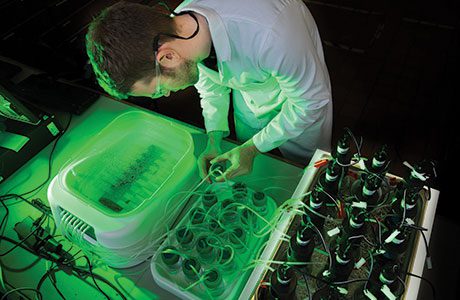
By integrating an anaerobic digestion system into the production process, food and beverage manufacturers can improve sustainability and generate increased profit. Nick Simpson of AD solutions provier Ondeo Industrial Solutions introduces AD and offers a few initial thoughts.
AT present, Anaerobic Digestion (AD) is one of the hottest topics in the food production and food processing sectors. Government initiatives, such as the Anaerobic Digestion Strategy and Action Plan, are driving the implementation of AD technology, with a significant increase in technology installation and usage in recent years. “The coalition is committed to being the ‘Greenest Government ever’ and achieving that will in part mean substantially increasing energy from waste through Anaerobic Digestion (AD),” states the AD Strategy and Action Plan, published in 2011. “This offers a local, environmentally sound option for waste management, which helps us divert waste from landfill, reduce greenhouse gas emissions and produce renewable energy, which could be used to power our homes and vehicles. Farmers and gardeners can also benefit from the fertiliser produced, returning valuable nutrients to the land.”
What is it?
AD is a process by which, in the absence of oxygen, microorganisms break down biodegradable material. It has advanced rapidly as a technology for wastewater processing in the past two decades. An important development was the realisation that bacteria in biological treatment forms pellets of a similar size to a pea. From this came the move to employ AD in processing high strength effluents in small, highly efficient reactors, where previously it was only used to process larger solids.
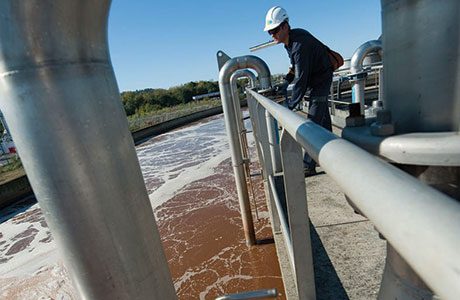
What happens?
In the anaerobic biological treatment process organic carbon is broken down, generating methane, which can be recovered to produce energy. Typically, removing 1 ton of COD (Chemical Oxygen Demand) has the potential to produce around 3,500 KWh. A variety of anaerobic biological digesters are in common use, with different areas of suitability.
A contact reactor, for example, is more often the norm for processing chemical, pulp and paper residue, and the treatment of complex food juices. A fluidised bed is used to treat evaporation condensate and alcohols, while the use of granular sludge with an Upflow Anaerobic Sludge Blanket (UASB) is a common approach to treating effluent from sugar refineries, wine producers and breweries.
Deciding when it’s suitable
While AD technology has the potential to deliver important benefits to many businesses operating in the food and beverage sector, it is impoprtant to realise it may not always be suitabe. AD processes are sensitive to even the slightest changes in wastewater input quality and, because wastewater contains microorganisms, feedwater may require treating with nutrients, which can be a time consuming and costly investment, to provide the right level of nitrogen and phosphates. It is also essential that AD is operated at closely monitored temperatures, given the combustible and volatile nature of methane, which needs to be handled with care. So in some cases, the true costs of installing and running an AD system may be high compared to the payback.
One way to assess the technology’s suitability is to consult with an industrial water solutions expert. A solutions provider may well be a better source of impartial advice than a manufacturer.
A solutions provider can also evaluate factors such as potential gas yield, microbiology and inhibition, cost of design / build and financial returns to establish the correct specification for you.
• Ondeo Industrial Solutions is part of Degremont Industry.