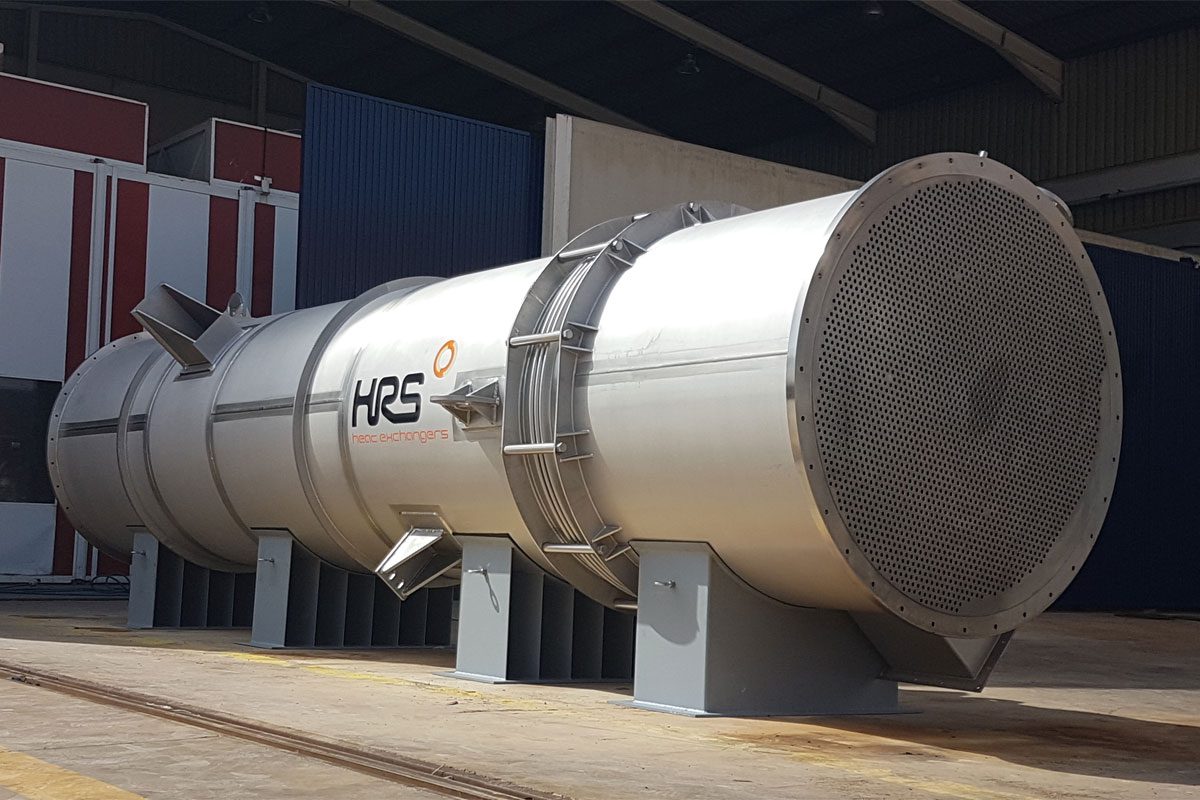
Matt Hale, International Sales & Marketing Director, HRS Heat Exchangers, writes: The biggest efficiency benefits of heat exchangers come about when they facilitate the reuse of as much thermal energy from a process (such as heating, cooling, pasteurisation, evaporation, etc.) as possible.
For example, a pasteurised product is heated then rapidly cooled using two heat exchangers. The first uses hot water to raise the temperature, while the second uses chilled water to cool the product down again. In the second process, the temperature of the cooling water is increased significantly. This heated water can be discarded, cooled again for re-use; or some of the heat it contains can be used towards the heat required for the pasteurisation phase – heat regeneration, reduced the amount of new energy required for the first heating phase.
Many anaerobic digestion (AD) plants use heat exchangers to pasteurise the digestate so it can be sold as an agricultural fertiliser. The ‘surplus’ heat generated by the system is used to preheat the digestate, reducing total heat load and improving overall plant efficiency.
Finally, combining multiple heat exchanges can often provide even greater energy benefits, such as in a multi-effect evaporation system like the HRS DCS Digestate Concentration System. The first stage heats liquid digestate in a cyclone separator; the steam produced from this first cycle or effect is then used as the heating media for the second effect, where the process is repeated. The number of effects is determined by the level of dry solids required and the amount of surplus heat available, up to a maximum of four cycles. After the final stage, the steam is condensed back to water and this heat is used to pre-heat the incoming product before the first stage of evaporation.
