. ECS suggested the installation of a Landustrie automatic screen cleaner which could provide for all the immediate requirements of the EA and would be covered by an initial warranty and continued maintenance support.
ECS delivered a turn-key solution which included the removal of the obsolete equipment, additional civil engineering to prepare the site, complete mechanical and electrical installation as well as testing and commissioning. All of this had to be completed in the most discrete and sympathetic manner so as to follow the guidelines for the Grade II listing.
Having removed the original weedscreen, ECS needed to use divers to modify the bottom of the watercourse to provide a flat base for the new screen. Additional civil engineering works were required to prepare the concrete bases for the overhead gantry and to install underground ducts for the electrical cabling. Once this work had been completed the task of erecting the steelwork could begin and would only take 3 days to complete.
Getting up and running
Electrical work to provide power, ultrasonic level control and telemetry was completed and connected to the central control panel. Testing and commissioning was completed along with operator training to ensure efficient and reliable operation every day. The project was completed with the installation of additional hand-railing and perimeter fencing to secure the site and provide improved operator safety.
The completed project has provided the EA with a much improved weed screen with an automated cleaning system which greatly improves the reliability and reduces maintenance costs. The new system performs a cleaning cycle each time it is triggered, which can be when the pumps operate, on a timer or based on a water level differential measured by the ultrasonic sensors. It can also be operated manually using a plug-in hand held console. This choice of operation makes the cleaning system very adaptable and suitable for a variety of applications.
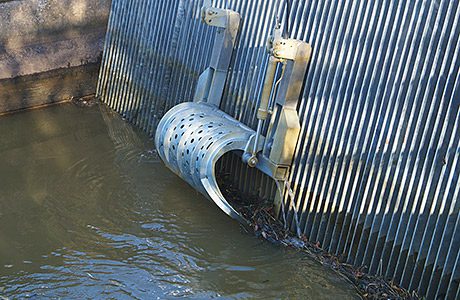
The cleaning cycle involves the grab moving from its parked position to a point above the weedscreen where it is lowered onto the screen to a point below the surface of the water. The grab is then closed hydraulically and raised out of the water before traversing along the gantry to a point above the skip, where the weed is deposited. This procedure is repeated until the full width of the screen is cleared.
The system is built to provide reliable operation, with a minimum of components to simplify the maintenance requirements and as such does not rely on proximity sensors for the control of the carriage and hoist. Instead, it uses counters which are programmed via the control panel and provide a more accurate and reliable system of operation.
The installation is connected to the local telemetry system to provide feedback on the current operation status as well as a requirement for operator intervention. The cleaning system can also be operated locally by hand with the push-button pendant which is plugged into the system at a point close to the screen to allow the operator a clear and safe view of the operation.
Once installed and tested, training has been provided to the EA staff who are working on this and other sites in the area. The completed solution has greatly improved the reliability of the site as well as removing the manual handling requirement and its reliance on regular operator intervention.