In the following article, Josh Thomas from instrumentation specialist Ashtead Technology, discusses the risks associated with dust at quarries, and highlights the vital role of monitoring.
Almost all quarrying operations have the potential to create dust. Control measures should therefore be established to prevent the generation of levels that cause harm. These measures should be identified in the health and safety document, and measurements should be taken to monitor exposure and demonstrate the effectiveness of controls.
Many minerals contain high levels of silica, so quarrying activities of these materials generate silica dust known as respirable crystalline silica (RCS) and particular care must be taken to control exposure. Guidance is available from the HSE; see document HS(G) 73 Respirable crystalline silica at quarries. Sandstone, gravel and flint typically contain over 70% crystalline silica, shale contains over 40% and granite can contain up to 30%. Inhaling RCS can lead to silicosis which is a serious and irreversible lung disease that can cause permanent disablement and early death. There is an increased risk of lung cancer in workers who have silicosis, and it can also be the cause of chronic obstructive pulmonary disease (COPD).
The Control of Substances Hazardous to Health Regulations 2002 (COSHH) requires employers to ensure that exposure is prevented or, where this is not reasonably practicable, adequately controlled. The COSHH definition of a substance hazardous to health includes dust of any kind when present at a concentration in air equal to or greater than 10 mg/m3 8-hour time-weighted average of inhalable dust, or 4 mg/m3 8-hour TWA of respirable dust. This means that any dust will be subject to COSHH if people are exposed to dust above these levels. Some dusts have been assigned specific workplace exposure limits (WELs) and exposure to these must comply with the appropriate limits. For example, the WEL for RCS is 0.1 mg/m3 8-hour TWA.
The Quarries Regulations 1999 cover all surface mineral workings, and include tips and stockpiles, as well as areas used for crushing, screening, washing, drying and bagging. Buildings and other structures are also included, as are common areas and prospecting sites. The Regulations were created to protect the health and safety of quarry staff, as well as others that may be affected by quarrying activities, such as those living, passing or working nearby, or visiting the site.
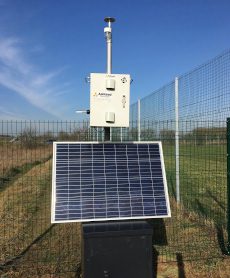
The role of monitoring
In order to assess the risks posed by dust, it is necessary to undertake both workplace monitoring – inside buildings, vehicle cabs etc., as well as environmental monitoring in and around the quarry. The technology for doing so is similar but different instruments are available for every application. Ashtead supplies personal air sampling pumps when it is necessary to conduct compliance monitoring, or when the identification and measurement (in a laboratory) of a specific dust type, such as RCS, is required.
Once the dust risks at a quarry have been assessed, ongoing monitoring is more often conducted with direct reading instruments that employ optical techniques to measure the different particulate fractions. Portable battery-powered instruments such as the TSI SidePak and the DustTrak are ideal for this purpose and feature heavily in Ashtead’s fleet of instruments for both sale and rental.
The same dust monitoring technology is employed by the TSI DustTrak Environmental (DTE), which has been developed specifically for applications such as dust monitoring at quarries. Fully compliant with stringent MCERTS performance requirements, the DTE employs a ‘cloud’ based data management system, which provides users with easy access to real-time data on dust levels, with the optional addition of other sensors. Alarm conditions can be set by users so that text and email alerts are issued when threshold levels arise. The DTE monitors PMTotal, PM10, PM2.5 and PM1.0 mass fractions simultaneously, which provides detailed information on the type of dust present, and means that alarms can be set for specific fractions.
Clearly, dust monitors can perform a vital role in helping to protect safety at working quarries. However, a TSI DTE was recently hired from Ashtead Technology to perform monitoring prior to the commencement of quarrying operations, so that baseline dust levels could be established for comparison once the quarry is operational. Monitoring prior to operations is important, because airborne dust at a quarry is not necessarily derived from the quarry alone; local agricultural or industrial activities may also contribute to the particulate burden. This also highlights the advantages of 24/7 monitoring because dust pollution may be intermittent, so continuous monitors such as the DTE are able to identify peaks and thereby assist in the attribution of sources.
Ashtead Technology fitted the DTE mentioned above with a solar panel and rechargeable battery so that it could operate unattended for extended periods in a remote location. With web-based access to the data, site visits were minimised and costs lowered. This equipment was hired from Ashtead to avoid capital expenditure, and looking forward, the client is planning to add a Lufft wind monitor to the rental, because data on wind speed and direction helps with modelling and with the identification of dust pollution sources.
Ideally, quarry site monitoring should be undertaken prior to the commencement of operations to establish baseline levels for that site. Risk assessments can then be undertaken around the site and within buildings and vehicles/machinery. However, conditions can change significantly, so continuous monitoring is preferable. Changes in quarry practices and weather can affect environmental conditions, and workplace exposure can be affected by a wide range of factors such as broken filter bags, spillage, insufficient cleaning, filter blockage and dry (instead of wet) drilling or cutting.
With a variety of applications for dust monitoring, it is important that appropriate technology is employed, so the Ashtead Technology instrument fleet has been developed to meet almost every need, and technical advice is available to help consultants and quarry operators ensure that dust hazards and effectively managed.