Few engineered components are as steeped in tradition as the pump. But how does this fit into the age of digitalisation? Is it possible to design hydraulic elements fit for Industry 4.0?
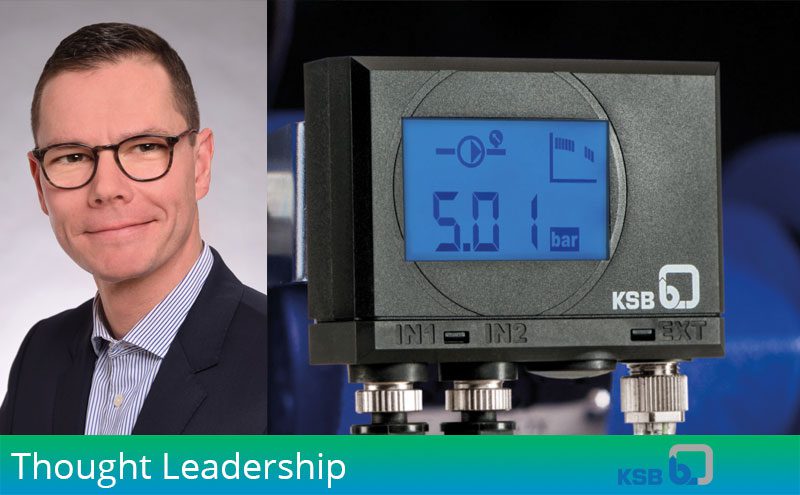
Daniel Gontermann
KSB Drives and Mechatronic Solutions
www.ksb.com
KSB has always focused primarily on optimisation of pumps. The sheer number of different pump casings, materials and impeller adjustment options available confirms this. However, conditions can change during the pumps life, it often no longer runs at the optimum operating point. For years, KSB experts have been investigating ways to optimise pumps more easily without using complex analytics or having to replace the pump.
Digitalisation offers tremendous potential for this, however, it takes time to develop. “It requires transferring decades of experience and expertise into an algorithm and a software solution,” explains Dr Thomas Paulus, Head of Programme Office Digitalisation & Startup Projects at KSB. “This cannot be done in a single step: it involves many different components and aspects. By bringing these component parts together, you end up with an intelligent and practical concept that provides real added value for the pump operator.”
Step 1 – The Digital Monitoring Unit
The KSB “PumpMeter” monitoring unit shows in plain language what goes on inside a pump. With pressure sensors and an analysing display unit fitted to the pump, suction and discharge pressures are measured around the clock. The PumpMeter uses this data to calculate the differential pressure and determines the current operating point, updated in real time.
A typical four-quadrant pump characteristic curve shows the pump operating range at a point in time. This display allows the operator to evaluate the operating point upon start-up and adjust the pump accordingly. Operators see at a glance whether the availability of their pumps is at risk and whether they are operating economically or if there is potential for significant energy savings.
Step 2 – Algorithms to Interpret Vibration Characteristics
In the future, instead of using wetted sensors, it will be possible to record vibrations and transfer this data to the cloud using mobile communication. This has two advantages:
Conventional measurements are not always straightforward, particularly when pumped medium is a chemical product.
With cloud access, technicians can obtain information about the pump status anywhere in the world without being on site.
This application is currently being piloted successfully with 100 selected partners. Measurements taken in parallel using PumpMeter are being used to verify the values from vibration sensors, while the KSB team is continuing to optimise the underlying algorithms. According to Dr Paulus: “From these results, it is already easy to see whether it makes sense to switch to closed-loop control, change operation modes, or replace the pump.” The data is transferred to the cloud via a portal. KSB processes the data, the user receives an automatically generated PDF with clear recommendations and improvement suggestions for the pump.
Step 3 – Operating Point Optimisation with MyFlow
How can these improvement suggestions be actioned? What if it were possible to adjust the pump using software instead of adjusting the impeller manually?
“This is possible with our MyFlow Technology,” says Daniel Gontermann, Head of Product Management – Drives and Mechatronic Solutions at KSB. With a combination of the KSB SuPremE IE5 motor and MyFlow Drive, the conventional approach for fixed speed pumps of trimming the impeller to match the operating point gives way to adjustment by changing the speed.
MyFlow Technology offers many advantages in day-to-day work. Because the operating voltage of the IE5 synchronous reluctance motor is modulated by the minimum frequency inverter mounted on the motor, it can be used in almost any power grid around the world, global engineering contractors no longer need to consider the local mains voltage when selecting pumps. Direction of rotation is now defined at the factory, saving time and costs of conventional direction-of-rotation checks.
Step 4 – Software-Controlled Pump Adjustment
“Although these advantages make the pump operator’s job much easier, they are not enough to make a pump fit for Industry 4.0,” acknowledges Daniel Gontermann. “Nevertheless, they form the basis for the next crucial step: pump optimisation using virtual impeller trimming.”
During it’s life cycle, the pump speed can be adjusted to individual requirements – pump optimisation with virtual impeller trimming, fast and convenient by smartphone or tablet. “A software application is used to bring the pump closer to its optimum operating point,” says the pump specialist. No interruption of operating process, quick, economical energy efficiency optimization if the Q/H point deviates from design values, reaction to system-induced operating point changes. “Because speed change brings power change, substantial savings can be made”
“During development, attention was paid to security. The KSB FlowManager app establishes point-to-point connection, ensuring the correct pump is addressed, only by the authorized person” says Daniel Gontermann.
“The great thing is, you can now defer the individualisation of the pump to a much later point in the supply chain.” Another aspect likely to play a role in future pump selection is, with individual fixed speed adjustment, fewer pump sizes now cover the entire selection chart – efficiency and NPSH values remaining practically constant. Variant complexity for hydraulics is reduced by more than 50%, saving time and money on design and administration. “Simply reducing complexity with fewer variants will promote virtual impeller trimming,” continues Daniel Gontermann.
Outlook
Original equipment manufacturers (OEMs) will benefit from the new opportunities presented by digitalisation, being able to drastically reduce their stock, for example. While this shows the direction in which pump technology will move, “Digitalisation is not an end in itself,” emphasises Dr Paulus. “Users will only accept new technologies if they bring added value to their day-to-day work and are workable.” This is one of the greatest challenges. It is useful that KSB set out on the road to digital future early. “In the way we have been getting the most from pumps in performance and efficiency for decades, we are now also making progress developing algorithms and software. Without our many years of pump expertise, it would be impossible to make a pump fit for the Industry 4.0 era.”
Sponsored article