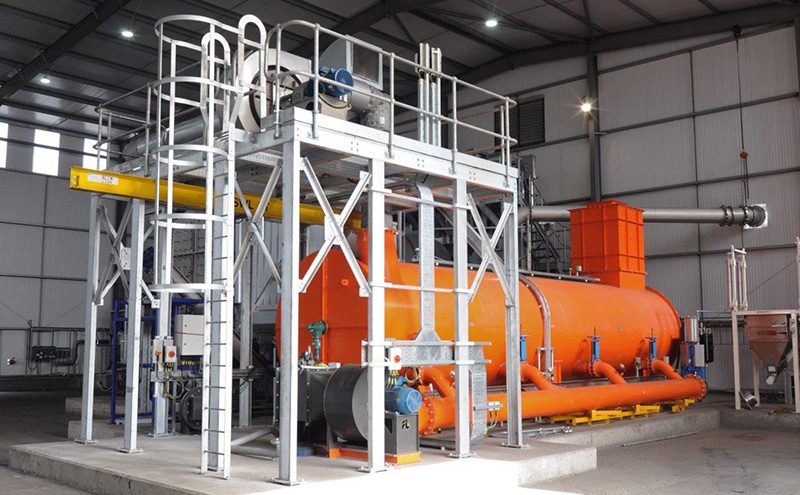
Wigan-based supplier of activated carbons, mobile carbon filtration systems and spent carbon reactivation services, CPL Activated Carbons, has dramatically increased its capacity for reactivating ‘amber list’ spent carbons from industrial purification processes, following a major expansion at its Immingham production facility.
Activated carbons are used in a wide range of gas and liquid phase filtration applications, such as air treatment, water purification and numerous other environmental protection applications. When carbons are ‘spent’ and no longer achieving the required level of filtration, they need to be replaced. In most cases, spent carbons can be regenerated by a process called thermal reactivation, which involves passing the spent media through a high temperature rotary kiln to restore its filtration capability.
Spent activated carbons from the various purification applications are generally categorised into two broad types, which dictates how they are subsequently handled and reprocessed. Spent carbons from industrial applications such as air and biogas filtration, waste water and remediation projects are referred to as ‘amber list’ materials. Carbons that have been used in drinking water or food grade applications are referred to as ‘green list’ materials.
CPL’s carbon regeneration facility is located at the group’s UK manufacturing site in Immingham, Lincs., where it has been successfully reactivating ‘amber list’ spent carbon filtration media from industrial applications since 2013.
Following a major investment by the parent organisation, CPL Industries, the company has dramatically increased its capacity for treating these ‘amber list’ spent carbons, with the installation of a brand-new, state-of-the-art rotary kiln at the Immingham site. The kiln, which is the largest ‘amber list’ regeneration facility in the UK, and one of the largest in Europe, has a sophisticated thermal oxidiser and scrubber system to ensure full environmental protection and compliance.
Commenting on the expansion, CPL’s Divisional Director Steve Bell commented, “After proving our capability in this sector since we started reactivating carbons back in 2013, it is great to complete this next phase in our growth strategy with the installation of this very impressive new kiln. It has three times the capacity of the previous unit and can regenerate spent granular and pellet carbons with a high loading of contaminants. Its sophisticated scrubbing system ensures it is an environmentally friendly process. 2018 has been an exciting year for CPL Activated Carbons, with the start-up of our ‘green list’ reactivation kiln earlier in the summer, and the ongoing growth of our mobile carbon filter fleet and engineering capability. The expansion of our amber list carbon regeneration capacity puts us in a very strong position to take the business forwards and benefit from the increasing demand for our environmental purification solutions.”
The benefits of reactivating spent carbon, rather than disposing of it and replacing it with virgin material, are considerable, in terms of both cost and environmental impact. CPL Activated Carbons believes strongly in the recycling of spent carbons wherever possible.