
When considering the purchase of a heat exchanger or processing system, there are many considerations to be made, but the follow-up service and aftercare are not always considered, although they are crucial both during delivery and commissioning, but also further into the future.
The term aftercare can be applied to any support obtained from the supplier once the order has been agreed and can therefore include initial start-up services such as commissioning and installation. Depending on the nature and size of the project, these will often be carried out by the supplier in conjunction with the client’s own engineering team and/or third-party contractors. Over the last two years, the Coronavirus pandemic has seen an increase in the use of IT and communication systems to supervise commissioning remotely, a solution which allows for efficient and timely installation while limiting travel and contact.
While correct installation is essential to increase the lifetime of the system and ensure its correct functioning, there are other support services which clients should expect from their equipment suppliers. These include initial aspects such as the provision of training and documentation for both operation and maintenance.
When equipment is fitted with a remote access and monitoring system, the manufacturer can access key information and metrics and, when necessary, log on and discover any potential issues and quickly identify their resolution. A reputable manufacturer will also offer expert insights into the latest technological advancements that could benefit users’ systems process and operational costs.
When selecting a heat exchanger supplier, it may well also useful to ascertain the range of maintenance services which they can offer to help keep equipment running smoothly, including preventative maintenance and servicing, holding reserved stocks of necessary spare parts, and exchanging components where necessary.
Today’s global business structures mean that the location of manufacturing plants is not an issue when it comes to choosing an equipment supplier, and as such you should look at a supplier’s capabilities to support you both locally and remotely.
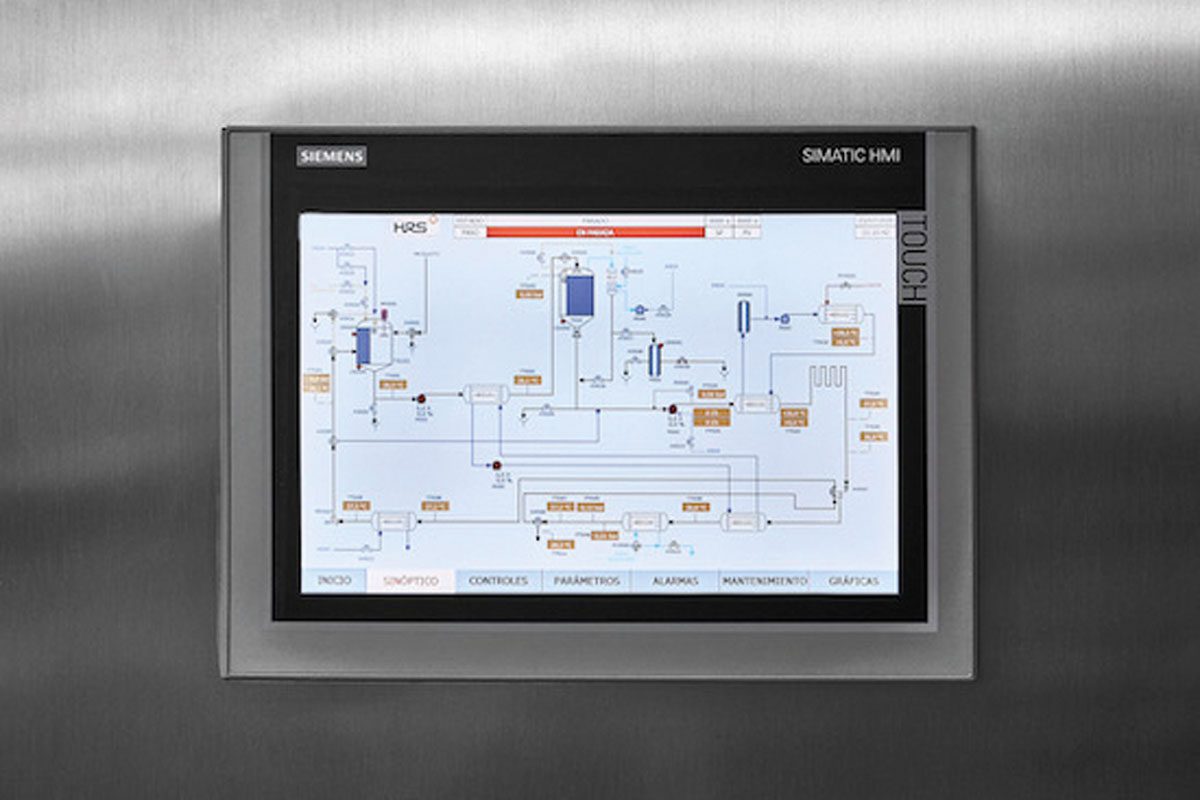