A pig farm in North Carolina says it has increased its biogas yields by 10 percent following the installation of new pumps, with improvements to the mixing of feedstock used for anaerobic digestion.

In a bid to reduce its impact on the environment, Butler Farms developed its own pig-manure-powered biogas operation in 2011.
As a contract grower that takes 20,000 pigs per year from their arrival weight of around 40 lbs to their departure size of about 290 lbs, Butler Farms of Lillington (just south of Raleigh) has enough manure to warrant a one-million-gallon storage lagoon turned anaerobic digester (60 ft x 180 ft x 18 ft deep) for the (up to) 10,000 gallons of manure that are produced every day.
“We may have started out in 1994 as a simple generic contract grower”, said owner, Tom Butler, “but starting with improvements through the EPA’s Clean Water Act, we wanted to do whatever we could to lessen our impact on the environment and our community”.
Adopting best management practices for environmental improvements, Butler Farms chose to cover its pig waste lagoon in 2008 so that as well as significantly reducing odours, methane could be safely flared off. Three years later it began to use that methane to run a biogas engine.
“It’s a never-ending learning process”, says Tom. “We’re pig farmers, not engineers or renewables experts, which is why perhaps we didn’t have the best mixing system for a biogas plant”.
Now referring to the old small mixers as ‘eggbeaters’, Tom said that the pressure ratios on the previous set up, plus varying diameters of pipework also put a strain on the biogas engine, but that pump supplier Landia helped to optimize the system.
“Power isn’t always everything”, he continued, “but our first mixers were so undersized. We’ve gone up from around just 10 HP to 60 HP, which means we can now move a million gallons whenever we want to.
He said he is using two Landia Chopper Pumps at the start of the process, “and then just one is sufficient to keep everything moving.”
He added: “This is quite an achievement because our lagoon is rectangular, not round.” But with two nozzles per pump, he said, “we are finally getting everything mixed properly, so its perhaps no surprise that we’re seeing such an increase in methane levels for our biogas plant, which will continue to improve as we fine-tune the operation”.
Butler Farms now generates more electricity than the farm needs through its 180-kW biogas-fueled gen-set, so it has a power purchase agreement to sell the excess renewable energy to its power provider, South River Electric Membership Corp. The farm has also installed 20-kW worth of solar panels; the power from which it too sells back to South River EMC. It also has a 250-kW/735-kWh battery storage system. In addition, a new hydrogen sulphide (H2S) removal cleaning module, which cools and dries methane prior to being used as a fuel for the biogas generator, has been installed.
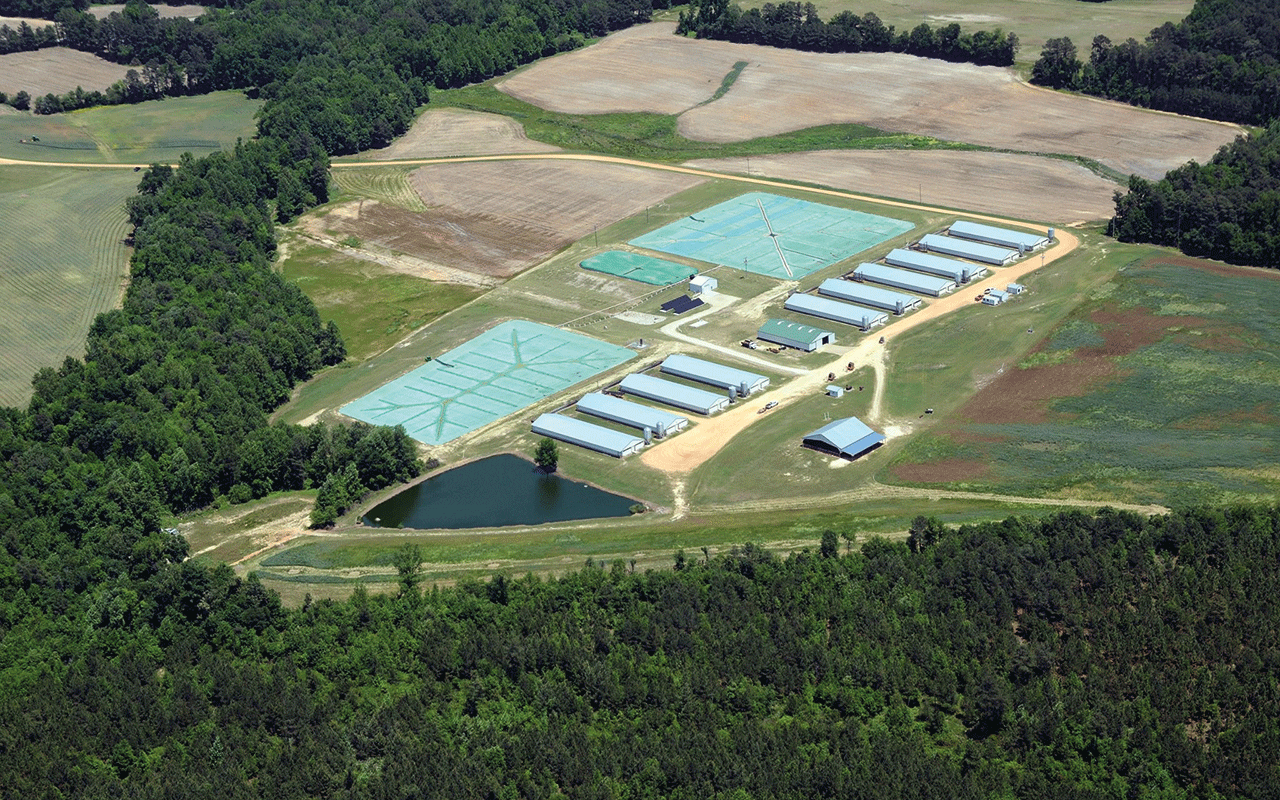
Filling feedstock gaps