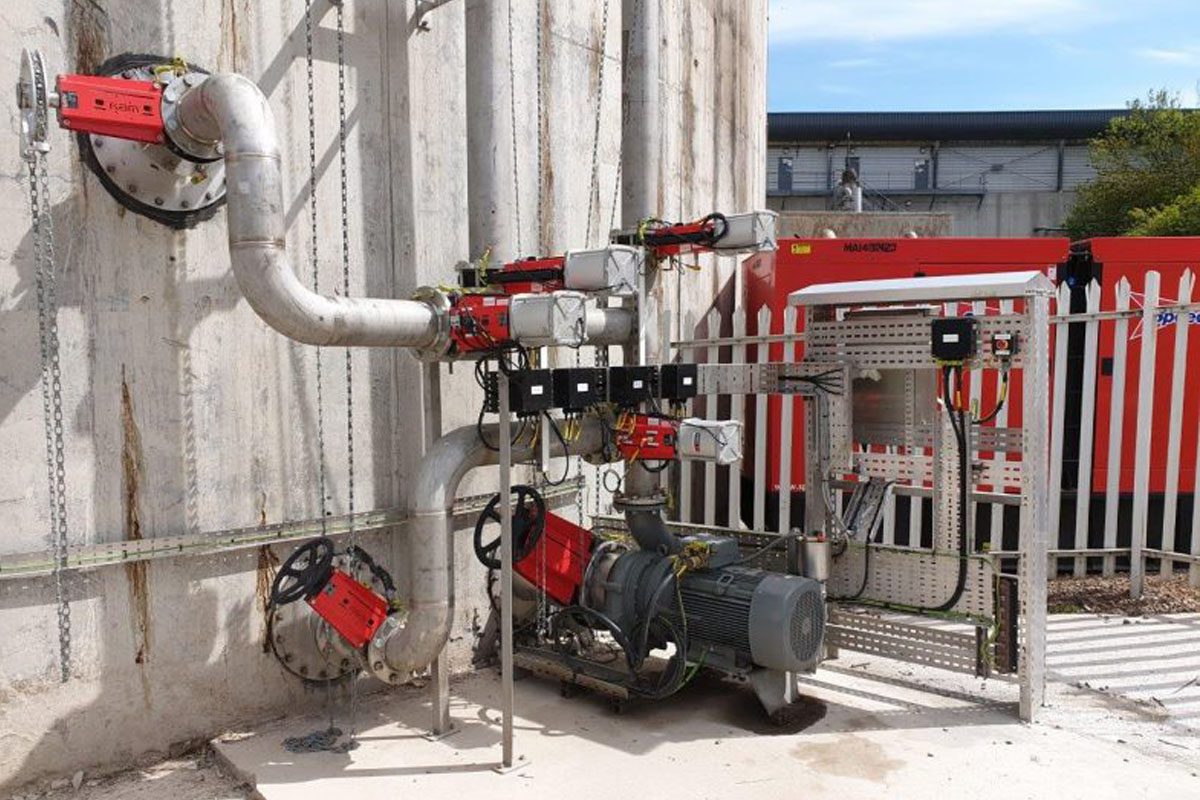
The anaerobic digestion of sludge for energy generation is a process whose efficiency depends to a great extent on the degree to which the solids in question can be thoroughly mixed. All kinds of tank configurations and mixing approaches are in use, but these vary across a spectrum of sophistication and efficiency. Pumps specialist Landia has recently retrofitted its GasMix digester mixing system to a legacy AD tank at Scottish Water’s Nigg treatment works in Aberdeen, achieving substantial energy savings. Given the great number of such legacy AD tanks in use today, the quantities of available energy could be considered “a sleeping giant” of the sector – given the potential to unlock it with a simple retrofit, as Landia suggests. Envirotec asked Landia about the practicalities of this kind of work.
Dissatisfaction with the existing mixing system seems to have prompted Scottish Water’s search for alternatives. The AD tanks at Nigg were only mixing in one plane. Landia’s guarantee to provide “a fully mixed tank” is an unusual and eye-catching claim in this sector.
Landia cites a key advantage for GasMix in the superior chopping and mixing action provided by its pumps. This “unique macerating action” is combined with a process of gas purging and stirring. The system provides a three-dimensional mixing pattern, which prevents clogging of pipes and nozzles.
Landia’s Paul Davies speaks about the limitations of other mixing systems. Some modern installations take the gas and bubble it through an array of diffusers, but the bubbles take the easy route to the surface, leaving columns of relatively unmixed digestate. None combine the benefits offered by GasMix, says Landia.
How it works
The GasMix system combines a biogas digester, apirating stirrer and mixing system – all based on the firm’s long-established “chopper” pump. When fitted to the side of an AD tank, it draws in reactor sludge at a low level of the tank, and ejects the macerated material back into the tank through a jet nozzle. This mixing stage alternates with a biogas injection stage (the “GasMix” stage). A simple Venturi suction process operates here, recirculating the biogas and providing additional mixing, and breaking up any “crust” that might form on the surface of the reactor liquor. By breaking down the cell walls of any organic material, it seemingly facilitates a speedier gas release.
This process of progressive cell breakdown and gas recirculation helps maximise biogas yield, says Landia – one of the key benefits cited for using the GasMix system
Repair and maintenance
The costs of maintenance associated with many AD mixing systems has been a bugbear traditionally given the fact that moving parts tend to be located inside the tank. Decommisioning a digester can run into the tens of thousands of pounds, so the fact that Landia’s GasMix locates all the moving and serviceable parts outside the tank is an important cost saver that the company is keen to highlight. The parts in question are ground mounted, which dispenses with the need for repair personnel to get on top of the tank or access areas of it via ladders and so on – all of which can be a liability in health and safety terms.
At Nigg, GasMix has been installed on two partly underground, cast in-situ digesters measuring 17 x 20m. Each digester is fitted with two diametrically opposite Landia chopper pumps. Landia has carried out this kind of retrofit on tanks “of all shapes and sizes”, says Davies, including those made from steel, concrete and precaste panels. So it offers a lot of flexibility over other systems, he says, which tend to be designed for one system only.
Power is also said to be a key advantage of GasMix and in applications like these it can permit the use of lower power pumps – they are only “on” for limited periods. And this can provide a significant cost saving. Two 30kW units are being installed on each 4,000m3 digester at Nigg. A larger diameter tank might have thre or four, says Davies.
This provides power equivalent to 15W/m3 – considered very economical. And when factoring in the reduced running times – which can be as low as 20 minutes in the hour – the energy savings can seemingly be substantial.
But perhaps “best of all” is the additional concentrations of biogas generated by this mixing process – which the firm cites as 10% and beyond, and the potential basis this provides for “a real big change for the water industry”.